This article is for those who want to learn the basics of what a Cause-and-Effect Diagram (Fishbone Chart) is, understand its purpose and the situations in which it can be applied, and learn how to create one with concrete examples.
We’ll explain everything clearly and concisely so you can understand it in just 10 minutes.
Additionally, we’ll provide tips on how to approach creating a cause-and-effect diagram.
If you need this knowledge for your immediate tasks or are struggling with solving specific problems, we encourage you to read through to the end and use it as a reference.
What is a Cause-and-Effect Diagram?
The cause-and-effect diagram, also known as the Ishikawa diagram or fishbone chart, is one of the “Seven Tools of Quality” (QC Seven Tools).
The QC Seven Tools are methods primarily used to efficiently manage quality through statistical data, and they are highly versatile, applicable not just in manufacturing but across various fields. For those involved in quality management, mastering these tools can be incredibly useful.
Example of a Cause-and-Effect Diagram
The diagram resembles the structure of a fish skeleton, which is why it is often called a fishbone chart. Keywords are arranged at the tip of the “head” and at the ends of the “main bones” and “smaller bones.“
Key Components:
- “Effects”: These represent the “outcome” or “result” and are placed in the “head” of the fish. You can think of this as the “problem” to be solved for a clearer image.
- “Causes”: These indicate the “factors” or “reasons” leading to the outcome and are organized along the main bones, middle bones, and smaller bones.
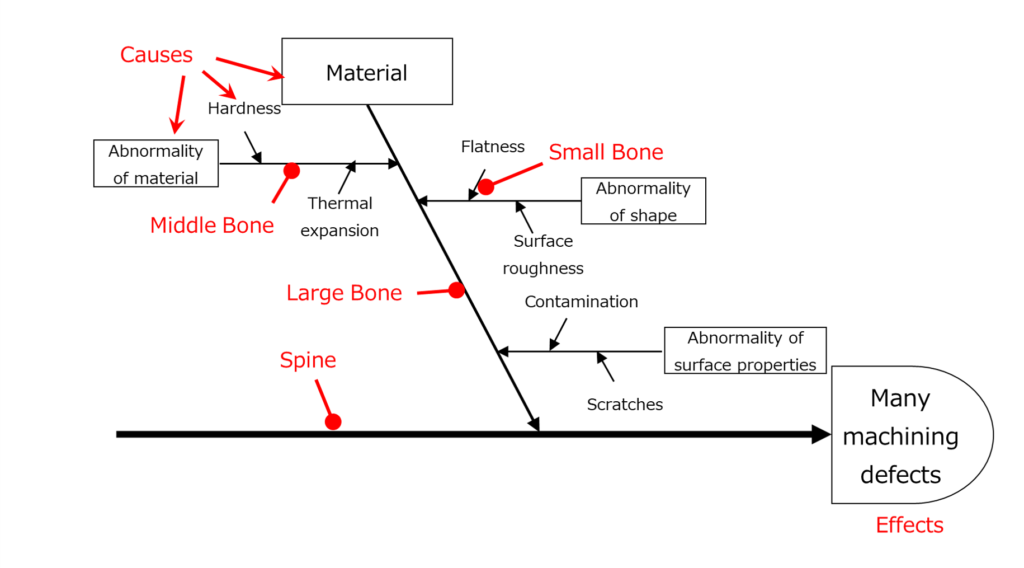
In summary, a cause-and-effect diagram is:
“A systematic visualization of outcomes (characteristics) and their causes (factors).”
Features of the Cause-and-Effect Diagram:
- Visualization for a clear understanding of the overall structure.
- A hierarchical system to comprehensively extract causes.
In its focus on hierarchical classification, the cause-and-effect diagram shares similarities with Fault Tree Analysis (FTA).
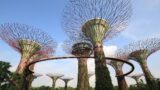
The Relation Diagram Method, part of the “New QC Seven Tools,” is often used in situations with complex interdependencies among factors.
While the Interrelationship Diagram is effective for identifying cause-and-effect relationships in such scenarios, the Cause-and-Effect Diagram is particularly useful when delving deeper into the layers of potential causes by categorizing them hierarchically.
Understanding the strengths of each tool and adapting them to fit the situation will enable more effective problem-solving.
Purpose and Applications
Root Cause Analysis
The cause-and-effect diagram can be effectively utilized for investigating the root causes of defects or problems.
