“What types of check sheets are there?”
“Why do we use check sheets?”
“I want to know how to create and use them!”
This article is for those who have these questions or requests. We will explain everything clearly and concisely so you can understand it in just 10 minutes.
We will also discuss what insights can be gained from check sheets and highlight key trends to focus on, using real-life analysis examples. Be sure to read until the end and use it as a reference!
What is Check Sheet?
They are used for data aggregation to create Histogram and Pareto Diagram, as well as for pre-operation inspections of equipment.
There is no fixed format for check sheets; they are often customized to fit specific purposes.
For example, they are commonly seen in everyday situations such as inspection checklists for apartment viewings or restroom cleaning checks.
Why Use Check Sheet?
Purpose and Applications
Check sheets can be categorized into two main types based on their purpose: “Survey & Recording Check Sheets” and “Inspection & Verification Check Sheets.”
Survey & Recording Check Sheets
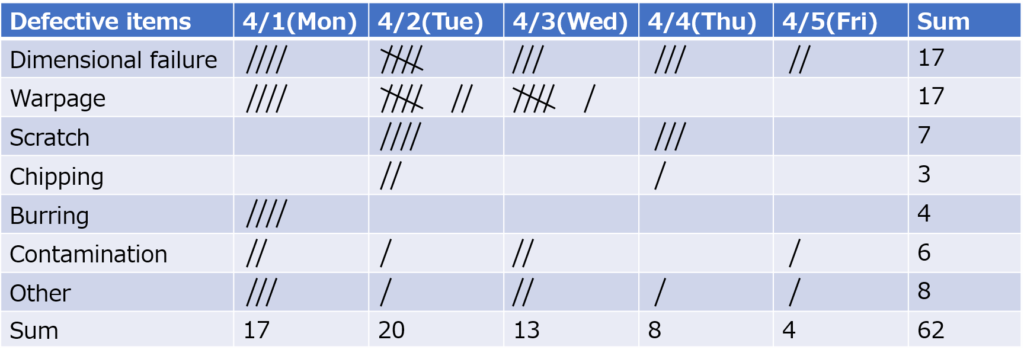
- These sheets classify data into categories and record occurrences by counting them.
- Once the data is aggregated, it can be viewed as a table to identify overall trends.
Inspection & Verification Check Sheets
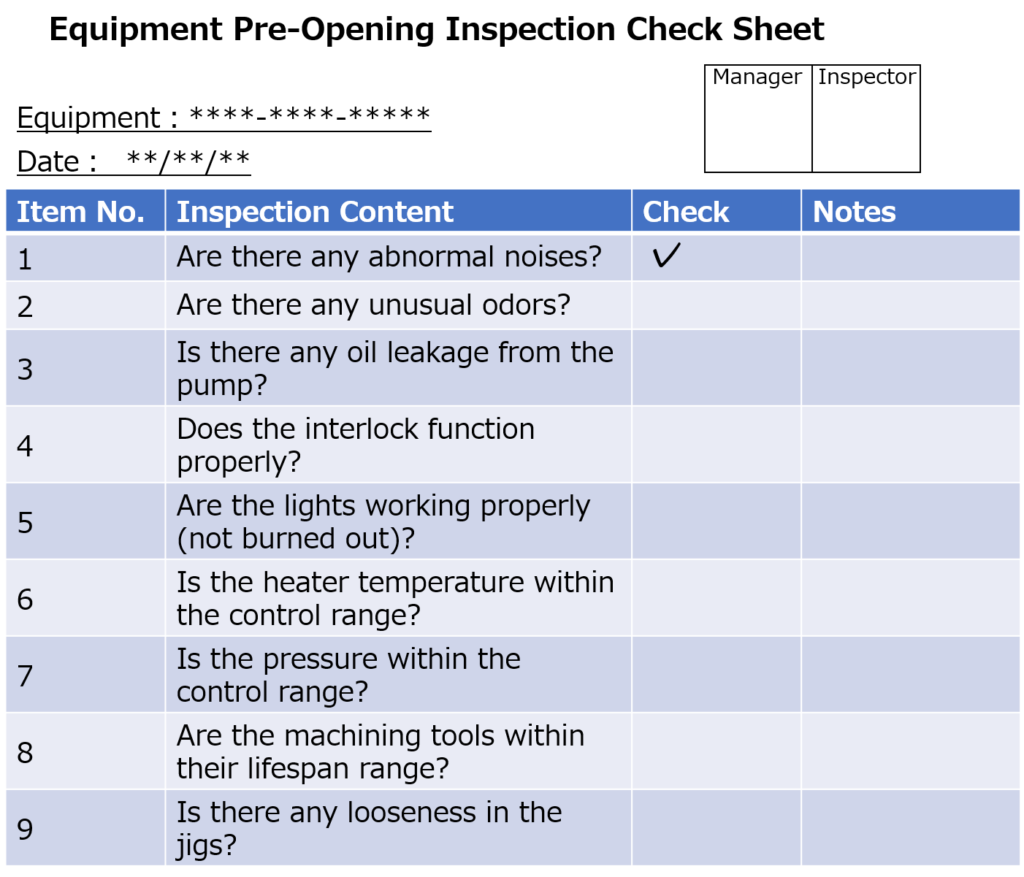
- Used for performance checks of equipment, safety inspections in workplaces.
