FTA(故障の木解析)は、不具合事象をトップにして、故障の要因を階層に分解した樹形図状の図式で、原因調査を網羅的に行うための解析手法です。
FTA基礎編の記事でも紹介した通り、不具合の原因調査、不具合要因の一覧化、発生確率の推定など、様々な目的で活用できる強力なツールです。
しかし、その有効性はいかに漏れなく基本事象を洗い出せるかに大きく左右されます。
基本事象とは、FTAの最下層に位置する、それ以上分解できない事象のことで、これらが抜け漏れてしまうと解析の信頼性が損なわれ、リスク評価や対策検討が不十分になる可能性があります。
例えば、製造業の現場で設備の故障を分析する際、基本事象の洗い出しが不十分だと、見落とした要因が原因で再発してしまうかもしれません。医療現場であれば、医療機器の故障原因を見誤り、患者の安全を脅かす可能性もあります。
そこで本記事では、FTAの基本事象を漏れなく抽出する秘訣としてMECE(ミーシー)という概念に着目し、網羅的かつ効率的に基本事象を洗い出すための具体的なアプローチを紹介いたします。
FTAの精度を向上させ、より信頼性の高いリスク評価や対策検討を行う上で、皆さんの参考になればうれしいです。
基礎編から学習したい方はこちらからどうぞ。
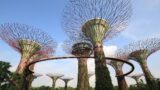
MECE(ミーシー)とは?
FTAの精度を高めるためには、基本事象を網羅的に洗い出すことが不可欠です。そこで重要となるのが、MECE(ミーシー)という概念です。
MECEとは、「Mutually Exclusive and Collectively Exhaustive」の略で、「互いに重複せず、全体として漏れがない」という意味です。
つまり、ある事象を分析する際に、考えられるすべての要素を網羅し、かつそれらの要素が互いに重複しないように分類することを指します。
例えば、ある製品の故障原因を分析する場合、MECEな分類とは、考えられるすべての故障原因を網羅し、かつそれらの原因が互いに重複しないように分類することです。
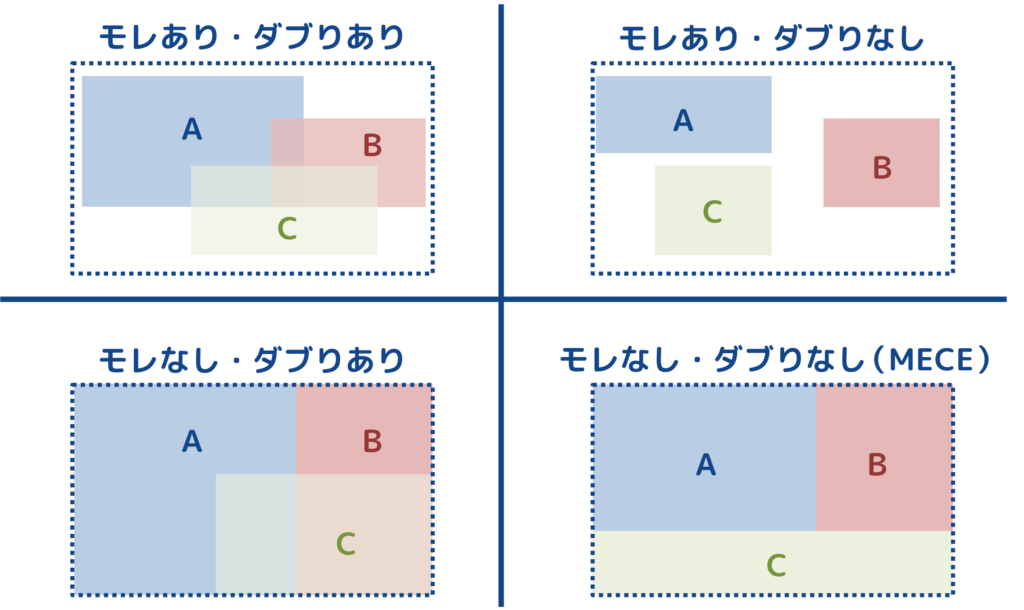
FTAにおけるMECEの重要性
- 基本事象の抜け漏れ防止
MECEな分類を行うことで、考えられるすべての基本事象を網羅的に洗い出すことができる - 分析の効率化
要素が重複しないように分類することで、無駄な分析を省いて効率的に原因を特定できる - 分析結果の信頼性向上
抜け漏れや重複のない分析は、その結果の信頼性を高め、より正確なリスク評価や対策検討につながる - 関係者とのコミュニケーション円滑化
分析結果を関係者に説明する際に内容が伝わりやすい
MECEの身近な例
MECEのイメージをより具体的に掴んでいただくために、身近な例を紹介します。
旅行の持ち物の分類
- 衣類(下着、上着、ズボンなど)
- 洗面用具(歯ブラシ、シャンプー、タオルなど)
- 貴重品(財布、パスポート、航空券など)
- その他(カメラ、モバイルバッテリー、常備薬など)
給食の献立
- 主食(ご飯、パン、麺類など)
- 主菜(肉、魚、卵など)
- 副菜(野菜、きのこ、海藻など)
- 汁物(味噌汁、スープなど)
意外と日常生活にも馴染みのある考え方と思いませんか?
