“What is the purpose of DRBFM?”
“What kind of format does it use?”
“Just show me an example already!”
This article is for those who have such questions or concerns.
DRBFM (Design Review Based on Failure Mode) is a framework developed by Toyota Motor Corporation to prevent quality issues before they occur.
Incorporating DRBFM method as part of a Design Review (DR) can enhance your sensitivity to potential quality issues.
In this article, we’ll explain from the basics what DRBFM is, the benefits of using it, and step-by-step instructions for preparing DRFBM sheet, including examples, so even beginners can understand.
If you work in design or production engineering, there’s a high chance you’ll need to apply this in practice. I hope this serves as a helpful reference for everyone!
What is DRBFM?
DRBFM stands for “Design Review Based on Failure Mode“.
In the development of new products or the improvement of existing ones, changes in design or manufacturing processes are inevitable.
As the saying goes, “No evolution without change.”
Without consciously making changes, it is impossible to create better products.
While innovation in product and process design is essential, it is precisely where changes occur that potential quality pitfalls often lie.
DRBFM identifies changes made to the design or process, pinpoints potential issues arising from these changes, and formulates countermeasures.
By addressing risks during the design phase, it effectively prevents quality issues from occurring.
Differences Between DRBFM and FMEA
Another framework for preventing quality issues is FMEA (Failure Mode and Effects Analysis).
FMEA is an analytical method used to rank potential failure modes of a product, visualize the items with the highest scores, and establish strategies or priorities for addressing them.
While both FMEA and DRBFM share the goal of anticipating failure modes in advance, their focus differs. FMEA addresses potential issues broadly, whereas DRBFM specializes in identifying and analyzing specific changes.
In this sense, DRBFM could be described as a “Change-focused FMEA.”
Both methods are crucial for preventing issues before they arise, so it’s best to choose and apply the appropriate one based on your specific objectives.
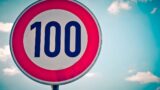
Structure of DRBFM sheet
Below is an example of a DRBFM format.
Breaking Down the DRBFM Structure by Color-Coded Sections.
①: Items Pre-filled by the Design Department (Light Green)
The left side of the sheet is filled out in advance by the design department.
Here, you’ll record:
- The name of the part or process subject to change.
- Details of the change.
- Concerns related to the change.
- Root causes of these concerns.
- Countermeasures implemented at the design stage.
Additionally, you will rank the frequency of potential failures, their severity, and the priority of addressing them.
②: Items Discussed by Reviewers During the Design Review (Yellow)
The yellow sections contain information to be completed during discussions with reviewers at the review stage.
During the design review, reviewers examine the concerns and root causes identified by the design team. If any issues were overlooked, they are added here.
The right side of the sheet is then used to document items that should be incorporated into the design, evaluation, or manufacturing process based on feedback from reviewers.
By pre-filling section ① and discussing section ② during the review, DRBFM clarifies the additional critical actions required.
③: Items for Recording Results of Action Taken (Orange)
The orange section on the far-right side of the sheet is where you document the results and progress of actions taken to address the critical issues identified.
Purpose and Applications
1. Preventing Defects Before Occuring
As its name, “Design Review Based on Failure Mode,” suggests, the primary goal of DRBFM is to assess the validity of product and process designs from a quality assurance perspective.
By proactively identifying risks and addressing them during the design phase, DRBFM helps prevent defects before occuring.
2. Centralized Management of Changes
In traditional design reviews (DR), differences from existing products or processes are typically compared. However, DRBFM is a framework specifically tailored to focus on and organize these changes.
By using the DRBFM format for centralized management, all changes—regardless of their impact—can be comprehensively identified and monitored without omissions.
3. Information Sharing Among Stakeholders
A design review is not just about designers receiving feedback and making improvements. It requires collaboration with other departments to build robust processes.
For example:
- The production department may focus on daily inspections or operator training.
- The quality assurance department may devise measures to prevent defects from escaping.
DRBFM clearly outlines the items that need to be addressed, making it an effective tool for organizing improvement tasks collectively with all stakeholders.