By visualizing and listing potential causes (factors) in a systematic way, this tool allows for:
- A comprehensive investigation of all possible causes.
- Easier prioritization of which causes to address first.
Organizing Problems
By categorizing causes into “main bones” and “smaller bones,” the hierarchical relationships between factors become clearer. This enables a structured and visually clean organization of problems.
The resulting diagram is easy to understand, even for third parties seeing it for the first time. If prepared neatly and systematically, a cause-and-effect diagram can serve as a valuable informational asset for future reference.
Information Sharing
To ensure no potential causes are overlooked, collaborating with colleagues and stakeholders in the workplace is essential.
A practical approach is to start by sketching the results (characteristics) and the “spine” on a whiteboard and then conducting a brainstorming session where everyone contributes ideas.
This approach offers several benefits:
- Raises the overall knowledge level of participants.
- Helps correct any misunderstandings or misalignments within the group.
- Facilitates consensus building and alignment within the organization.
By fostering collaboration, the process not only identifies key factors but also strengthens teamwork and shared understanding within the team.
When Is the Cause-and-Effect Diagram Used?
Using the example of the manufacturing industry, the cause-and-effect diagram is primarily applied in the following scenarios:
- Production Issues: Identifying and addressing the root causes of defects, inefficiencies, or deviations in the production process.
- Quality Management: Improving product quality by analyzing and categorizing potential quality issues.
- Quality Assurance: Ensuring compliance with standards by systematically evaluating factors that could impact quality.
Beyond these areas, the cause-and-effect diagram is widely utilized in other departments as well:
- Planning: Structuring ideas and identifying risks during project planning stages.
- Research and Development: Investigating potential causes of failures or bottlenecks in innovation processes.
- Design: Analyzing factors that may affect functionality, performance, or usability.
- Procurement: Evaluating suppliers and identifying risks in the supply chain.
- Sales: Understanding customer feedback by systematically organizing causes behind issues or complaints.
Its versatility makes it an invaluable tool for professionals across diverse roles, far beyond just manufacturing or quality-related fields.
How to Create a Cause-and-Effect Diagram
The Core Idea Behind the Diagram
If you’re already accustomed to applying logical thinking in your field, you can create a rough draft of a cause-and-effect diagram in about 20–30 minutes.
For those who feel less confident about logical thinking, it might take more time initially to identify causes and organize their relationships. However, there’s no need to worry. The process itself is invaluable.
Think of it as a “decluttering exercise for your mind”—writing down ideas that may previously have been vaguely understood but not explicitly organized.
Benefits of the Process
- It helps you identify gaps in your knowledge, such as missing elements or flawed logic in cause-and-effect relationships.
- Even just recognizing your current level of understanding makes the exercise worthwhile.
At first, focus on organizing your thoughts clearly. It’s fine to take your time. The key is to ensure that you systematically and comprehensively list and organize the causes.
Over time, as you grow accustomed to logical thinking, the process will naturally become faster and more intuitive.
At first, dedicate sufficient time to this process, treating it as an exercise in clarifying and organizing your thoughts.
If you’re familiar with tools like mind mapping, you’ll notice similarities in the thought process. Both approaches aim to visualize information systematically.
Now that you understand the basics, let’s move on to actually creating your diagram!
Steps to Create a Cause-and-Effect Diagram
Let’s create a diagram step by step, using the example of “frequent machining defects in mechanical processing.”
- Define the Problem and Draw the Spine
- Add the Main Causes (Large Bones)
- Add Subcategories (Middle Bones)
- Add Detailed Causes (Small Bones)
Step 1: Define the Problem and Draw the Spine
- Decide on the issue or problem to address (the cause)—in this case, “frequent machining defects.”
- Write it at the rightmost end of the diagram.
- Draw a horizontal thick line extending to the left; this will act as the “spine.”
- Position the spine in the middle of the page to leave enough space above and below for factors to branch out.
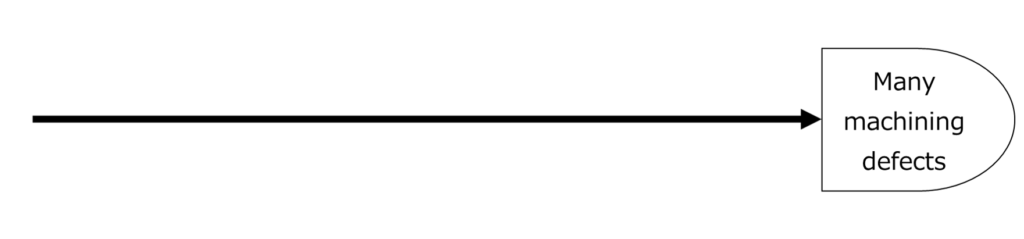
Step 2: Add the Main Causes (Large Bones)
- Identify major categories influencing the problem.