- Items are pre-listed, and checks are made by marking each item.
- These sheets can also be stored as inspection records.
Benefits
Simplified Record-Keeping
- Pre-listing items streamlines the recording process, reducing workload and saving time.
Efficient Data Analysis
- Visualizing data in a table format makes it easier to identify issues and trends.
Standardized Evaluation Criteria
- Predetermined inspection criteria ensure consistent evaluations.
- Helps prevent missing important verification steps.
How to Create a Check Sheet
- Define the Purpose
- Determine the Check Items
- Design the Format
- Test & Improve the Sheet
Define the Purpose
First, clearly identify the purpose of the check sheet.
For example, if you are creating a survey check sheet, simply collecting data without a clear goal won’t yield useful insights. Instead, determine whether you want to identify trends for improvement or streamline data collection, as this will influence the format and structure of the sheet.
Determine the Check Items
Decide what information is necessary to achieve your goal.
When investigating defects, listing every tiny detail isn’t always effective—too much detail can make it harder to recognize trends.
For example, if you want to understand the main causes of defects, you might categorize them based on the 4M method:
- Man (People)
- Machine (Equipment)
- Material (Materials)
- Method (Processes)
Grouping issues under these broad categories makes it easier to identify key problem areas and take targeted action.
Design the Format
Create a structured format that includes all necessary check items.
Make sure the time frame for data collection is appropriate. For instance, if you want to analyze weekly trends, a format covering Monday to Friday on a single sheet will make it easier to spot patterns.
Test & Improve the Sheet
Conduct a trial run in the actual work environment and identify areas for improvement.
Usability issues often become apparent only after real-world use. Once a draft version is ready, test it in practice and refine it as needed for better efficiency and effectiveness.
Examples of Check Sheet Applications
Survey & recording check sheets are used for various purposes. Here are some key applications:
- Nonconformity Cause Investigation
- Nonconformity Location Investigation
- Frequency Distribution Investigation
Nonconformity Cause Investigation
This type of check sheet records the occurrence of defects by category.
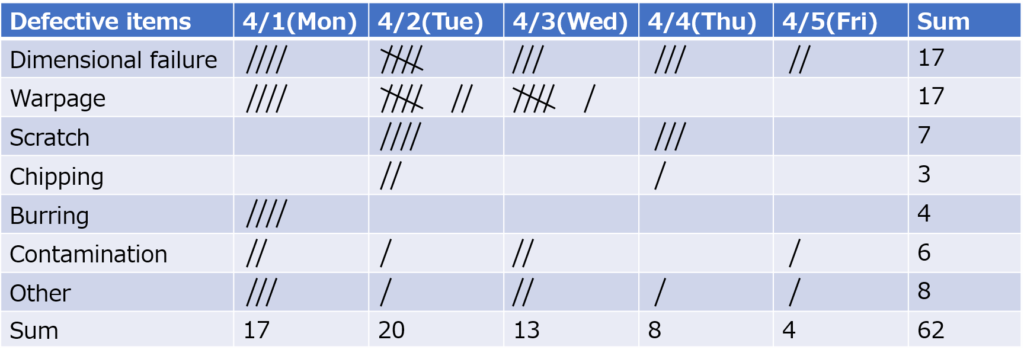
- It helps determine what happened, when, and how often it occurred.
