「プロセス保証って、どんな考え方なの?」
「特殊工程って何だか不安」
「保証に使えるツールを教えて」
こんな疑問や悩みをお持ちの方に向けた記事です。
プロセス保証とは、製造プロセスの作り込みによって品質を保証すること意味し、出来上がった製品で直接的に品質保証する考え方と合わせて重要視されています。
この記事では、プロセス保証と特殊工程の考え方、管理項目の事例、保証に使える便利ツール5選を紹介しています。
10年以上のプロセスエンジニア経験を元に実践のポイントを解説しますので、どのように実務に取り入れたらよいのか、お困りの方の参考になればうれしいです。
プロセス保証とは?
結果の保証とプロセスによる保証
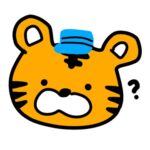
過程と結果のことだよね?
JIS Q 9027:2018によると、プロセス保証とは以下のように定義されています。
プロセスのアウトプットが要求される基準を満たすことを確実にする一連の活動。
注記:プロセス保証は、品質のプロセスでの作り込みを意図しており、これを具現化するべく、決められた手順及びやり方どおりに行うことで、プロセスの最終アウトプットを目的及び基準どおりになるようにするための一連の活動からなる。
引用元:JIS Q 9027:2018(マネジメントシステムのパフォーマンス改善ープロセス保証の指針)
プロセスとはインプットに対するアウトプットまでの過程を意味しており、モノづくりに当てはめると、製造工程そのものを表します。
つまり、材料、設備、作業方法をきちんと管理してプロセスを作り込むことで、アウトプット(出来栄えの品質)が要求仕様を満たすことを確実にするための活動です。
一方で、「プロセス保証」に対して、「結果の保証」という考え方もあります。
結果とは、まさにアウトプットのことで、外観検査や寸法測定など、プロセスのアウトプットとして得られた製品に対して品質を保証することを意味します。
プロセス保証では製品の製造過程で間接的に保証する考え方に対し、結果の保証では製品そのもので直接的に保証する対比的な考え方で、どちらも頭に入れておきましょう。
特殊工程との関係
特殊工程とは、完成品の検査では品質を保証することが困難な工程のことを意味しており、例えば、めっき、はんだ付け、接着、熱処理などの工程が該当します。
これらの工程では、外観検査や寸法・形状測定などによって健全性を示すことができません。
例えば、めっき皮膜の膜質や、はんだ付けの接合界面の状態など、破壊試験で特別な分析を行わない限り、良し悪しを判断できません。
このような特殊工程の品質保証には、プロセス保証が適用されます。
つまり、材料、設備、作業方法を規定・管理することによって、設計品質(狙いの品質)を満足する考え方で、特殊工程とプロセス保証には密接な関係があるのです。
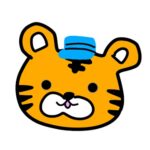
見えない部分はプロセスで保証しよう
プロセス保証を適用する目的
1.特殊工程の品質保証
プロセス保証の考え方を適用する最も大きな目的は、やはりプロセスでしか保証できないもの、すなわち特殊工程の品質を保証することです。