- Add these categories as diagonal lines branching off the spine—these are the large bones.
- Use the 4M framework for categorization:
- Man (People)
- Machine (Equipment)
- Material (Raw materials)
- Method (Processes or techniques)
- Optionally, include Measurement (Inspection) and Environment to form 5M+1E, depending on your needs.
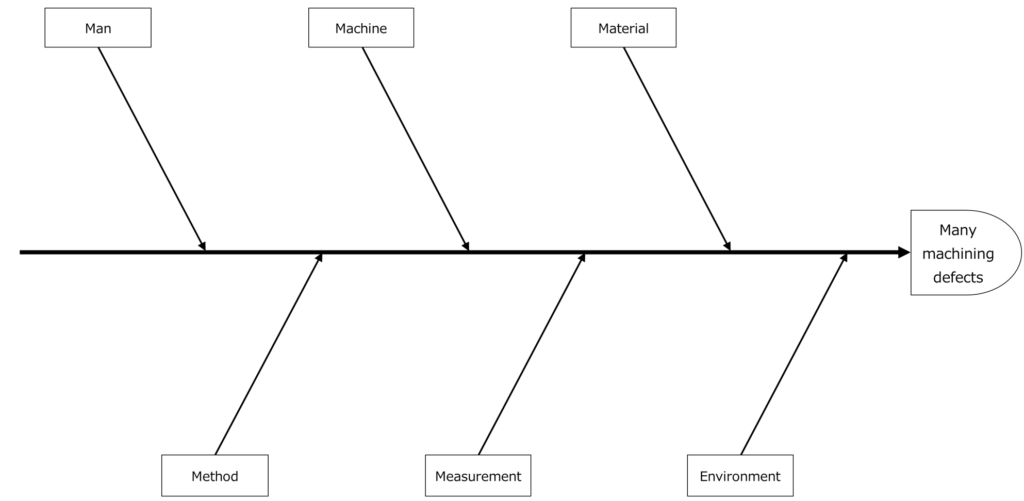
Step 3: Add Subcategories (Middle Bones)
- For each large bone, list more specific factors contributing to the issue as middle bones branching off.
- For example:
- Man: Lack of training, fatigue, communication issues.
- Machine: Malfunction, maintenance issues, calibration errors.
- Material: Low-quality materials, impurities, inappropriate specifications.
- Method: Inefficient processes, outdated techniques, unclear instructions.
- For example:
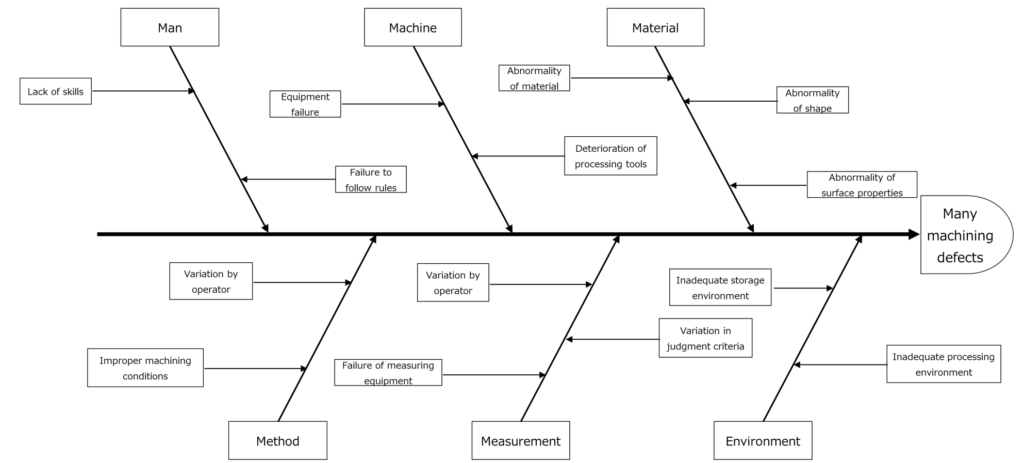
Step 4: Add Detailed Causes (Small Bones)
- For each middle bone, break the causes down further into small bones if needed.