Steps for Preparing DRBFM sheet
Let’s go through the process of preparing DRBFM sheet with an example involving a part where wiring electrodes are deposited onto a ceramic substrate.
The procedure includes identifying changes in both design and manufacturing processes.
Filling Out the Left Side of the Sheet (By the Design Team)
1. Component or Process Name
Begin by noting the name of the part or process undergoing the change.
- If the main focus is design changes, classify by component units for clarity.
- If the focus is process changes, classify by individual processes, as in this example.
- For processes with multiple changes, avoid combining them. Instead, list each change as a separate item.
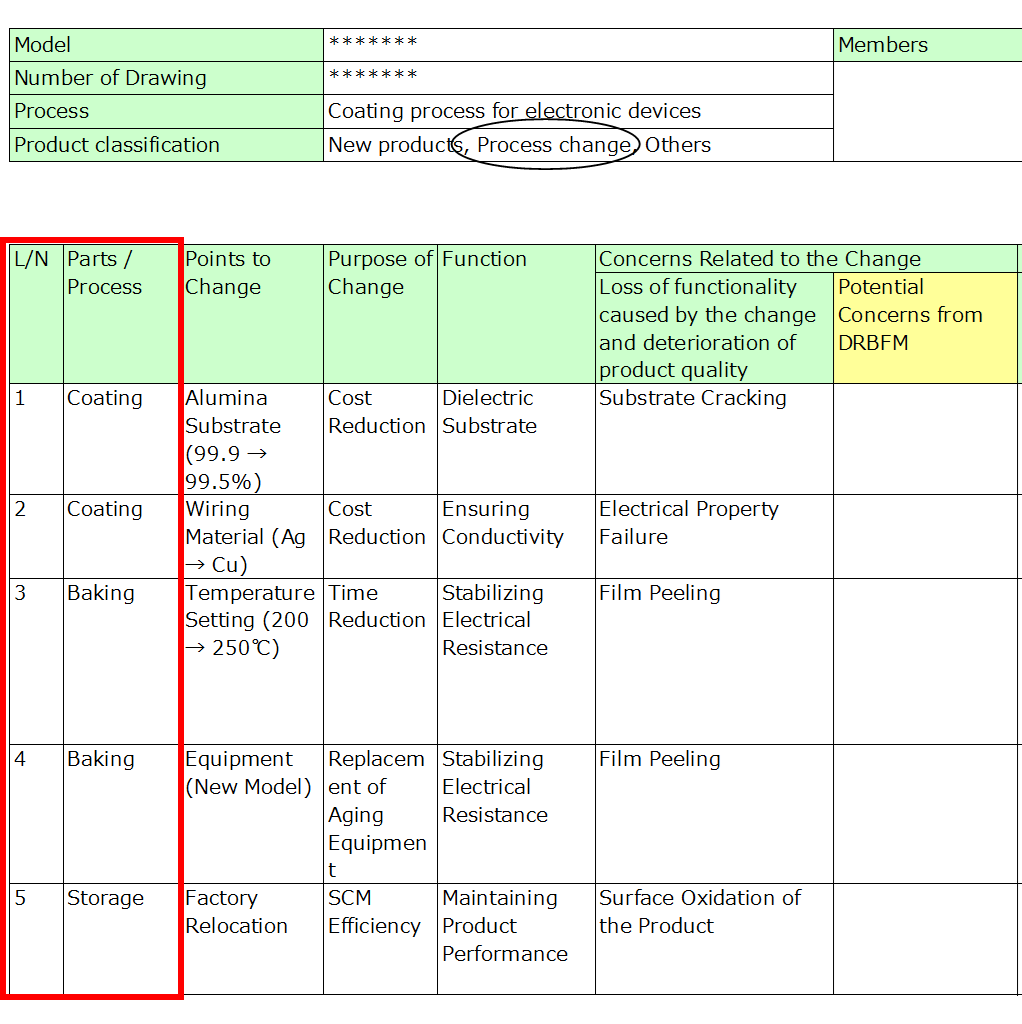
2. Details of the Change, Purpose, and Function
Document the specific changes, their purpose, and the function of the part or process.