先に説明した通り、特殊工程は結果で品質保証ができないために、プロセスをきちんと管理せざるを得ないのです。
そうでない工程は管理不要という訳ではありませんが、特殊工程はプロセスがすべてと言っても過言ではないので、特に重点的な管理が必要となります。
2.検査コストの削減
製品の全数検査であれば、経年劣化などの寿命故障を除いて、初期故障品の流出の可能性がゼロであることを保証できます。
しかし、たとえ全数検査をやれば疑義品を全てスクリーニングできるといっても、検査コストが膨大になってしまいます。
そして、検査コストを抑える手段としては、抜取検査、あるいはプロセス保証で検査レスにすることが考えられます。
工程能力が十分過ぎるほどあって、万が一、不良品が流出しても、ppm(100万分の1)単位で許容範囲内と判断できる場合には、検査レスにする選択肢もあります。
3.製造現場の風土醸成
プロセス保証の考え方は、製造部門の品質意識の向上にもメリットがあります。
最終検査で歯止めをかけられるから適当な管理でOKという考え方では、当然ながら不良率は下がりません。
最悪の場合、不具合が出て波及範囲を調べる時に、作業記録がなくて疑義品を全て廃却し、膨大なロスコストが発生するケースも考えられます。
プロセス保証を適用することで、5M+1E(Man、Machine、Material、Method、Measurement、Environment)管理をきちんと行う意識が現場まで定着し、安定したモノづくりの地盤を築くことができます。
保証に使えるツール5選
プロセス保証に使える便利ツールを紹介します。
①:管理図
管理図とは、 品質特性の折れ線データと中心線、管理限界線からなるグラフで、QC7つ道具の一つです。
一般的には、±3σで規定した管理限界線を基準に品質のトレンドを管理します。
統計的には±3σの範囲内に、99.7%が収まることになります。
管理限界線の逸脱は確率的には稀な事象で、工程に何らかの異常が生じている可能性があり、管理図によって兆候を迅速に見つけ出すことができます。
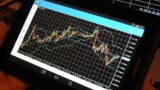
②:ヒストグラム
ヒストグラムは、縦軸に頻度、横軸に階級をとった統計グラフで、同じくQC 7つ道具の一つです。
データを区間に分け、各区間の頻度を棒状にグラフ化したもので、全体の分布を視覚的に捉えられるので、安全余裕度を確認しやすい利点があります。
異常原因が抑えられて管理の行き届いた工程では、品質特性のデータは正規分布に従うことが多いです。
ヒストグラムの分布形状に何らかの異常が見られた場合は、工程管理や規格値(しきい値)が適正でない可能性があるので、プロセスの健全性の確認に有効です。
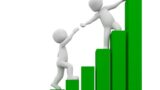
③:工程能力指数
規格の範囲内で製品を作ることのできる能力を数値化したもので、代表的なものにCp(シーピー)とCpk(シーピーケー)があります。
指標の意味を端的に言うと、公差範囲に対して3σが何個分収まるかを表しており、標準偏差σ(ばらつき)の値が小さいほど安定した工程と言えます。
プロセス保証と工程能力指数は切っても切れない関係で、プロセスで品質を保証できる実力値があるかどうか、その判定基準はまさに工程能力指数が担っているのです。
