品質管理の基本的な考え方の一つとして、「重点指向」をご存じでしょうか。
重点指向とは端的に言うと、きちんと優先順位を付けて取り組む活動方針の考え方です。
人・カネ・時間など、限られたリソースの中で活動するには、プライオリティを付けて取り組むことが求められます。
この記事では、モノづくりにおける重点指向を実践するにあたって、優先順位の付け方と具体例を解説しています。
製造に関わる中で、優先の付け方のポイントを知りたい方や、重点指向に使えるツールの具体例を知りたい方にとって参考になればうれしいです。
重点指向とは
重点指向とは、あらかじめ結果に及ぼす影響の大きいものを予測して、効果の大きいものから優先順位を付けて対処することで改善を効率的に進める考え方です。
例えば、良品率の改善をイメージしてみてください。
何か一つの不良であれば、それだけに注力すれば良いですが、おそらく様々なモードの不良があり、全てを対処していては、時間もお金も膨大にかかってしまいます。
そんな時にプライオリティを付けて進めるのは、ごく一般的な考え方で、どの生産現場でも無意識に重点指向を実践していると思います。
ただ、優先順位を決める時に、何となく発生数が一番多いからという理由だけで判断していませんか?
もちろん、数が多いのも大きな目安の一つですが、この他にも判断のポイントがいくつかあります。
以降では、優先順位を決める判断基準の3つのポイントを解説します。
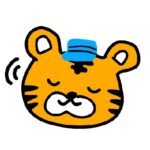
どれから手を付けるか、最初に順番を決めるのが大事だね
プライオリティの付け方のポイント
ポイント1:重要度
当たり前の話ですが、重要度の高いものから対処していきます。
例えば、100個の不良が発生している事象と、1個しか発生していない事象、優先順位を付けるとしたら、当然多い方を選びますよね。
このように不良品の数として明白な場合は簡単ですが、その他にも重要度を図る指標をご紹介します。
①:製品の数量
これは先ほど紹介した事例です。