- Be specific: Avoid vague terms like “material” or “temperature.” Specify whether temperature is being increased or decreased, as risks vary depending on the direction of change.
- Include the purpose: Clearly stating why the change is needed helps justify its necessity and aids in trade-off decisions if risks outweigh benefits.
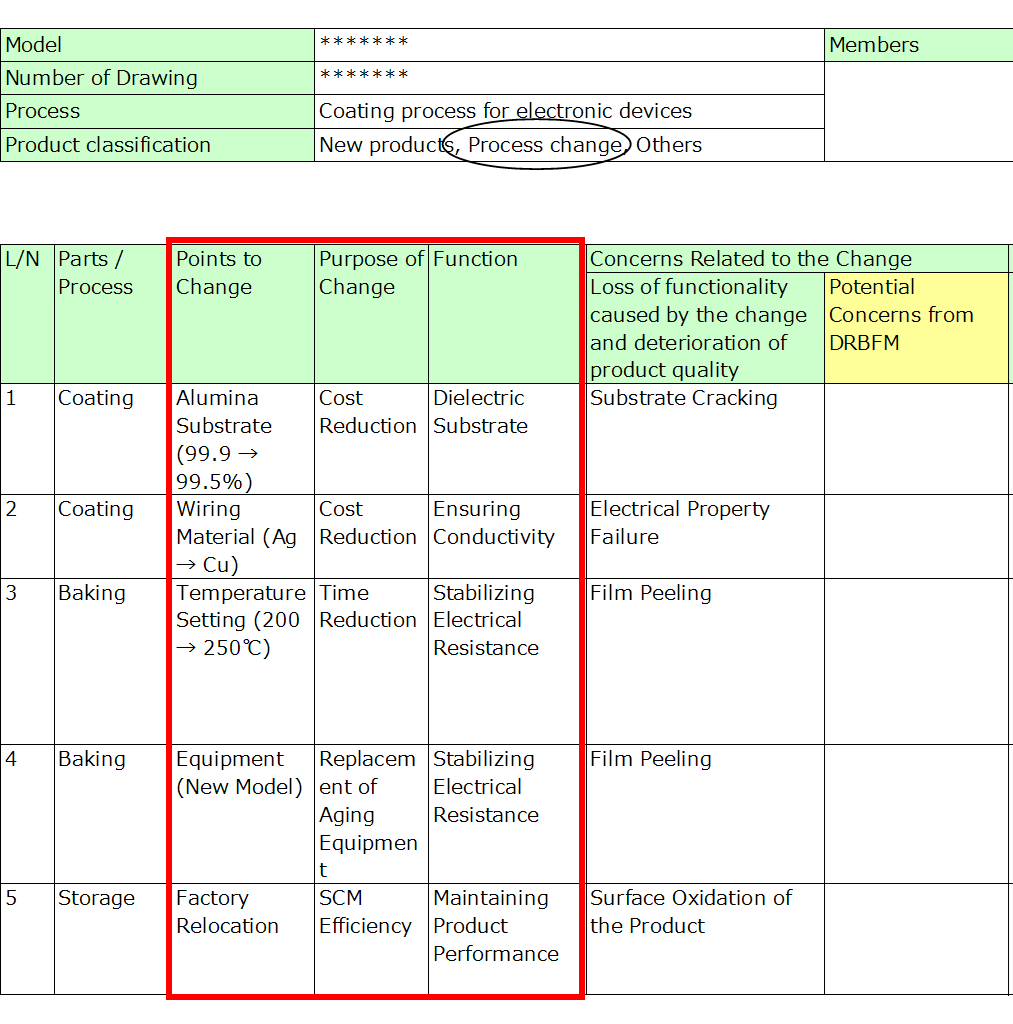
3. Concerns Related to the Change
Identify potential failure modes (risks) arising from the change.
- Be detailed: Rather than general terms like “damage” or “appearance defect,” specify the exact failure mode. This precision supports later analysis of causes.