- Example:
- Machine → Malfunction → Worn-out parts or overheating issues.
- Example:
- Continue branching into grandchild bones (smaller branches) if deeper analysis is required.
Final Touches
- Review the diagram for completeness.
- Highlight critical factors that are likely to have the most significant impact on the problem by circling them in red or marking them with symbols.
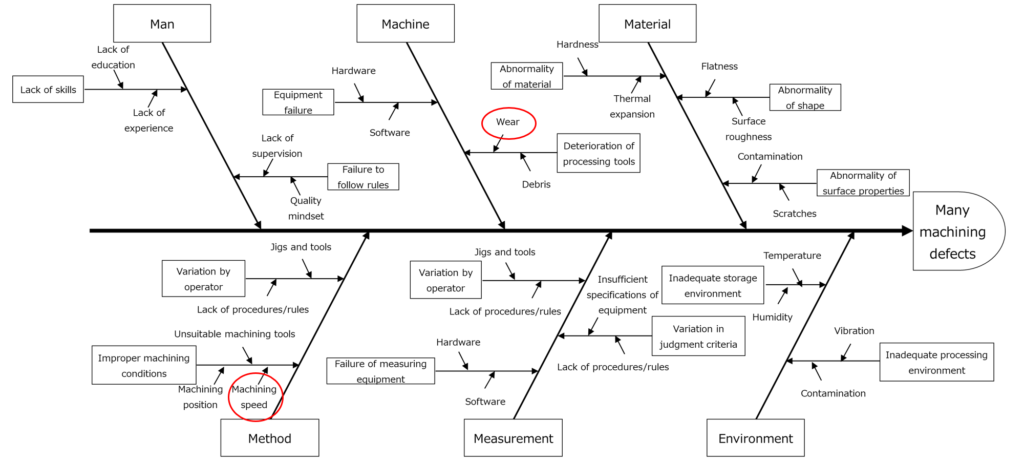
With this, your cause-and-effect diagram is complete!
By following these steps, you systematically identify, categorize, and visualize factors, enabling a comprehensive understanding of the issue at hand.
Key Points for Creating a Cause-and-Effect Diagram
- Classification of Main Causes (Large Bones) is Crucial!
- Don’t Overthink the Hierarchy of Middle and Small Bones
- Use “Why” to Organize Hierarchies
- Link the Diagram to Action
Classification of Main Causes (Large Bones) is Crucial!
The effectiveness of your diagram largely depends on how well you classify the large bones.
While the 4M framework is commonly used, it’s essential to adapt your classification to suit the specific topic.
Examples of Alternative Classifications:
- Case 1: Cost Reduction Initiatives
- Material costs, processing costs, testing/inspection costs, administrative expenses.
- Case 2: Supply Chain Management
- Procurement, manufacturing, sales, logistics.
Proper classification at this stage simplifies the organization of middle bones, makes the diagram visually clean, and reduces the time needed for completion.
Don’t Overthink the Hierarchy of Middle and Small Bones
When extracting causes beyond the large bones, focusing too much on maintaining a perfect hierarchy can limit your ability to identify factors.
Instead, aim to extract all potential causes comprehensively, even if the hierarchy isn’t perfect initially. You can always refine it later.
Use “Why” to Organize Hierarchies
The relationship between causes and effects is built by asking “Why?” repeatedly.
- For every identified factor, ask:
- Why is this happening?
- What is causing this?
- Use these answers to build and refine the hierarchy of causes systematically.
For example:
- Defect → Why? → Machine malfunction → Why? → Worn parts → Why? → Inadequate maintenance schedule.
This process naturally deepens your understanding of the root causes.
Link the Diagram to Action
Remember, creating a cause-and-effect diagram is a means to an end, not the goal itself.
Once the diagram is complete, revisit the original objective (e.g., root cause analysis, information sharing) and take steps to:
- Address the critical causes identified.
- Implement actionable solutions.
- Share insights with relevant teams or stakeholders to drive improvements.
By keeping these points in mind, you’ll create a diagram that not only visualizes the problem but also sets the stage for practical and effective solutions.
Column
The Challenge of Launching a New Process
My first introduction to the cause-and-effect diagram came when I was tasked with starting up a new piece of equipment.
