「特性要因図とは何なのか基本から教えてほしい」
「どういう目的でどのような場面で活用するのか知りたい」
「具体例を挙げて作り方を教えてほしい」
このような悩みをお持ちの方に向けた記事です。10分で理解できるよう、わかりやすく簡潔に解説します。
特性要因図を作成するにあたっての考え方のヒントも紹介していますので、直近の業務で必要な方、課題解決の進め方でお困りの方は、ぜひ最後まで読んで参考にしていただければと思います。
また、Youtubeチャンネルでは、この記事の内容をさらに詳しく動画で解説していますので、あわせてご覧いただけると幸いです。
特性要因図とは?
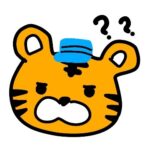
特性?要因? むずかしそう・・
特性要因図は、QC 7つ道具の一つです。
QC 7つ道具とは、主に統計データを用いて品質管理を効率的に行う手法で、製造業だけでなく幅広い分野に使えるので知っておくと非常に便利です。品質管理に従事している方は、使い方もぜひ習得しておきたいですね。
QC 7つ道具の説明や、その他の手法は別の記事で紹介していますので、あわせてご覧ください。
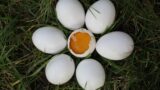
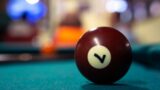
まず、特性要因図の例を以下に示します。
魚の骨の構造をしており、別名でフィッシュボーンチャートとも呼ばれています。
先端の頭の部分と枝分かれした大骨・小骨の末端にキーワードを配置した形となっています。
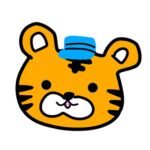
見た目が印象的だね!
「特性」と「要因」って、どういうこと?
「特性」とは、言い換えると「結果」のことで、魚の頭の部分に示す項目です。解決すべき「課題」と考えた方がイメージしやすいかもしれません。
「要因」とは、その名の通り「要因、または原因」を表します。それぞれ、大骨、中骨、小骨に分類して配置します。
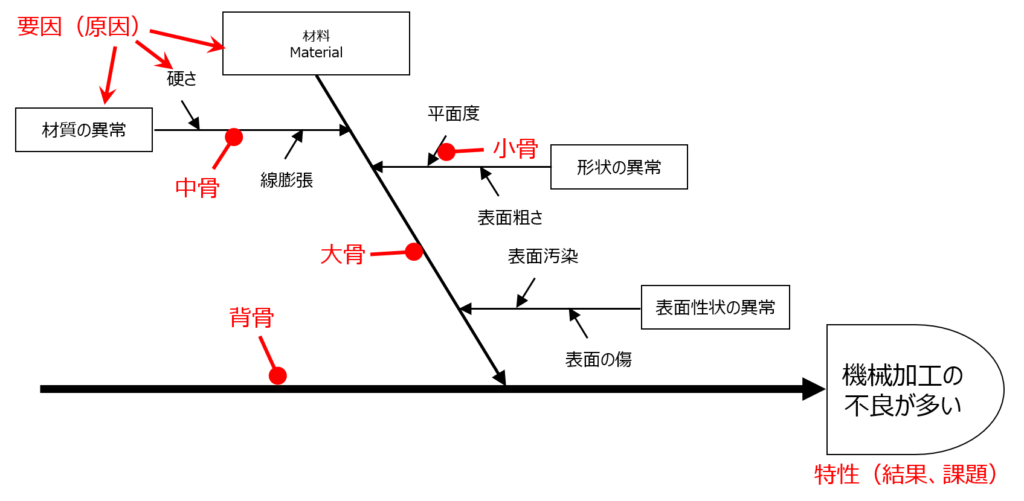
つまり、特性要因図とは
「結果(特性)と原因(要因)を系統的に整理して視覚化したもの」です。
- 視覚化して全体像を把握しやすい
- 階層構造で要因を網羅的に抽出できる
といった特徴がありますね。
要因の階層を分けるという観点では、FTA(故障の木解析:Fault Tree Analysis)と似た性質があります。
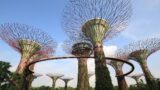
また、新QC7つ道具の連関図法も特性要因図とよく似た考え方で用いられます。
連関図法は、要因どうしの間にも因果関係がある場合など、複雑に関係性が絡み合っている状況で有効に活用できます。
一方、特性要因図は要因を階層別に分類して整理するので、要因を深堀りしていく場合に有効です。
それぞれの特徴を押さえつつ、状況に応じて上手く使い分けられるようにしておくといいですね。
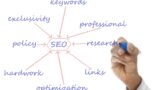
なぜ特性要因図を使うの?