数を集計すれば、おのずと順位付けができるので分かりやすいと思います。
②:ロスコスト
製品の金額に換算することも一つの目安になります。
例えば、同じ100個の不良でも、単価が100円の製品と1万円の製品なら、一目瞭然ですね。
あるいは、製品そのものの金額でなくとも、追加の加工や検査が発生する場合は、その工数を加算して見積もることも考え方の一つです。
ポイント2:緊急度
緊急性の高いものから対処する考え方です。
緊急性の判断には、以下のような指標があります。
①:納期
納期遅延は、お客様に迷惑をかけるだけでなく、会社の信頼を損なってしまいます。
また、お客様への出荷だけでなく、自社の後工程への受け渡しについても同様で、装置や人を準備してスタンバイしたものがムダになってしまいます。
納期のデッドラインまでの猶予を考えて、優先順位を付けるようにしましょう。
②:波及範囲
仮に、処置をせずに見送った場合、他の製品や後工程に波及する恐れがあります。
その場合、他の生産ラインや後工程を止めることになりかねないので、早急に波及の有無を判断する必要があります。
不具合が発生した段階では、数量や金額は同じであっても、その後の波及を考えた場合に、優先順位が明確なことがあるので見逃さないようにしましょう。
ポイント3:拡大傾向
最後に時間軸に対する推移を見る考え方です。
拡大傾向にあるものは、今後の影響が増々大きくなるので、優先した対処が必要です。
日常点検や検査結果のトレンドを見て増加傾向にある場合や、近いうちに許容範囲から逸脱することが見込まれる場合には、工程を止めて調査が必要です。
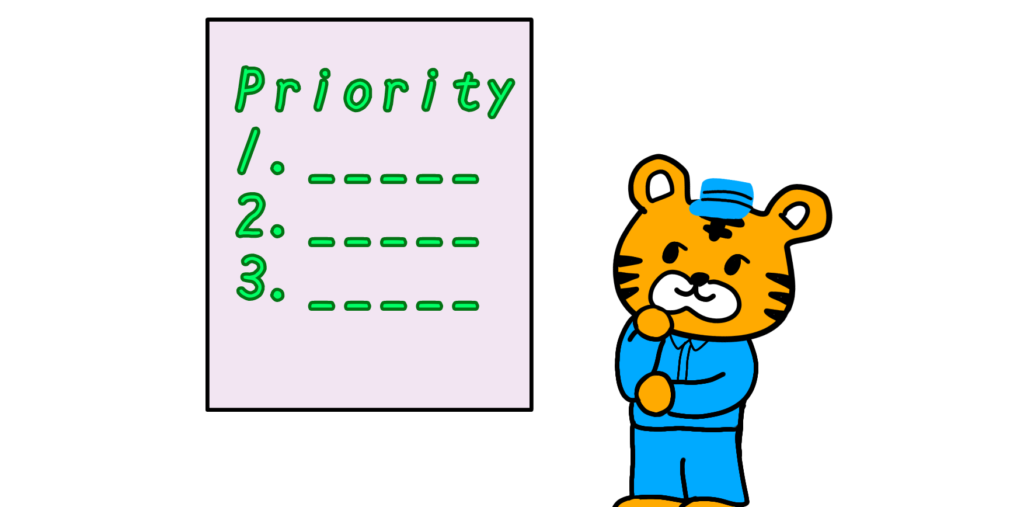
重点指向に使えるQC7つ道具
ツール1:パレート図
パレート図とは、棒グラフと折れ線グラフを組み合わせた複合グラフで、降順(値の大きい順)に並んだ棒グラフと、累積構成比を表す折れ線グラフから構成されています。
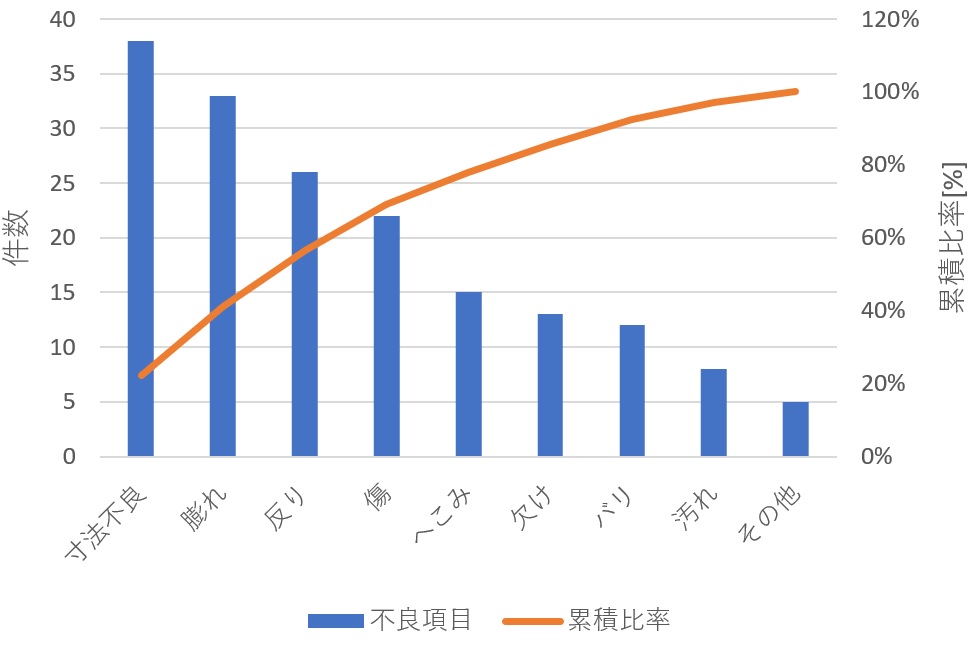
