「FMEAを使うと、何のメリットがあるの?」
「どのような様式なの?」
「作り方の手順を知りたい」
こんな疑問や悩みをお持ちの方に向けた記事です。
FMEAは記入する項目が多く、点数付けも必要で、一見とても難しそうに思いますが、ひとつずつ手順を踏んで埋めていけば、誰でも簡単に作成できます。
初めての方でもわかるよう、できるだけ基本から説明しますので、皆さんの参考になればうれしいです。
また、YouTubeチャンネルでは、このブログの内容を動画で解説していますので、あわせてご覧いただけると幸いです。
FMEAとは?
FMEAとは、「Failure Mode and Effects Analysis」の略で、日本語では「故障モード影響解析」と呼ばれます。
あらかじめ、想定される製品の故障モードをランク付けし、点数の高い項目を見える化して対策の方針や優先順位を決めるための解析手法です。
FMEAには、製品の構成要素ごとに項目をリストアップする設計FMEAと、工程の手順ごとに項目をリストアップする工程FMEAがあります。
どちらも、設計、または工程の構成要素に分解し、それぞれの要素に対して故障モードを挙げていく、いわゆるボトムアップ型の解析手法です。
FMEAの構成
こちらは、工程FMEAの様式の一例です。
大きく分けて、表の左半分と右半分に分かれます。
左半分には、現在の工程(製品)の解析結果を記載します。
想定される故障モード、製品への影響、原因、発生防止、流出防止(検出)を記載して、最後にリスクの点数を記載します。
右半分には、対策に関する項目を記載します。
対策内容、期限、完了日付を入れて、最後に対策結果としてのリスクの点数を記載します。
このように、ひとつの表で工程(製品)を一覧化できるだけでなく、現状の問題点から対策結果まで全てFMEAのシートに表現できるので便利です。