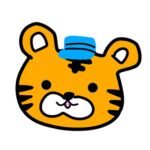
どんな風に役に立つの?
主に次の目的で活用されます。
目的・用途・メリット
- 原因調査
不具合の原因調査に活用することができます。
原因(要因)を図示して一覧化できるため、網羅的に調査を進められること、調査の優先順序を付けやすくなることが利点です。 - 課題整理
大骨、小骨に系統立てることで、要因の従属関係が分かりやすくなり、視覚的にスッキリと整理できます。
第三者にも初見でわかりやすい構成になっており、キチンと体裁を整えた特性要因図であれば、その資料自体を貴重な情報資産として残すことができるでしょう。 - 情報共有
要因をもれなく抽出する観点では、職場の関係者と協力して作り上げることも重要です。
はじめは、ホワイトボードに結果(特性)と背骨を記載し、みんなでアイデアを出し合う会議形式(いわゆるブレーンストーミング)で進めるのも一つの手です。
参加者全員の知識レベルの底上げにつながるだけでなく、認識の食い違いを修正できるため、組織としての意思統一を図ることに役立ちます。
どういう場面で使うの?
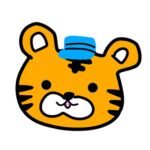
いろんな使い道がありそうだけど
製造業を例に挙げると、主に以下のような場面で活用されます。
製造、品質管理、品質保証部門はもちろんのこと、企画、研究開発、設計、調達、営業に携わる方にとっても登場する場面は多く、活用例は幅広いです。
活用例
分類 | 活用例 |
品質(Quality) | 不具合調査 品質維持管理 |
コスト(Cost) | 生産性改善 原価低減活動 |
納期(Delivery) |
工期短縮 サプライチェーン管理 |
その他 | 新人教育 QCサークル活動 情報共有ツール |
どのように作るの?
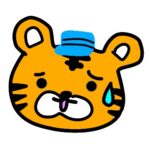
でも、自分で作るのは大変そうだな・・・
特性要因図の本質
ご自身の専門分野で、普段から論理的思考を実践できている方であれば、所要時間20~30分ほどでおおよその形を作ることができると思います。
「論理的思考なんて苦手だな・・」という方は、最初は要因の抽出と従属関係を整理するのに時間を要するかもしれませんが、心配することはありません。
いままで、何となく整理して理解したつもりになっていることを書き出すこと”頭の中の棚卸し作業”が重要なのです。
項目に抜けや漏れがあったり、因果関係のロジックが崩れていたりと、理解が足りないことに気づくキッカケになるものです。
このように「自分の理解度を正しく認識する」ことだけでも、特性要因図を活用する価値があります。
最初は頭の中を整理する目的で、しっかりと時間をかけて取り組みましょう。
重要なことなので繰り返しますが、”網羅的に系統的に要因を整理する”ことが肝心なので、お忘れなく。
やがて、論理的な思考方法に慣れてきたら、おのずと作業時間も短くなっていくことでしょう。
頭の中の情報を図示化して整理する「マインドマップ」という手法が一般的に使われていますが、これに似た考え方かもしれませんね。
前置きは、このくらいにして、実際に作っていきましょう。
手順
4つのステップで、作っていきます。