Though I already had experience launching several systems and was familiar with the general process, I initially underestimated the task.
The equipment in question, however, was part of a completely new process with no prior production records or established expertise. The equipment itself was fully customized and unlike anything we’d worked with before.
During the launch, I found myself struggling alone to fine-tune the production parameters. I had no clear understanding of the variables involved, their relationships, or their respective impacts.
Every day became a cycle of blindly changing conditions, testing, failing, and hitting dead ends.
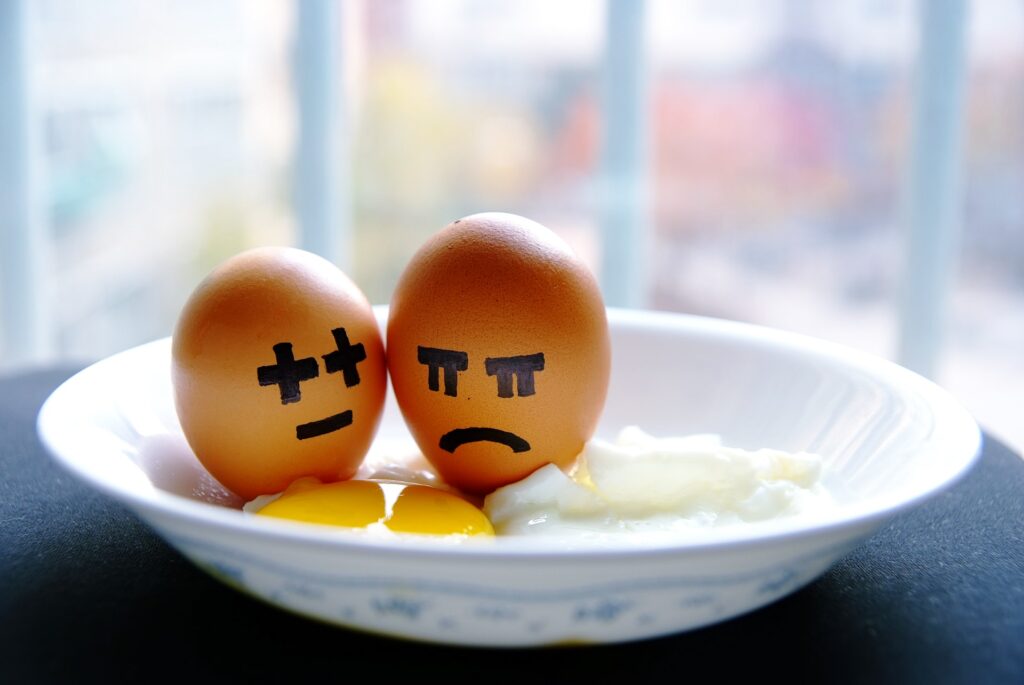
Finding the Cause-and-Effect Diagram
At this point, I came across the concept of the cause-and-effect diagram.
I decided to list out all the equipment parameters and hardware components I could think of and organize them systematically.
While this didn’t magically solve everything overnight, it allowed me to structure the variables and relationships hierarchically. This, in turn, made it much easier to explain the situation to other stakeholders and solicit advice.
Through discussions and feedback, I eventually found a way forward.
Looking Back on My First Diagram
The diagram I created at the time wasn’t perfect. Without any prior training, I relied on online resources and improvised. In hindsight, the structure was far from ideal.
However, the act of organizing my thoughts, identifying cause-and-effect relationships, and presenting them visually was a significant learning experience.
Recommendations for First-Time Users
The cause-and-effect diagram may seem unfamiliar and intimidating at first, but once you try it yourself, you’ll realize it’s not as difficult as it appears.
I highly recommend giving it a shot. Once you’ve created your first diagram, the process will feel much easier the next time around.
This tool not only helps you clarify your understanding of complex systems but also fosters better communication and problem-solving collaboration.
Summary
What is a Cause-and-Effect Diagram?
A tool to systematically organize and visualize results (effects) and their causes.
Purpose, Applications, and Benefits
- Purpose: Root cause analysis, organizing problems, sharing information.
- Benefits:
- Visualizes causes in a hierarchical structure.
- Provides a comprehensive view of the overall situation.
- The process of creating the diagram itself promotes valuable critical thinking.
Getting Started
Start with a simple, real-world problem you want to solve. Experiment with creating a cause-and-effect diagram and experience its benefits firsthand.
Thank you for reading until the end!
コメント