項目の値の大きい順に並べたグラフの見た目から、影響度の大きさが視覚的に分かりやすいと思います。
単純に一番左の項目を見れば、頻度の高いものを把握できますが、原因別に項目を分類することで、共通点を分析して根本原因を解決する足掛かりにすることもできます。
詳細は、パレート図の記事で紹介していますので、合わせてご覧ください。
ツール2:管理図
管理図とは、データの折れ線、中心線、上下限の管理限界線からなるグラフで、製造工程で異常の兆候を見つけるための分析ツールです。
管理図では、時系列に対するトレンドの変化を見ることができます。
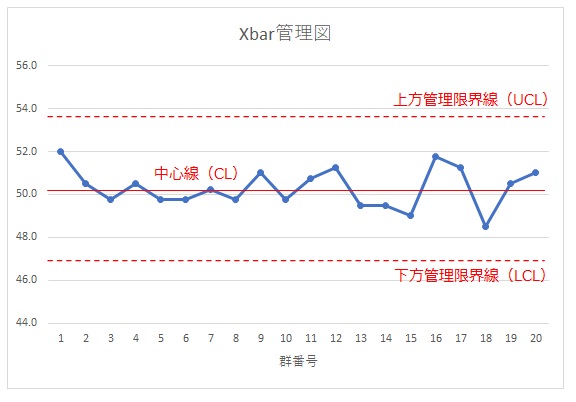
異常の判定には8つのルールがあり、管理限界線に対するデータのプロットの位置関係を見ることで、システマティックに判断できます。
また、管理図はデータの性質から計量値管理図や計数値管理図に分かれ、さらに、データの種類に応じて細かく分類されます。
これらの管理図を使い分けることで、工程で取得する色々なデータを当てはめることができるので、ぜひ実用に試してみてください。
ツール3:マトリックスデータ解析法
3つ目の事例は、新QC7つ道具から紹介します。
マトリックスデータ解析法は、主成分分析とも呼ばれます。
変数がたくさんある場合に、できるだけ元のデータの情報を残しつつ、要素を縮約して二次元の平面図に表し、問題と要因の関係をわかりやすく示す手法のことです。
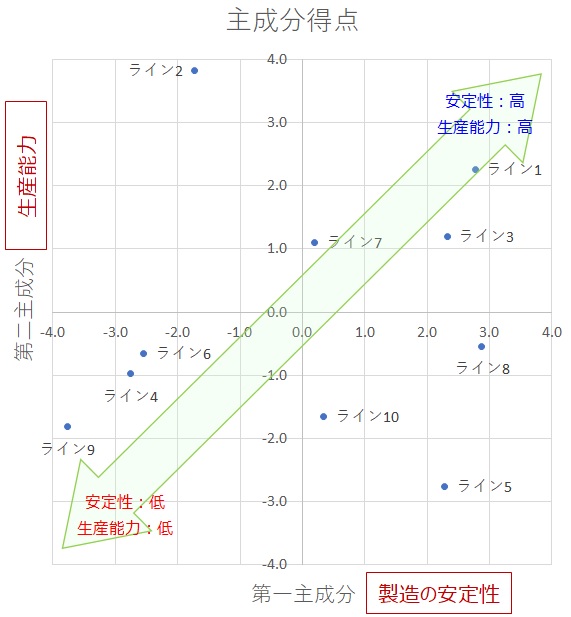
マトリックスデータ解析法では、元の変数から関連性の高いものを組み合わせた「主成分」を新たな指標とすることで、相関関係をより強く表すことができます。
そして、影響度の高いものから順に、第一、第二主成分と表現されます。
この手法を用いることで、膨大なデータから影響度を数値化して把握することができます。
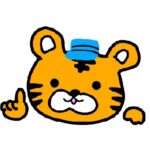
QC7つ道具は、数値化や見える化に重宝するよ
こてつ経験談
責任感が強い影響?