- Useful for understanding defect trends and identifying areas for improvement.
Nonconformity Location Investigation
Used when a more detailed analysis of a specific issue is needed.
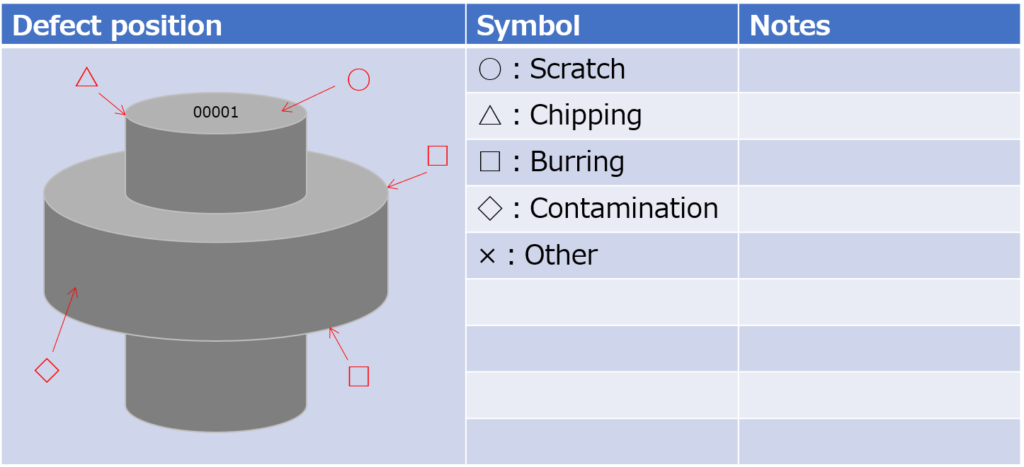
- Particularly effective for investigating appearance defects or other specific failure modes before conducting a root cause analysis.
- Records where, what, and how often a defect occurs.
- Often includes schematic diagrams to visualize defect locations in detail.
Frequency Distribution Investigation
This check sheet is used to count occurrences within predefined categories.
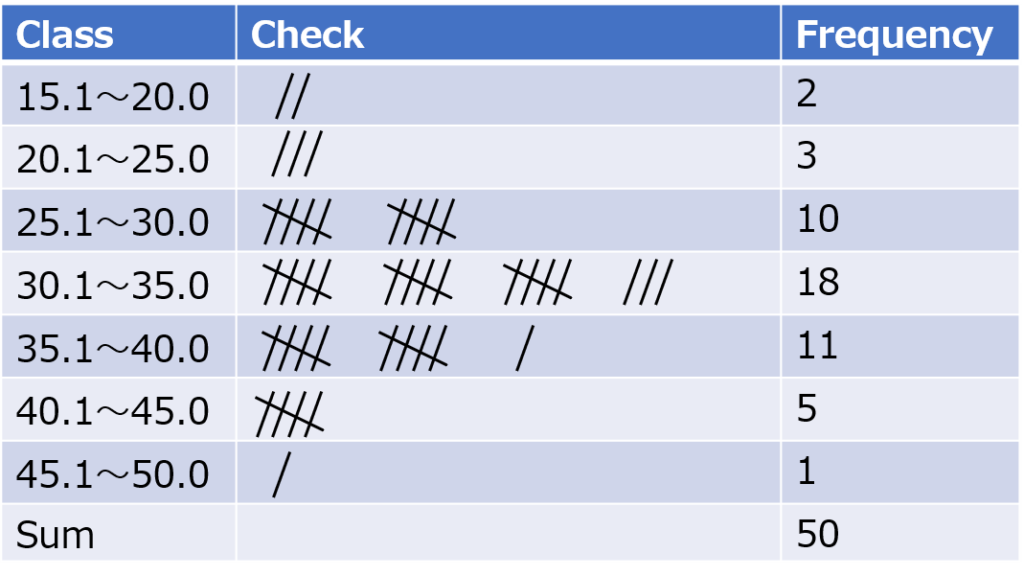
- Helps analyze data distribution and trends.