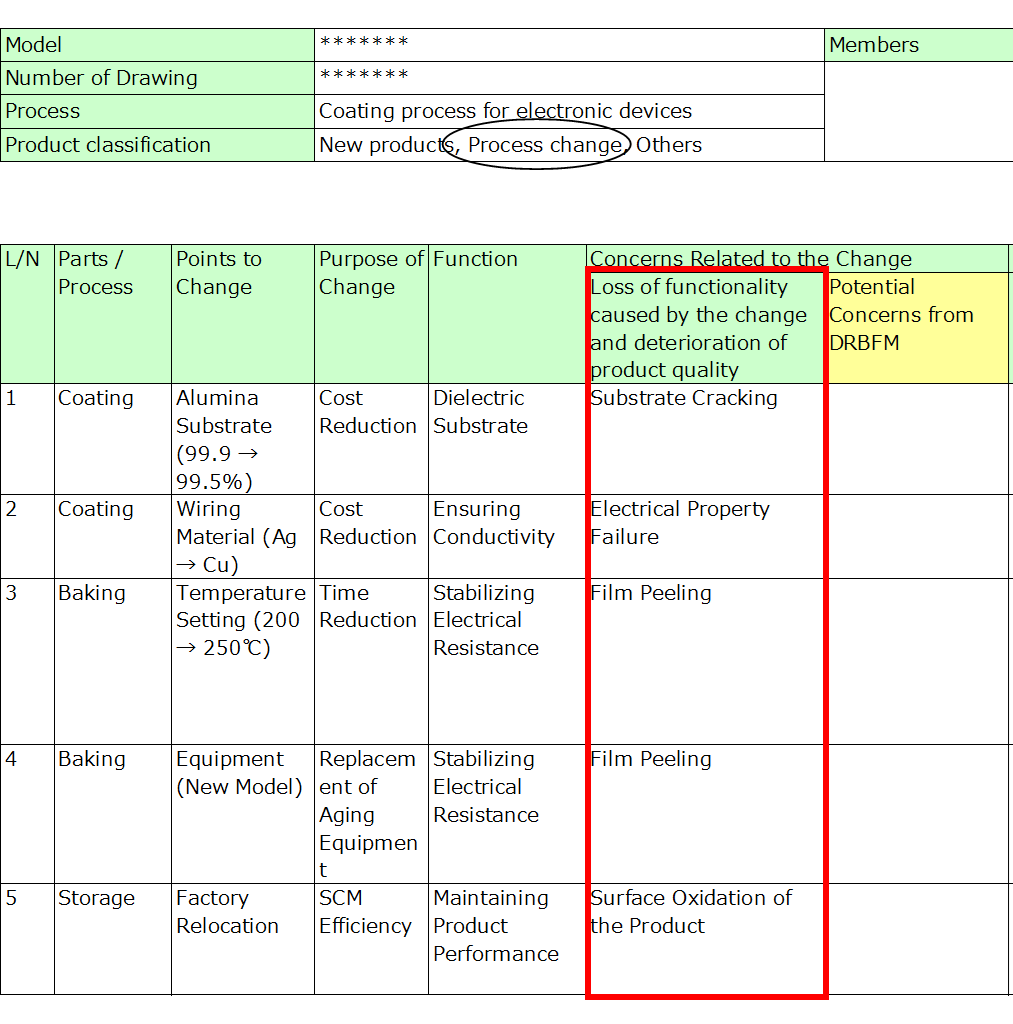
4. Conditions Under Which Concerns Arise
Describe the conditions or root causes under which the identified failure modes might occur.
- Connect these concerns directly to the specific changes made.