今回は、「機械加工の加工不良が多い」という題材を例に挙げて作成します。
- 課題を決めて背骨を作る
- 大骨を作る
- 中骨を作る
- 小骨を作る
- 課題を決めて背骨を作る
まず、解決したい課題(特性)を設定して右端に記入し、横一線に太い線を引きましょう。
これが背骨となり、後ほど細分化したさまざまな要因を結び付けていきます。
後で、上下に要因を結び付けていくので、配置に困らないよう、背骨はちょうど真ん中の高さに配置するとよいです。 - 大骨を作る
次に、課題に対して大まかに分類した影響要因を挙げ、大骨の末端に記載します。
分類の仕方は様々ですが、例えば、4Mの要素に分けて考えると整理しやすいと思います。
Man(人)、Machine(機械)、Material(材料)、Method(方法)の頭文字を表しており、大骨の項目をどのように分類するかによって、この後の要因の抽出のしやすさが変わってきます。
また、Measurement(測定)やEnvironment(環境)を加えて、5M+1Eとして分類することもあり、大骨の数に特に制約は考える必要ありません。 - 中骨を作る
大骨のそれぞれの項目に紐づく要因を挙げていきましょう。
例えば、以下のような項目が挙げられますね。 - 小骨を作る
先ほどと同じように、中骨に枝分かれする要因を抽出しましょう。
さらに細かく分割できる場合は小骨をさらに分岐させ、孫骨として記載しても構いません。
ここまでで要因の抽出は完了です。
最後に、結果に大きな影響を与えると考えられる要因を赤丸などで囲って、強調してわかりやすく表示します。
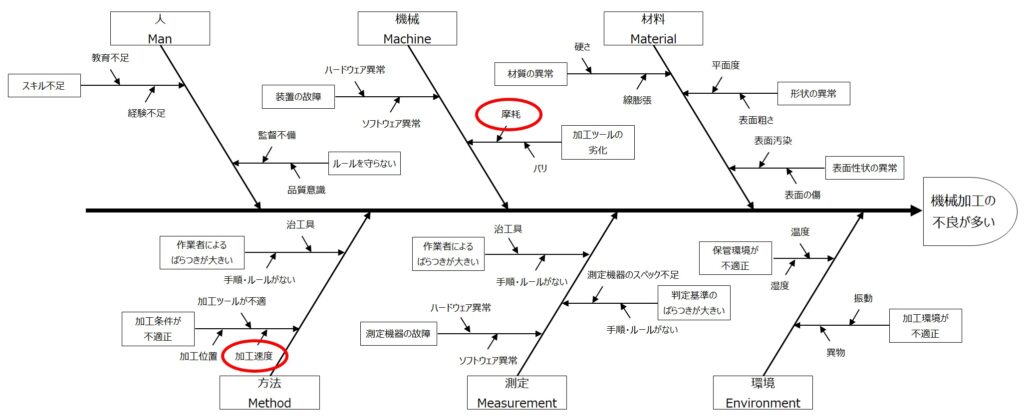
これで特性要因図が完成しました。
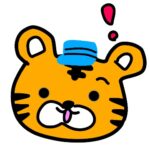
手順通りにやれば、思ったより簡単にできたよ!
作るときのポイント
- 大骨の分類が最重要!
- 中骨・小骨の要因の抽出は階層を意識しすぎない
- 「なぜ」を重ねて階層整理
- 次のアクションに結び付ける
- 大骨の分類が最重要!
大骨の分類がすべてと言っても過言ではありません。
先に説明した4Mは一例ですが、テーマによっては以下のような分類も有効です。
事例①:原価低減活動
⇒材料費、加工費、試験・検査費、販売管理費など
事例②:サプライチェーン管理
⇒調達、製造、販売、物流など
ここで適切な分類ができれば、中骨の要因整理をしやすくなり、体裁がスッキリするだけでなく、作成に要する時間も短縮化できます。 - 中骨・小骨の抽出は階層を意識しすぎない
中骨以降は分類項目が増えるので、階層整理を意識しすぎると、要因の抽出が不十分になる可能性があります。
まずは、要因をもれなく抽出することに集中しましょう。 - 「なぜ」を重ねて階層整理する
要因と結果の関係は、「なぜ?」の問いかけに対する答えです。
なぜの問いを重ねて、要因の階層を整理しましょう。 - 次のアクションに結び付けること
特性要因図の作成は手段の一つであって、目的ではありません。
完成したら、当初の目的(原因調査、情報共有など)を振り返り、次のアクションにつなげていきましょう。
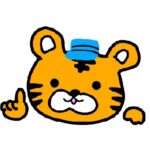
これでバッチリ!