プロセスで品質を担保するには、Cp、Cpkの数値は1.33以上(不良の発生確率が10万分の6以下)を目指しましょう。
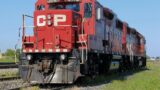
④:工程FMEA
FMEAは、想定される製品の故障モードをランク付けし、点数の高い項目を見える化して対策の方針や優先順位を決めるための解析手法です。
工程FMEAでは各工程での故障モードを一覧化できるので、工程の全体像や故障のインパクトの大きい工程を把握することができます。
例えば、ひとつの製品に複数の特殊工程がある場合には、優先順位を付けてプロセス保証の検討を進めなければなりません。
そんな場合に、影響度の大きさを考慮しつつ、かつ対象工程に確実に漏れがないようにするために、工程FMEAが活用できるのです。
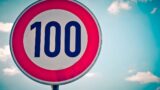
⑤:QAネットワーク
品質保証項目と工程手順をマトリックスにして、どの工程で不具合の発生と流出を防止するのか、点数化して把握するための分析手法です。
一つの不具合が複数の工程で生じる可能性のある場合に、FMEAでの検討漏れを補うのに有効に活用できます。
QAネットワークでは、目標レベルに対しての現状を一覧化することで、どの項目の防止策が不十分なのか、視覚的にも把握しやすいことがメリットです。
また、自工程完結(自らの工程で品質を保証して完結させる考え方)が出来ている工程と、そうでない工程も明確にすることができます。
そのため、プロセス保証にあたっては、発生防止、流出防止、自工程完結に問題がないか、工程全体を見渡して確認するようにしましょう。
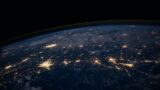
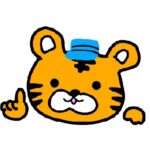
QC7つ道具には他にも使えるものが多いよ
実践のポイント
1.結果の保証とプロセス保証は一対
結果とプロセス、結局どちらが重要かと疑問に思われるかもしれませんが、これらは一対の関係にあるもので、結論としてはどちらも重要です。
先に説明した通り、特殊工程のように、結果の保証だけでは担保できないものもあります。
その一方で、「完璧な」プロセス保証はないことも事実であり、どんなに工程をしっかりと管理していても、突発的な原因で不良が発生・流出することは避けられません。
あくまで、工程能力の考え方に基づき、発生確率をできる限り抑える思想の活動ですので、誤解しないようにしましょう。
やはり、どちらか一方ではなく、プロセスと結果の両方をコントロールしてこそ、本当に作りこまれた工程と言えるのです。
2.管理項目は5Mを+1E意識する
特殊工程の管理項目に不備がないかどうか確認するには、5M+1E(Man、Machine、Material、Method、Measurement、Environment)を意識することをおススメします。
一例を挙げると、具体的には以下のような項目が管理対象になります。
Man(人):認定作業者、定期教育制度など
Machine(機械):設備(号機の指定)、ツール、治具など