普段は無意識に使っている用語や分類のしかたでも、実は漏れなく、ダブりなくフレームが決められていることで、すんなりと内容が理解できる助けになっているのです。
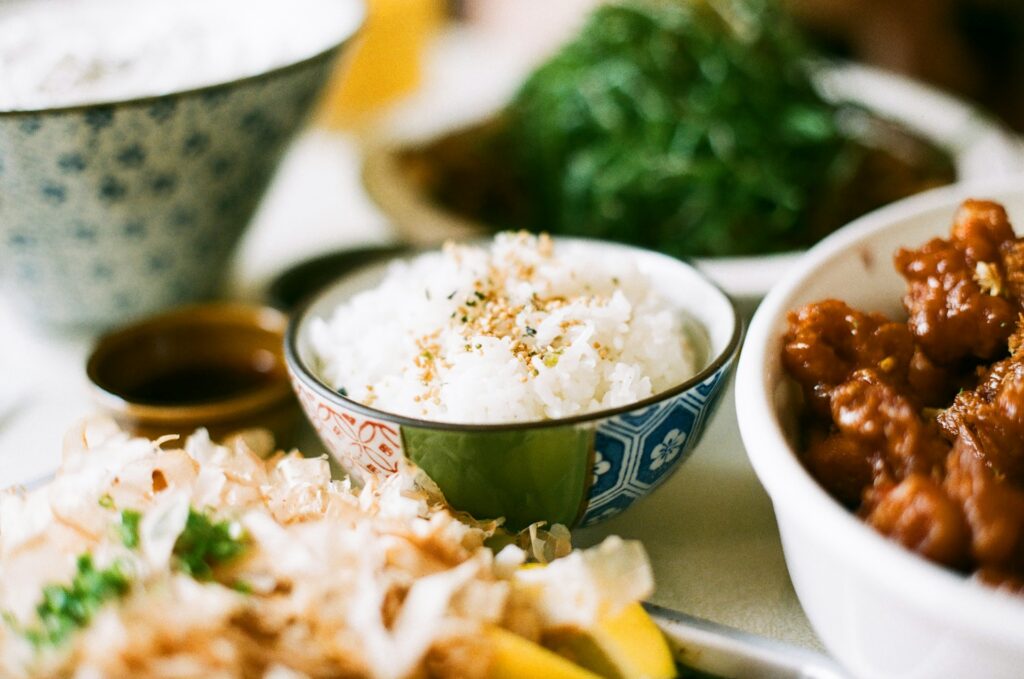
4Mの要素で分類:まずは製造業の基本を押さえる
それでは、実際にFTAの要因を抽出するにあたって、MECEの考え方をどのように用いるのか事例を紹介します。
FTAで基本事象を漏れなく洗い出すためには、一次要因をどのように分類するかに全てがかかっているといっても過言ではありません。
最初の入り口の分類が網羅的でないと、当然ながら基本事象が漏れなく抽出できるはずもなく、この一次要因の洗い出しにMECEの考え方が最大限に活用されます。
その最も代表的な例と言える分類が、4M(Man, Machine, Material, Method)による分類で、製造業を中心に広く用いられている基本的な分類方法です。
- Man(人): 作業者のスキル、経験、疲労、注意不足など
- Machine(機械): 設備の故障、精度不良、メンテナンス不足など
- Material(材料): 原材料の品質不良、保管状態の不備など
- Method(方法): 作業手順の不備、設計上の問題など
4Mによる分類は、シンプルで分かりやすく、現場で活用しやすいのが特徴です。
また、4Mの要素に「Measurement(測定)」や「Environment(環境)」を加えて、5M+1Eと表現する場合もあります。
工程順で分類:時系列で情報を整理する
分析対象のシステムや製品の製造・開発プロセスを時系列に沿って分解し、各工程で発生する可能性のある故障要因を洗い出します。
工程を順番に追っていけば良いので、例えばQC工程図やシステム設計書などに沿って要因を挙げていけば確実に抜け漏れを防ぐことができます。
事例)
- 製造業:原材料調達→部品加工→組み立て→検査→出荷
- ソフトウェア開発:要件定義→設計→開発→テスト→リリース
- 医療:患者受付→問診→検査→診断→治療→経過観察
- 工程を細かく分解しすぎると、分析が煩雑になる可能性があるので、適切な粒度で工程を設定する
- 並列工程やループが存在する場合は、それらを考慮した分析が必要
- 前工程で発生した故障が次工程に影響を与える可能性があり、工程間の相互作用も考慮が必要
機能別で分類:システムや製品の構造から攻める
システムを構成する各機能に着目し、それぞれの機能が故障した場合にどのような影響があるかを分析する方法で、特に複雑なシステムの構成を分解して考えるうえで効果的です。