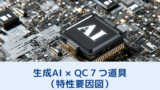
こてつ経験談
新規プロセスの立上げ
私が特性要因図を初めて知ったのは、とある新規設備の立ち上げを任された時でした。
それまでに、いくつかの設備の立上げ経験もあり、一通りの進め方を把握していたので、引き受けた際は安易に考えていたのですが・・。
実は、その設備は生産適用の実績やノウハウがまったくない、当時、新規プロセスとして初採用したもので、もちろん設備もフルカスタムでまったくの初物でした。
その立上げで、製造条件の追い込みに一人で悪戦苦闘していたのですが、とにかくパラメータの全貌も分からず、何がどの程度影響しているのかも分からず・・。
日々、闇雲に条件を変えて試しては失敗を繰り返し、行き詰っていました。
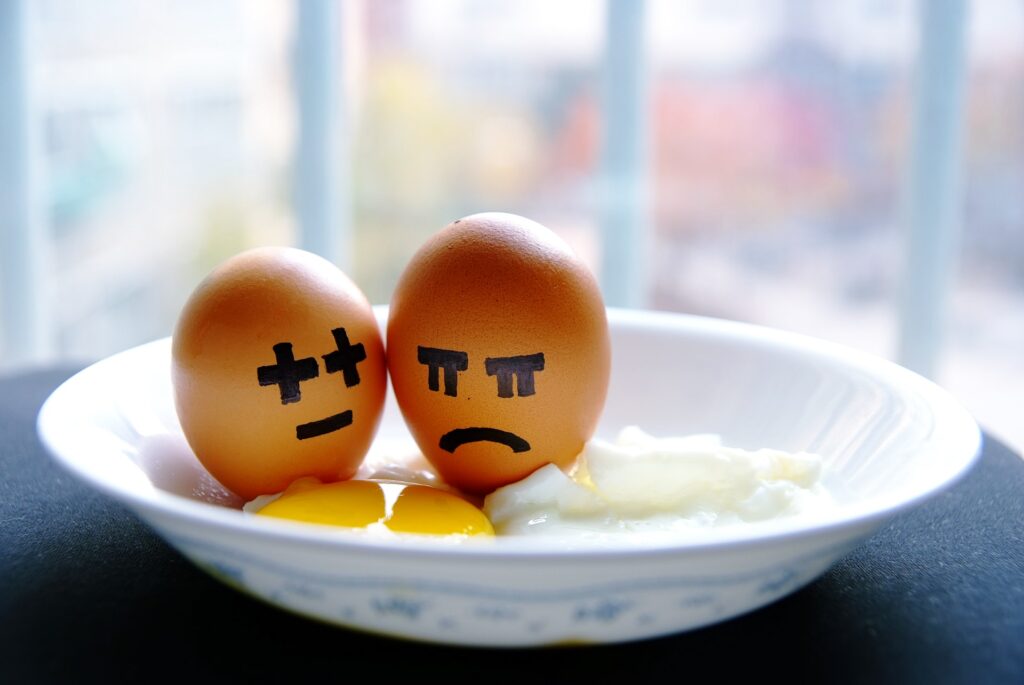
行き詰った先に
そんな時に特性要因図の存在を知り、設備のパラメータやハードウェアの構成要素を思いつくままに挙げて、整理してみることにしました。
さすがに、それで一挙に解決!と絵に描いたようなサクセスストーリーにはなりませんでした。
ただ、構成要素とパラメータを階層的に整理したことで、関係者に状況を説明しやすくなり、結果的に色々とアドバイスをもらうことができました。
結局、その当時に作成した特性要因図は、まとめ方も誰に教わったわけでもなく、自分でネットで調べて見よう見まねでやってみたので、いまから振り返ってみれば構成もイマイチでした。
ただ、自分なりに考えて因果関係を整理する、その行動自体が今となっては良い経験であったと思います。
特性要因図は初見では馴染みもなく取っつきにくそうなイメージがありますが、いちど自分でやってみれば、その次からは案外とハードルも低く感じるので、ぜひ実践してみることをおススメします。
まとめ
- 特性要因図
⇒「結果(特性)と原因(要因)を系統的に整理して視覚化したもの」 - 目的・用途・メリット
⇒原因調査、課題整理、情報共有など
⇒階層構造で視覚化して、全体像を網羅的に把握できる
特性要因図の作成プロセスそのものが価値のある思考方法です。まずは身近な課題解決を題材にして、ぜひ試してみてください。
最後まで読んでいただき、ありがとうございました。
この記事で紹介した特性要因図は、統計的品質管理(SQC)の手法の一つです。
製造業に携わるエンジニアであれば、その他のSQCの手法はもちろんのこと、品質管理、生産の基礎知識を幅広く身につけておく必要があります。
社内講座などの機会が設けられている場合は、ぜひ若手のうちから積極的に活用して受講することをおススメします。
ただ、多くの社員を対象とする社内講座の場合、皆さん一人ひとりのレベルに適した学習ができない場合もあります。
忙しい日々の限られた勉強の時間を最大限に活かすためにも、自分の教育プランは自分で管理することを意識して、能動的に学習することも検討してみてはいかがでしょうか。
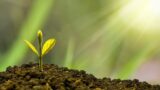
コメント