FTAとの違い
故障モード解析には、もう一つFTA(Fault Tree Analysis:故障の木解析)の手法があります。
FTAは、特定の故障モードの原因を調査するための手法で、トップに故障モードを記入して、そこから樹形図状に項目を細分化する様式をしています。
FTAはトップダウン型の解析手法で、FMEAと混同しがちなので、違いを覚えておくとよいでしょう。
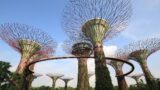
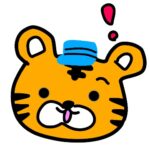
FMEAは未然防止、FTAは事後の調査で使うんだね
目的・用途・メリット
1.故障モードの一覧化
あらかじめ、想定される故障モードをリストアップすることで、不具合の未然防止に効果的です。
特に、新製品の開発や、設計・工程変更の際に整理しておくと、万が一、トラブルが発生しても迅速に初動対応を行うことができます。
2.対策の優先順位付け
FMEAの一番の特徴でもあるのが、項目の点数付けです。
影響×発生×検出=RPN(Risk Priority Number:リスク優先度)として点数化することで、優先対応すべき項目をはっきりと示すことができます。
客観的な指標で表現できるので、関係部門や客先との合意も得られやすくなります。
3.対策の効果確認
現状の問題点を解析して、対策を実施して、それで終わりではありません。
きちんと、対策の効果を確認して、次の課題設定を行い、PDCAサイクルを回していかねばなりません。
FMEAでは、ひとつのシートに効果の確認まで記載するので、対策の前後比較をしやすいことが利点です。
作り方の手順
FMEAシートの作り方の手順を説明します。
実施手順だけを説明しても、それぞれの欄にどのような項目を記載すればよいのかイメージが付きにくいと思うので、具体例を挙げて説明します。