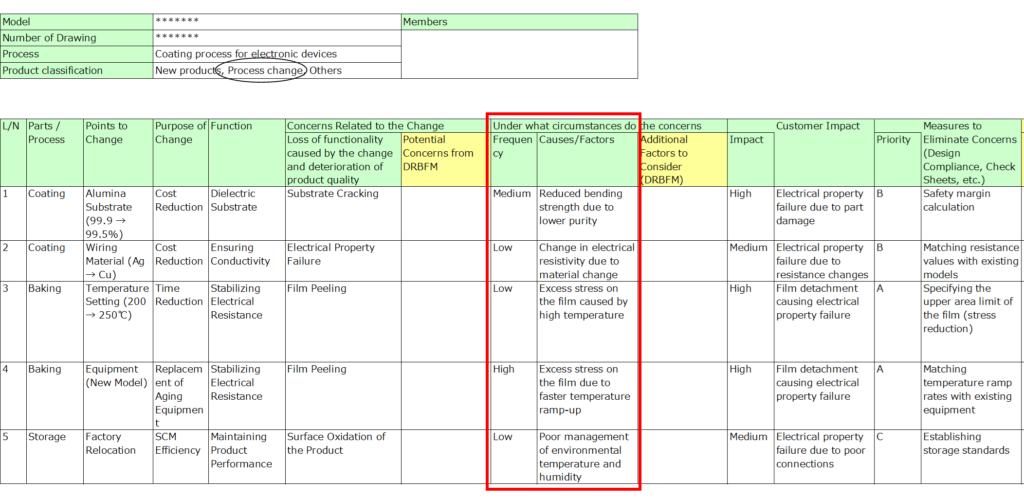
5. Impact on Customers
Evaluate the potential impact of failure on customers, including internal stakeholders if necessary.
- Rank the severity (e.g., high, medium, low).
- If managing downstream processes is critical, adopt the philosophy of “The next process is your customer” to ensure thorough quality management.
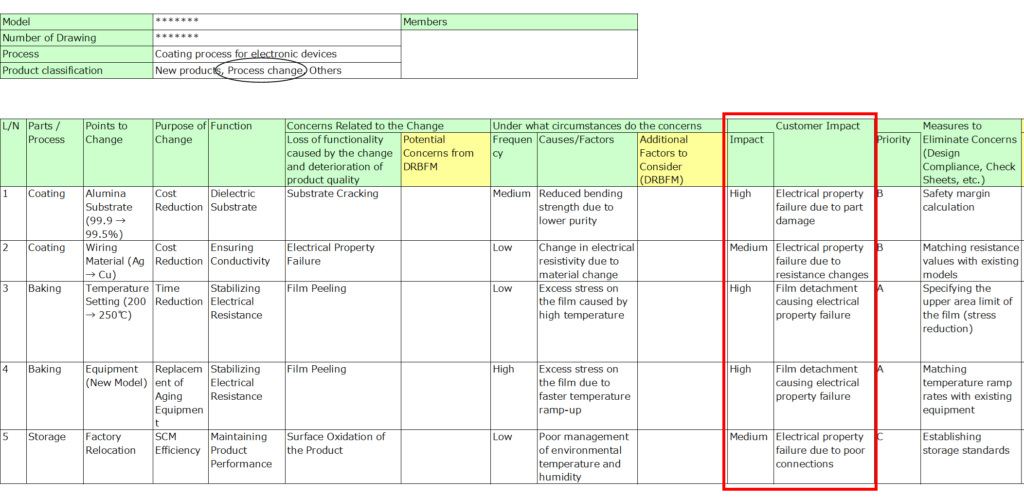
6. Design Measures to Address Concerns
List the measures implemented in the design to mitigate risks, along with their priority.
- Include items like design standards, specifications, or theoretical calculations.
- Robust measures here can reduce the need for additional design reviews or evaluations.