時折、複数の業務を掛け持ちして、仕事がパンクしている若手を見かけます。
聞くと、「あれもこれも任されて処理しきれません」というケースが多いです。
確かに、新人時代を過ぎて、ある程度一人で仕事ができるようになると、上司や周りから多くの案件を任されることになります。
上司が自分の負荷を細やかに管理してくれて、優先順位まで全て決めてくれれば良いですが、それでは自身の成長になりません。
自分で考えさせることを狙いとして、あえて細かいところには口出しせず、後ろから見守っている上司も多いことでしょう。
そして、責任感が強い人ほど、あれもこれも全て100点満点の成果を出そうと頑張るのですが、そうすると、やがてオーバーフローする時が来ます。
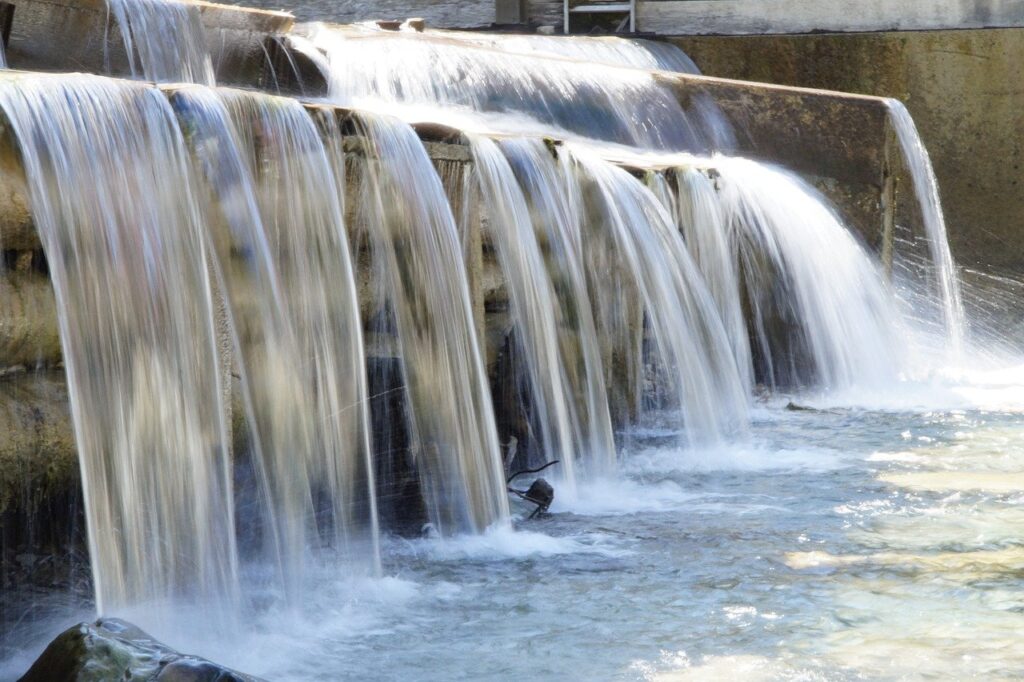
同時並行は重点指向ができてから
全て同時並行で完璧を目指そうとする心意気は良いのですが、区切りが中途半端であったり、順番が不適切であったり、進め方に問題があることも多々あります。
こんな時に若手の皆さんに伝えているのが、「まずは一つの案件に集中して、期限と完成度をよく精査すること」です。
つまり、いつまでにどの程度の完成度が必要か、完成できなかったら何に影響するか、これらをキチンと整理することです。
最低限で満たすべき完成度やデッドライン、可能であれば到達したい完成度や納期短縮、これらを明確に分離しておくことで、別案件が重なった際にも上手く両立させてバランスを取ることができます。
いきなり同時並行の処理を目指すのではなく、優先順位の付け方や考え方を定着させることに重点を置くことが望ましいと思います。
まとめ
- 重点指向
⇒あらかじめ結果に及ぼす影響の大きいものを予測して、効果の大きいものから優先順位を付けて対処することで改善を効率的に進める考え方 - プライオリティの付け方のポイント
⇒重要度(数量やロスコスト)
緊急度(納期や波及範囲)
拡大傾向 - 重点指向に使えるQC7つ道具の例
⇒パレート図
管理図
マトリックスデータ解析法 など
いつまでに何をやる必要があるか、最初の目標設定がすべてを決めると言っても過言ではありません。
限られたリソースで結果を出すのは、モノづくりの現場だけではなく、一般的に通じる話です。
ぜひ、身近な課題で重点指向の考え方を取り入れてみてはいかがでしょうか。
コメント