今回は、工程FMEAを事例に説明しますが、設計FMEAに関しても、工程を構成部品に置き換えて考えれば同じなので、ご安心ください。
工程を解析する
1.工程順を整理する
シートの左半分で、現状の問題点を洗い出します。
まずは、工程の手順を整理して記入していきます。
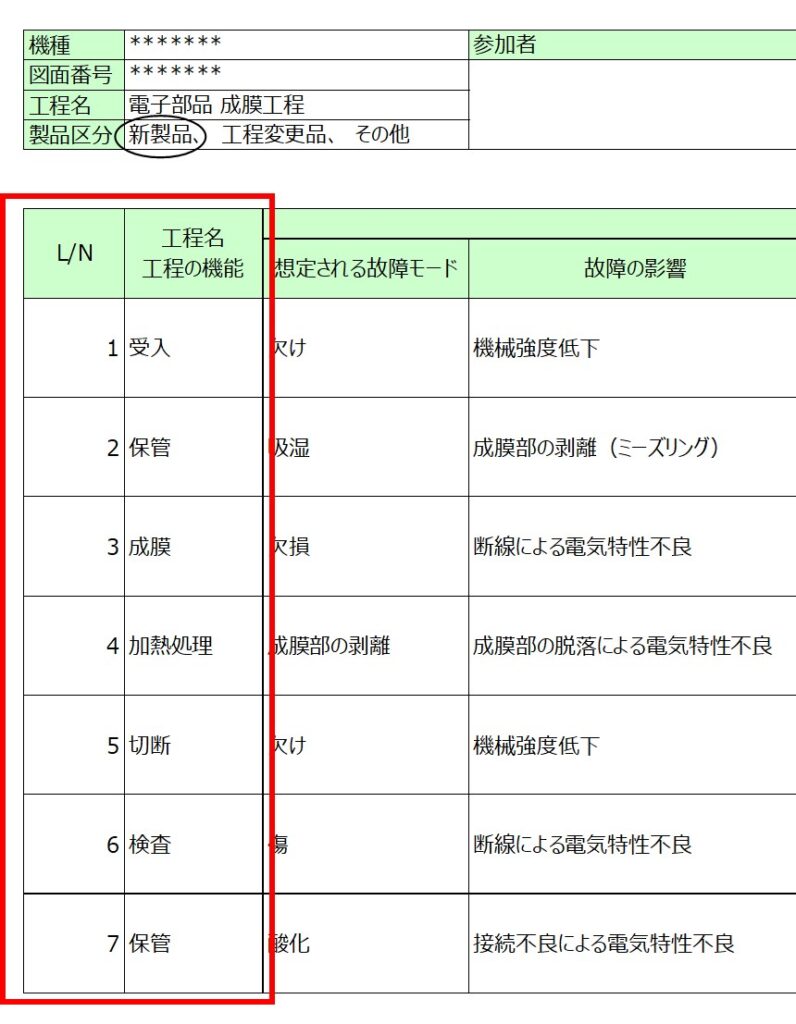
基本的には、QC工程図と同じ項目を挙げるイメージで良いです。
実際の加工の作業だけでなく、部品の受入や保管、検査についても記載するようにしましょう。
2.想定される故障モードを挙げる
次に、各工程で予測される故障モードを挙げていきます。
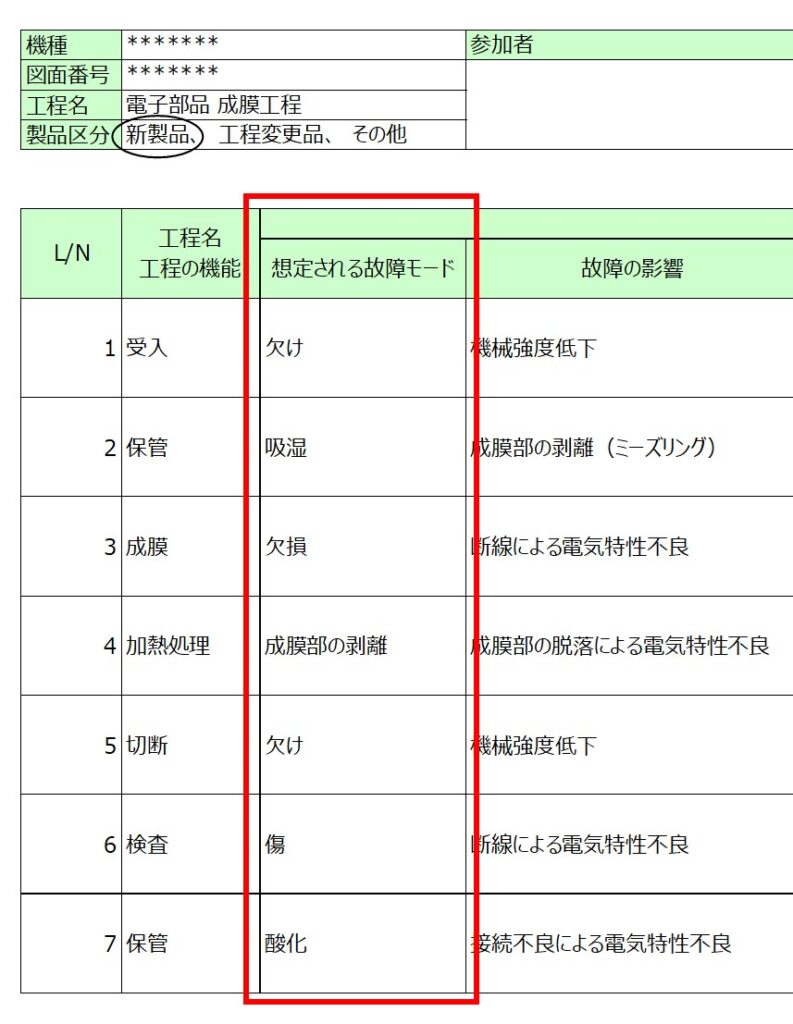
例えば、傷や割れなどの外観不良として見える項目だけでなく、部品の酸化や吸湿といった故障の原因となり得る要素も挙げるようにしましょう。
故障の原因となり得る項目は、「推定原因」の方に該当するのでは?と疑問に思うかもしれません。
確かに原因と言えばその通りですが、FMEAを作る順序に沿って考えてみてください。
具体例として、加熱工程での故障モードとして、剥離や膨れなどの外観異常があったとします。
そして、その推定原因に部品の吸湿が登場するわけなのですが、剥離や膨れの原因と言えば、製造条件の不良や装置の異常などが先に思いつくところで、部品の保管条件まで網羅して挙げられない可能性があります。
そのため、保管工程では保管に関わる異常として着目し、その故障モードして酸化や吸湿を挙げることで、漏れを防ぎやすくなるのです。
3.故障の影響と推定原因を挙げる
それぞれの故障モードに対応付けて、製品の品質への影響と、その原因を記載します。
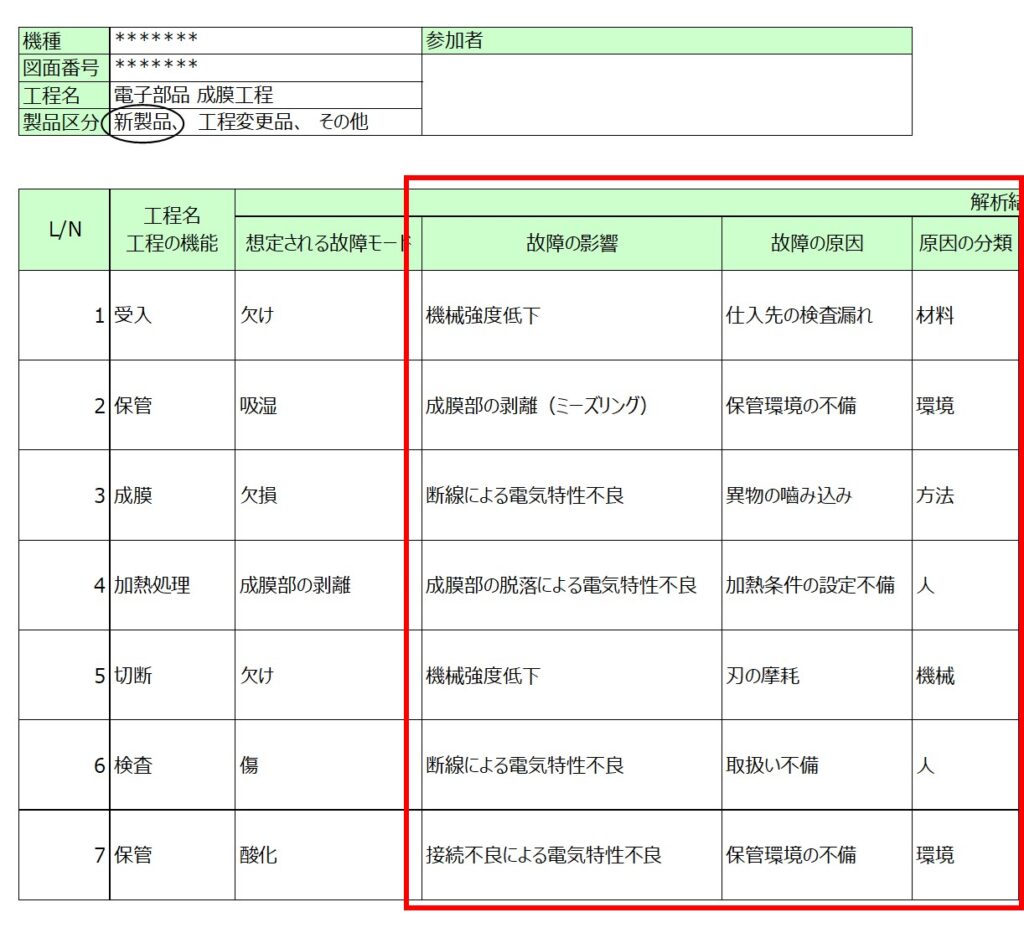