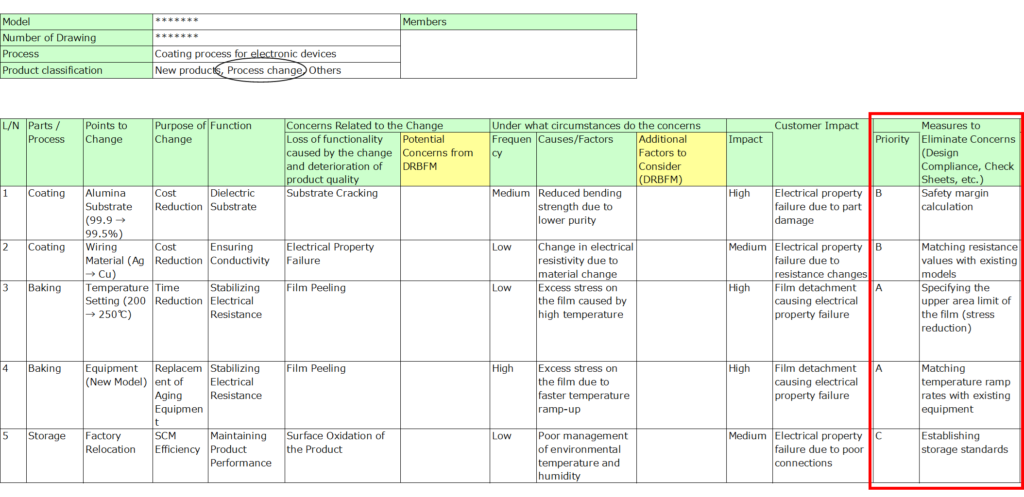
Refining with Reviewers During the Design Review
7. Concerns and Root Causes (DRBFM)
Discuss the concerns and root causes identified by the design team with all reviewers to ensure nothing has been overlooked.
Reviewers from different departments (e.g., inspection, production engineering) can provide diverse perspectives, enriching the analysis.
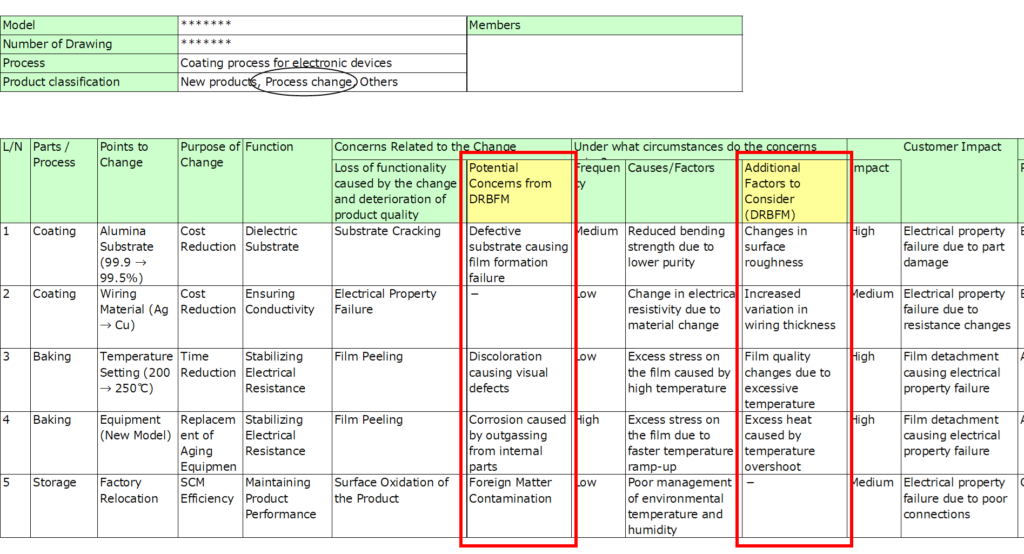
8. Recommended Actions (DRBFM Results)
Organize critical issues into actionable items based on the DRBFM review results.
- Highlight items requiring incorporation into design, evaluation, or process management.
- Assign responsibilities and deadlines for each action.
If the design measures alone are insufficient, additional design reviews or evaluations may be required.
For challenges in ensuring design quality, consider combining process management with quality assurance, which may necessitate further process-level analysis.
Recording the Results of Actions
Finally, document the results and progress of all actions taken.
Once all critical items have been addressed, the conclusion should state that “the quality impact of the changes is minimal,” allowing the changes to be implemented.
By following this systematic approach, DRBFM ensures a comprehensive assessment of risks, proactive measures, and thorough quality assurance throughout the process.
Key Points for Preparing DRBFM sheet
1. Don’t Overlook the “Results of DRBFM”
One common mistake is focusing solely on identifying concerns and their causes while neglecting to extract actionable items from the DRBFM analysis.
- While design-related sections of the form may be meticulously filled, other sections can often be sparse.