- Organizing data in columns based on time periods (e.g., daily, weekly) allows for tracking distribution changes over time.
Let’s Analyze the Data
So far, we have discussed the types and creation of check sheets. Now, let’s take it a step further by analyzing defect causes using a real case study.
Suppose we have gathered the following data from a survey check sheet.
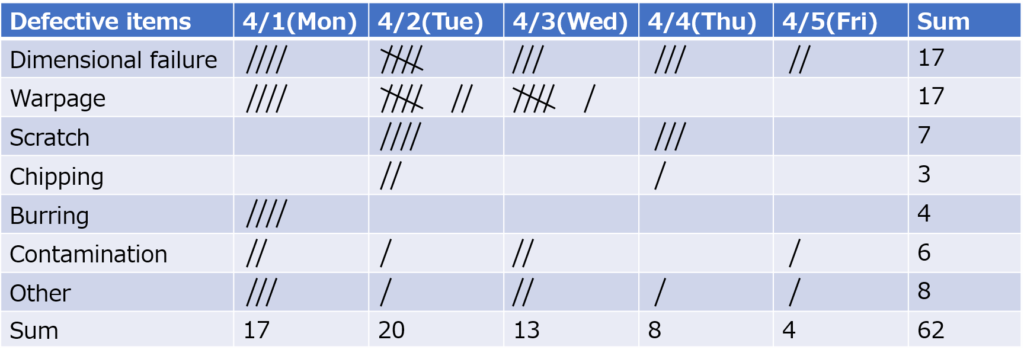
What insights can we draw from it?
Let’s consider four key perspectives:
- Focus on Time-Based Trends
- Focus on Trend Changes
- Focus on Sudden Anomalies
- Focus on Consistent Patterns
Focus on Time-Based Trends
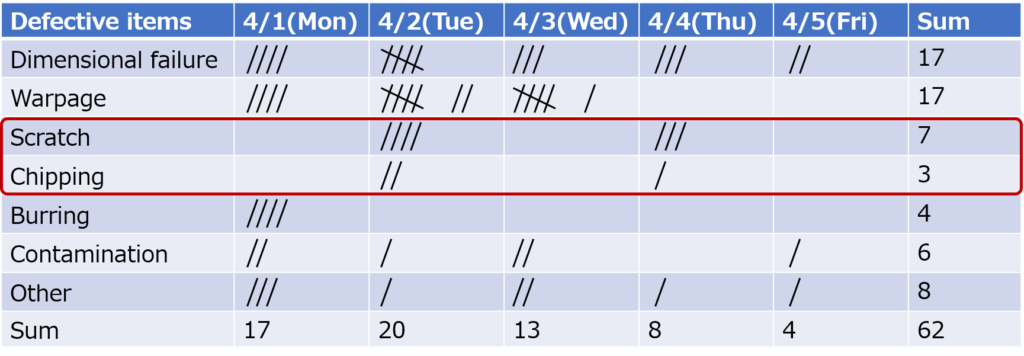
- Observation: Defects such as scratches or chips occur on specific days.
- Analysis: Investigate potential causes related to these specific days, such as worker shift schedules or other periodic influences.
Focus on Trend Changes
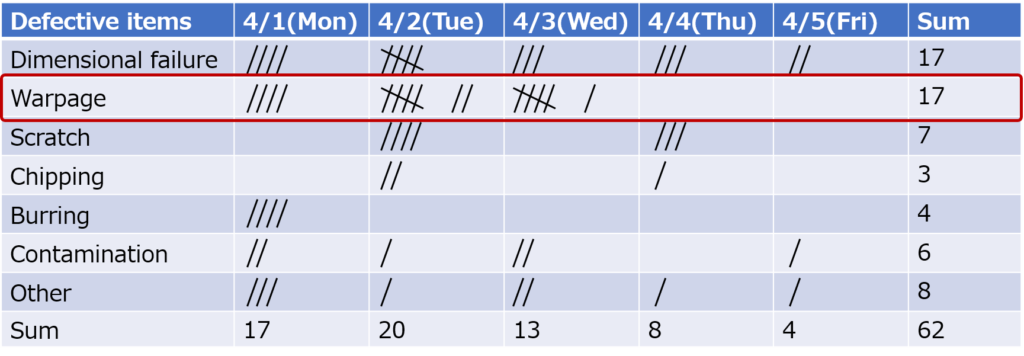
- Observation: Warping defects suddenly stopped occurring after a certain day.