原因の抽出には、5M+1Eの要素に分類すると網羅的で分かりやすいです。
5M+1Eとは、Man(人)、Machine(機械)、Material(材料)、Method(方法)の4Mの要素に、Measurement(測定)、Environment(環境)を加えたものを表します。
例えば、装置の入力間違い(人)、条件の不適正(方法)、保管温度・湿度が不適正(環境)といったように分類すると分かりやすいです。
また、このように分類することで、どの要素に多くの原因があるのか、すなわち自分たちの工程の弱点を知ることができます。
4.発生防止策、流出防止策を記載する
次に、現行の工程管理における発生防止策と流出防止策(検出策)を記載します。
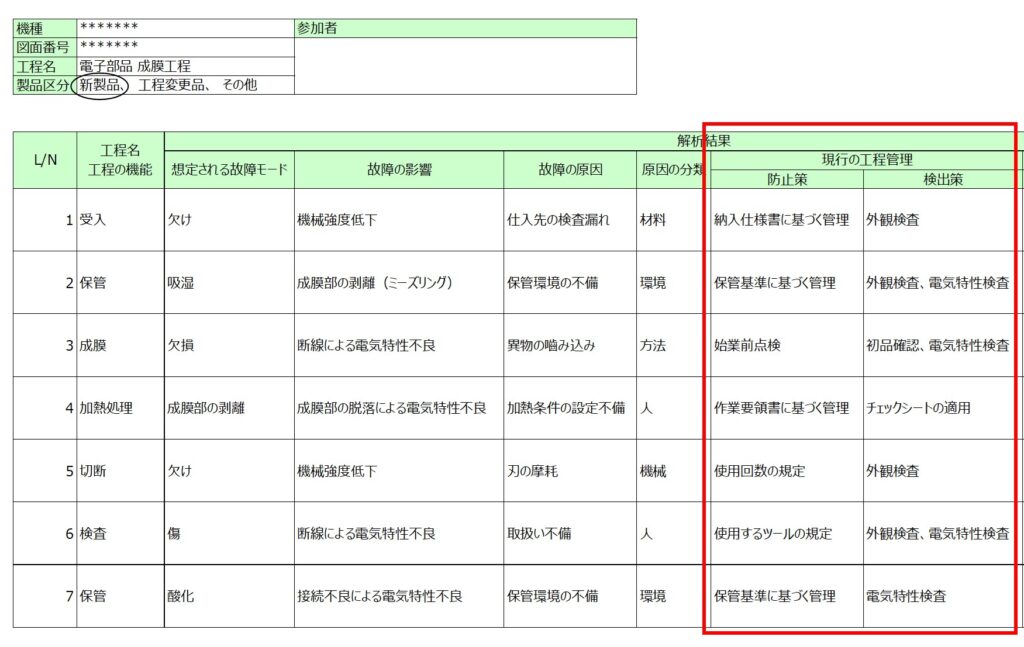
発生防止に関しては、例えば、作業方法の教育や、保管基準の規定、初品確認などが挙げられます。
大きく分類したイメージで言うと、作業者の教育、規格類の制定、現品確認、設備の始業前点検といった項目を挙げていくと、ほとんどの工程に対応付けられると思います。
また、流出防止に関しては、例えば、作業者の外観チェックや電気検査などがあります。
さらには、ダブルチェックや、チェックシートの適用などの仕組み的な要素も盛り込むことが望ましいです。
5.リスク優先度を点数化する
現状分析の最後は、リスク優先度の点数付けです。
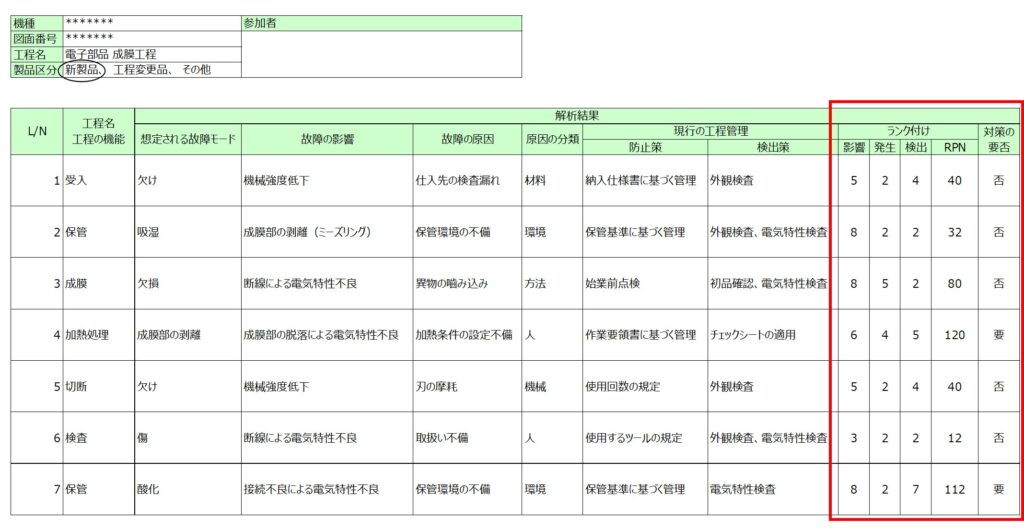
以下の3つの要素に分けて点数化します。いずれも、1~10で数値にして、点数が高いほど影響の大きいことを意味します。
①:影響
重要度を表します。例えば、故障が発生した場合に、製品が全く機能しなくなるのか、性能が低下するのか、それとも無視できる範囲なのかによって、影響の大きさが変わります。
②:発生