- DRBFM is not complete when concerns and causes are listed—it requires follow-through to address gaps in design review and finalize countermeasures for unaddressed risks.
A tight timeline that doesn’t allow for implementing DRBFM findings often indicates a disregard for the process’s importance. Allocate sufficient time to address all necessary actions to fulfill DRBFM’s purpose: preventing defects before they occur.
2. Conduct the Review Across All Departments
Another issue arises when the design team fills out the entire form while other departments merely observe.
- This results in a design-centric perspective, which can miss issues other departments might identify.
- Avoid scenarios where post-implementation complaints such as “this design isn’t manufacturable” or “there wasn’t enough design review” arise. These after-the-fact criticisms are counterproductive.
Engage all relevant departments to incorporate diverse viewpoints and ensure thorough risk analysis.
3. Differentiate Between “Changes” and “Impacts”
The distinction between “changes” and “impacts” is critical in DRBFM.
- Change: An intentional modification made to a product or process.
- Impact: An unintentional effect or alteration caused by a change.
In DRBFM:
- Begin by listing intentional changes made by designers.
- Subsequently, identify potential impacts—unintended alterations that could lead to failure modes—and address them proactively.
Misusing these terms can lead to confusion, so understanding and correctly applying their meanings is essential.
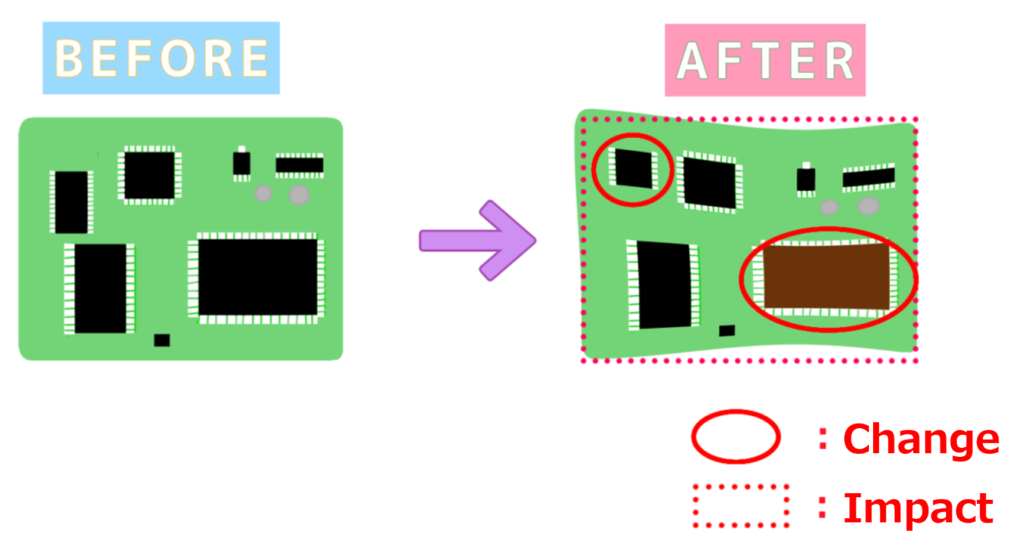
Summary
DRBFM (Design Review Based on Failure Mode):
A methodology for identifying design or process changes, predicting associated risks, and mitigating them during the design phase to eliminate quality issues.
Purpose and Applications:
Prevent defects before they occur.
Centrally manage changes.
Facilitate information sharing across stakeholders.
Steps to Prepare DRBFM sheet:
①: The design team documents changes, concerns, causes, and countermeasures.
②: Reviewers refine the analysis through discussions.
③: Document results and progress for follow-up actions.
Key Points for Success:
・Respect the importance of DRBFM results and allocate sufficient time for actions.
・Involve all relevant departments for a comprehensive review.
・Clearly distinguish between “changes” and “impacts.”
Effective change management is not only crucial for internal reviews but also often required by customers as part of change requests.
By fostering a culture of quality across all departments, your organization can strengthen trust with customers and ensure robust defect prevention.
Thank you for reading!
Be sure to reference the examples provided and put DRBFM into practice effectively.
コメント