- Analysis: Examine factors that might have changed over time, such as a new batch of materials or an adjustment in production processes.
Focus on Sudden Anomalies
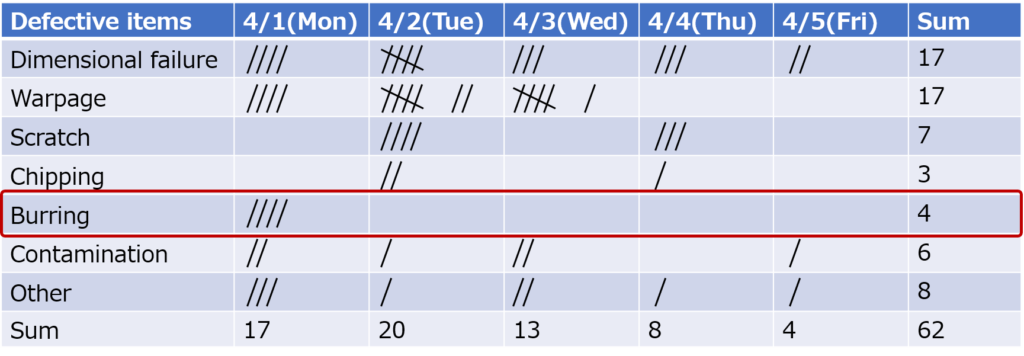
- Observation: Burr defects appeared only on a single day.
- Analysis: Look into temporary issues, such as inadequate warm-up of machinery at the start of the week or a one-time equipment malfunction.
Focus on Consistent Patterns
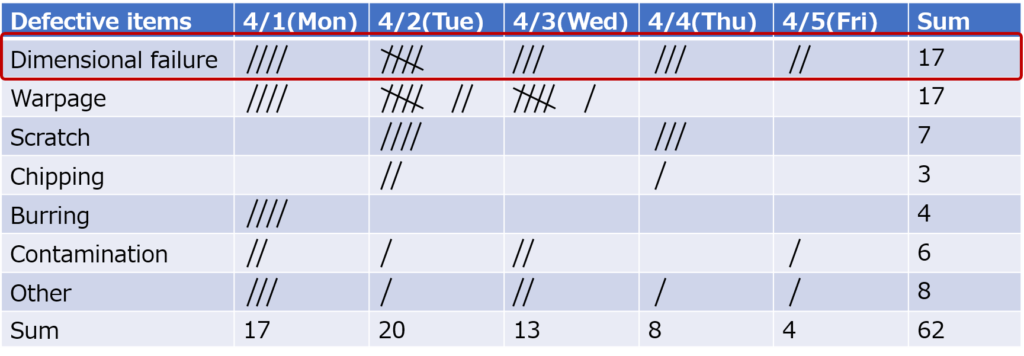
- Observation: Dimensional defects occur continuously.
- Analysis: This may indicate an underlying issue with processing conditions. It may be necessary to review and adjust baseline production parameters.
As seen in these examples, check sheet data reveals valuable insights. By carefully examining trends and anomalies, you can uncover hidden clues for process improvements. Keep refining your analysis to drive effective corrective actions!
Column
Initial Low Expectations
The analysis examples I shared earlier are based on my own past experience. Looking back, I can now highlight key takeaways, but to be honest, my approach at the time was far from ideal—it was more of a bad example.
Initially, my goal in creating a check sheet was simply to reduce defects in a given process, but I lacked a clear strategy. To be honest, I didn’t have high expectations and was merely staring at the collected data without much thought.
As a result, I didn’t start with a well-defined objective, analyze the data effectively, or implement targeted countermeasures. Unsurprisingly, the investigation ended without yielding any useful insights, and the situation remained unchanged. The problem was put on hold, and we continued to struggle with poor yield rates.