発生の頻度を表します。毎日発生するのか、あるいは週に1回程度なのか、目安を決めて点数化しましょう。
③:検出
検出の可能性を表します。全く検出できない、次の工程で検出可能、自工程で全て検出可能といったように、検出のしやすさを点数にします。
最後に、リスク優先度としてRPN(Risk Priority Number)を算出します。
計算の仕方は単純で、「影響」×「発生」×「検出」で求めることができます。
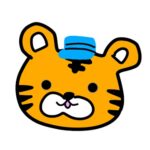
ここまで完成すれば、もう一息
対策を実施する
現状分析ができたら、次は対策の要否を検討して、必要なものは対策を講じます。
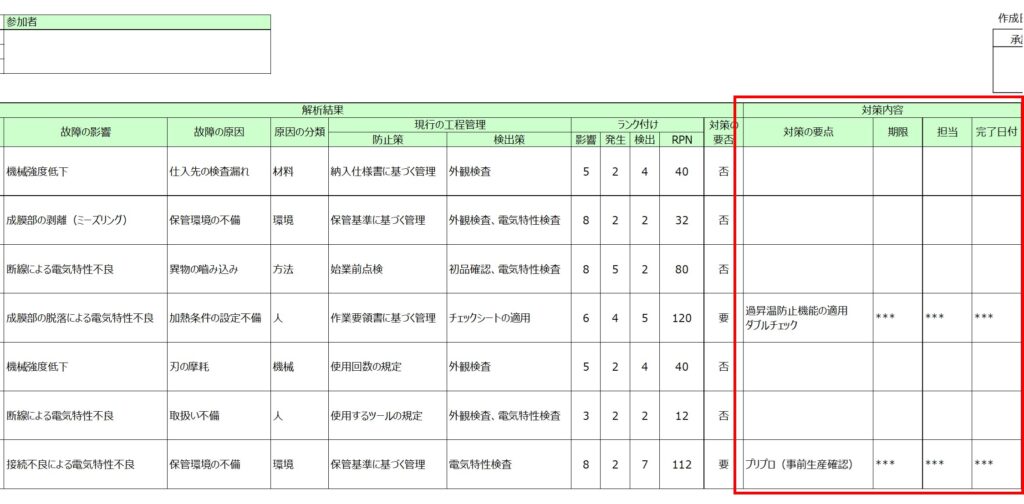
対策の要否の判断は、製品によって様々ですが、一般的にRPNが100以上の項目に対して対策が必要と判断することが多いです。
6.対策内容を記載する
対策の要点を記載します。
最終的にRPNを下げることを目的としているので、「影響」、「発生」、「検出」の要素のうち、点数の高いものを対処するようにしましょう。
以下では、それぞれの要素の点数が高い場合における対応策の事例を紹介します。
①:影響が大きい場合
故障が発生すると製品が機能しなくなるので、バックアップを備えた構造にする対策が考えられます。
例えば電子部品では、保護用のバックアップ回路を設けるとか、製造条件や保管条件を厳密に規定して断線による最悪の事態を避けるとか、設計や工程で対処できるものを挙げます。
②:発生の頻度が高い場合
モノづくりには、ばらつきが付きものです。
同じ材料、同じ条件で作っていても、一定の分布でばらつきが生じ、ロット内でも良品と不良品ができてしまいます。
規格値(しきい値)に対して、分布の位置が近いと規格を超える確率も高くなるので、発生率を抑えるには、次の3つのアプローチが考えられます。