機能別アプローチでは、システムを機能ブロック図や構成図などの形で表現し、各機能ブロックの役割と相互関係を明確にします。そして、各機能ブロックが故障した場合に、システム全体にどのような影響を与えるかを分析します。
事例)
- 自動車のブレーキシステム
マスターシリンダー、ブレーキパイプ、ブレーキキャリパー、ブレーキパッド、ABS(アンチロック・ブレーキ・システム) - オンラインショッピングサイトの決済システム
ユーザー認証、商品選択、支払い方法選択、クレジットカード決済、銀行振込、決済情報データベース - 医療用人工呼吸器
酸素供給、圧力制御、流量制御、アラーム機能、電源供給、制御システム - ソフトウェアのログイン機能
ユーザーインターフェース、ユーザーID/パスワード入力、認証サーバー、データベース、エラー処理
- システムが複雑な場合には、機能を階層的に分割したほうが整理しやすい
- 機能間の境界を明確にすることで、責任の範囲を特定しやすい
- 機能の相互作用を考慮することで、連鎖的な故障のリスクを評価しやすい
環境要因アプローチ:外部環境も考慮する
さらに別の切り口としては、環境要因から分類する方法も有効です。
例えば、高温多湿、振動が多い場合など、特定の環境条件下での故障対策に有効であり、脆弱性を把握して設計や運用に反映することで、システムの耐環境性を向上することができます。
事例)
- 物理的環境
温度、湿度、振動、衝撃、騒音、放射線 - 電気的環境
電磁波(電磁ノイズ、電磁誘導)、静電気、電圧変動 - 化学的環境
腐食性ガス、塵埃、塩害 - 生物的環境
菌類、微生物、昆虫
他の要因との相互作用
環境要因は、他の要因(4Mなど)と相互に作用して故障を引き起こすことがあるため、複合的な分析を行う上でも常に考慮に入れる必要があります。
- 温度+材料
高温環境下で材料の劣化が早まる場合など - 湿度+電気部品
高湿度環境下で電気部品の絶縁性が低下し、ショートや漏電が発生する場合など - 振動+機械部品
振動が多い環境下で機械部品の摩耗が早まり、故障につながるなど
まとめ
MECE:すべての要素を網羅し、かつそれらの要素が互いに重複しないように分類する考え方
FTAにおける一次要因の分類例
- 4Mで分類
- 工程順(時系列)で分類
- 機能別で分類
- 環境要因で分類
MECEによる分類は、FTAの精度を向上させるための強力な武器となります。
本記事で紹介した内容が、より安全で信頼性の高いシステムや製品を実現する一助になれば幸いです。最後までご覧いただきまして、ありがとうございました。
コメント