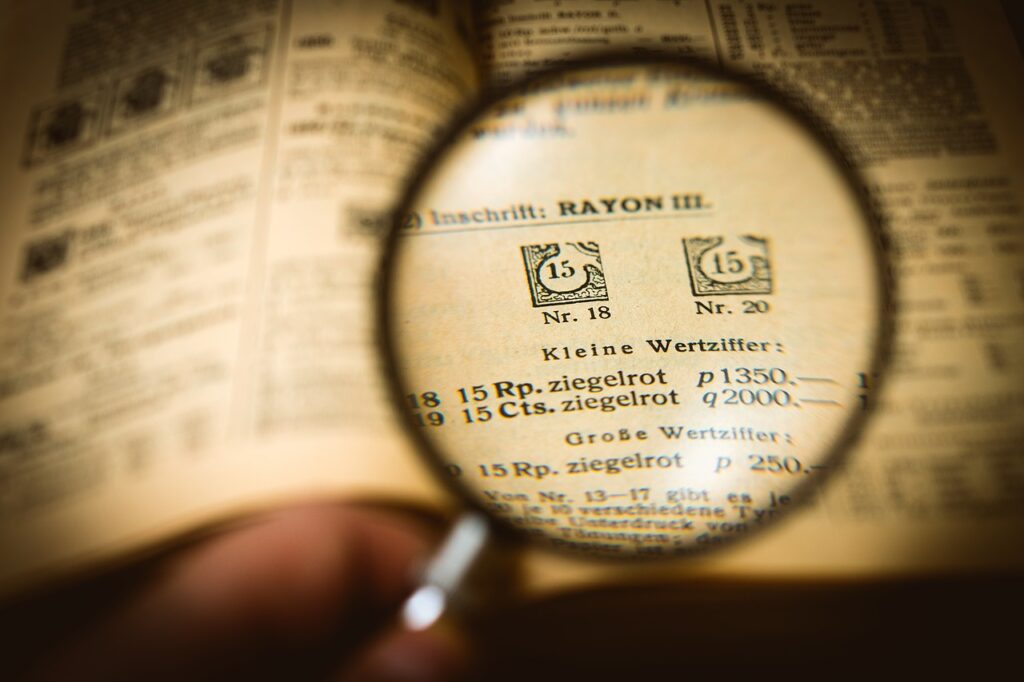
Unexpected Insights
Later, when we restarted the investigation more seriously—this time with advice from colleagues—we revisited the old data. That’s when we finally saw meaningful patterns.
By looking at time trends, changes in tendencies, and sudden occurrences, we started noticing hidden consistencies in the data. The moment we identified regular patterns, we could begin to analyze potential causes, leading to a clearer understanding of the situation.
Using these insights, we developed countermeasures and continued making improvements. Eventually, we successfully achieved our target yield rate.
The True Purpose of a Check Sheet
The goal isn’t just to create a check sheet—it’s about extracting valuable insights from it.
This applies to any analytical tool: if you approach it half-heartedly, you won’t gain anything. If you simply follow instructions without genuine curiosity, you’ll miss potential discoveries.
Try comparing different data periods or analyzing variations between production lines—experiment from multiple angles. Even if you find just one useful hint, it makes the effort worthwhile!
Summary
Types of Check Sheets
Survey & Recording Check Sheets – Used for classifying and recording data for analysis.
Inspection & Verification Check Sheets – Used for safety checks, equipment inspections, and standard compliance.
Benefits
✔ Simplifies Record-Keeping – Reduces manual work and improves efficiency.
✔ Efficient Data Analysis – Helps visualize trends and identify issues.
✔ Standardizes Evaluation Criteria – Ensures consistent assessments and prevents oversights.
Key Analysis Points
Focus on Time-Based Trends – Identify patterns tied to specific dates or shifts.
Focus on Trend Changes – Investigate sudden improvements or worsening conditions.
Focus on Sudden Anomalies – Look for unexpected one-time occurrences and their causes.
Focus on Consistent Patterns – Persistent issues may indicate fundamental process flaws.
Manufacturing challenges vary case by case. As you implement check sheets, refine them based on real-world usage, and develop a format that best suits your needs!
コメント