一つ目は、分布の平均値を下げること。
二つ目は、分布のばらつきを小さくすること。
これらは、材料や部品の改善や、製造条件の改善によって実現できます。
最後に三つ目は、規格値自体を見直すこと。
根拠なく緩めることは許されませんが、品質要求をあらためて精査して、妥当な規格を設定するようにしましょう。
分布と規格値の考え方は、ヒストグラムの記事でも紹介していますので、合わせてご覧ください。
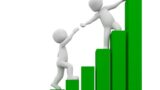
③:検出感度が低い場合
検出感度を向上するには、仕組み、人、装置の観点でアプローチすることをおススメします。
仕組みには、ダブルチェックやチェックシートの適用など。
人に関しては、作業者の教育や訓練など。
装置に関しては、検査の自動化や、しきい値の厳格化など。
このように、多角的に対策を講じることで、流出防止に強い工程(製品)を作ることができます。
特に、装置に関しては、単に一つのしきい値だけで合否を決めるのではなく、警告値を設けることが望ましいです。
いきなり規格値を超えてしまっては、現場もパニックになり、まともな判断ができなくなる可能性があります。
そのため、兆候を見つけることを目的として、しきい値よりも、さらに厳しい値を警告ゾーンとして設けて、これを超えたら生産を止めて確認する。
このような運用にすることで、不具合の未然防止に繋がり、万が一、不具合が発生しても迅速に対応できます。
対策結果を評価する
最後に、対策結果をランク付けしましょう。
現状分析と同じようにRPNを算出し、まだ点数の高いものが残っている場合は、さらに対応策を講じるようにしましょう。
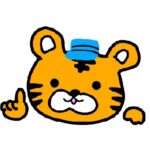
これで未然防止の対策はバッチリ!
FMEA作成のポイント
1.故障モードはできるだけ具体的に
故障モードやその影響、原因は、できるだけ具体的に記載しましょう。
例えば、故障モードに「破損」と記載した場合、欠けか傷か、あるいは割れているのか区別がつきません。
それぞれ、原因は異なりますし、故障の影響も変わってくるかもしれません。
漠然と記載すると、抽出漏れになりかねないので、具体性を意識することを心がけましょう。
2.点数付けは指標を決めて客観的に
FMEAは、RPNの点数が結果の全てと言っても過言ではありません。
つまり、点数の付け方しだいで、結果の見え方が全く変わってくるので、感覚で適当につけてはいけません。
例えば、発生頻度の場合、毎日、週に1回、月に1回とか。
検出の場合は、検出不可、後工程で検出可能、自工程で検出可能とか。
あらかじめ、点数と目安の対応を表に整理するなどして、常に客観的に同じ基準で点数付けできるようにしておきましょう。
3.全部門参加で実施する
FMEAは、その様式の特徴の通り、故障の予測から防止策、検出策までを一覧に表すので、製品設計、工程設計、製造、品質管理の全ての観点が必要です。
そのため、どこか特定の部門だけで進めるのではなく、全部門で議論して多角的な視点で課題と対策案を挙げるようにしましょう。
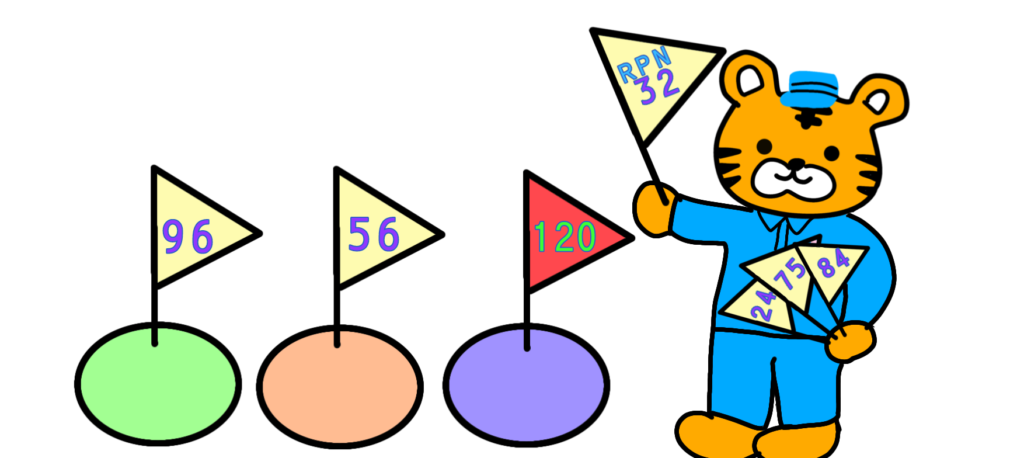
まとめ
- FMEA(Failure Mode and Effects Analysis:故障モード影響解析)
⇒想定される製品の故障モードをランク付けし、点数の高い項目を見える化して対策の方針や優先順位を決めるための解析手法
⇒設計、または工程の構成要素に分解し、それぞれの要素に対して故障モードを挙げるボトムアップ型の手法 - 目的・用途
⇒故障モードの一覧化、対策の優先順位付け、対策の効果確認 - 作り方の手順
⇒①:工程を解析する
②:対策を実施する
③:対策結果を評価する - 作り方のポイント
⇒①:故障モードはできるだけ具体的に
②:点数付けは指標を決めて客観的に
③:全部門参加で実施する
FMEAは、その様式の見た目から、ハードルが高そうに思えて、作るのを敬遠しがちになる方もいるかもしれません。
しかし、手順を踏めば誰でも簡単に作成でき、しかも現状の問題点から対策結果まで全てを一つのシートに表現できる優れものです。
客先の説明資料としても説得力のある有効なツールですので、ぜひ使いこなせるようにしておきましょう。
最後まで読んでいただき、ありがとうございました。
ケーススタディで学びたい方に。
基礎から豊富な事例まで幅広く、教科書的な一冊。
FMEAを極めるならコレ。
コメント