Material(材料):材料ロット、投入量など
Method(方法):加工条件、加工順序、処理バッチ数など
Measurement(測定):設備(機器の指定)、測定方法、判定基準など
Environment(環境):温度、湿度、暴露時間など
このような観点で影響要因を抽出し、管理を厳しくする、もしくは管理幅の上下限で品質に問題のないことを確認することで、工程能力を高いレベルで維持できます。
3.数字が苦手でもσだけは覚えよう
複雑な計算式や、数字の取り扱いが苦手、という方に向けては、とにかく標準偏差(σ)だけは使いこなせるようにしておきましょう。
ツール5選でも紹介した通り、管理図や工程能力指数、どちらも標準偏差を基準に工程の安定性を判断しています。
標準偏差は、膨大なデータからばらつきを表現するのに優れた指標で、Excelを使えば一瞬で計算することができます。
σが計算できれば、あとは四則演算で管理図も工程能力指数も求められるので、工程管理に必要な基本ツールを使いこなすには十分でしょう。
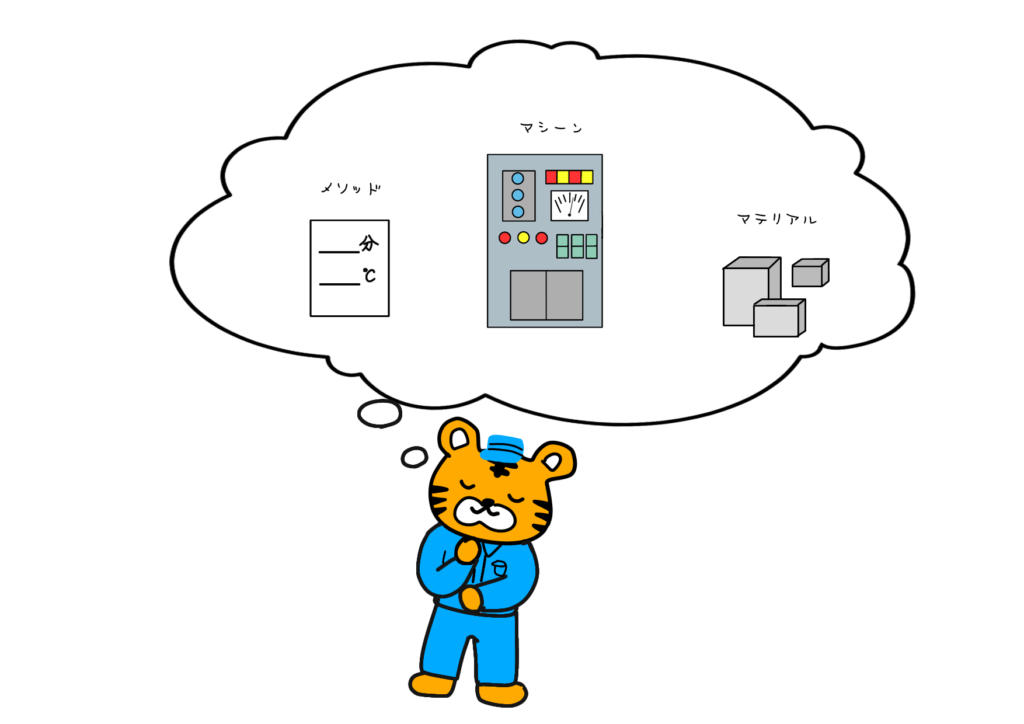
こてつ経験談
特殊工程しかない製品
過去に電子部品のアセンブリ工程を担当したことがあるのですが、その製品はほぼ特殊工程だけで構成される製造フローでした。
部品のめっき処理から始まり、接着、圧着、圧接、はんだ付け、溶接、ロウ付け、熱処理、シンタリング(焼結)、塗装の工程が一つの製品に詰まっていました。
思いつく特殊工程を全部並べただけじゃないの?とツッコミたくなりますが、これが本当の話で、出荷前検査の段階では外観以外ほとんど何も見えない状態でした。
実際にここまで集約される製品は多くないかもしれませんが、めっき、接着、はんだ付けのような技術は広く適用され、複数の特殊工程があるのは決して珍しくありません。
そして、このような製品では、何の不良がどこの工程で顕在化し、どこで歯止めをかけられるか、ひとつの故障モードだけでも工程全体を考慮する必要があるのです。
先ほど説明した、工程FMEAやQAネットワークは、まさにこの製品のプロセスを作り込む上で活躍しました。
結局のところ、複雑すぎて頭の中だけでは整理が追いつかなかった、ということです。
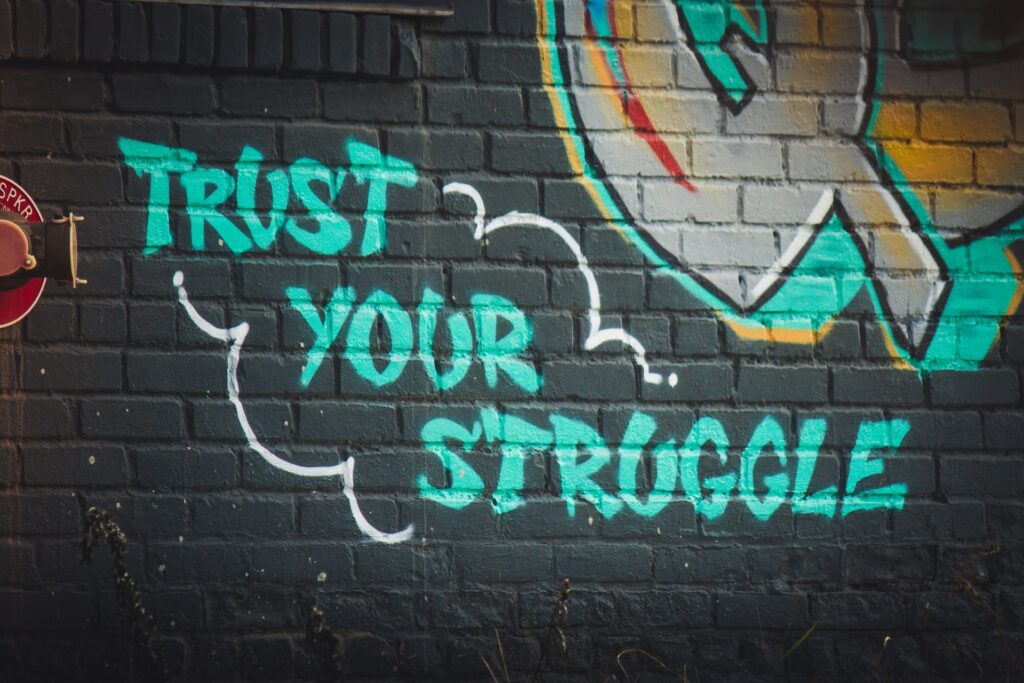
プロセス設計の腕の見せ所
特殊工程やプロセス保証と聞くと、責任が重そうで後ずさりしてしまいたい気持ちは分かりますが、モノづくりに携わる中では避けては通れません。
考え方によっては、プロセス設計が製品の品質を担っているということであり、プロセスエンジニアの腕の見せ所というわけです。
今回の記事では解説を省略しましたが、特性要因図や連関図法、マトリックスデータ解析法などを用いた要因分析もプロセス構築の源流にあたる重要な検討要素です。
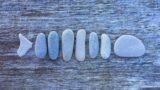
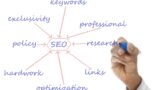
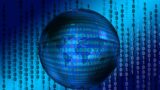
要因分析に始まり、5M+1Eで管理項目を網羅、FMEAやQAネットで管理の漏れを防止、管理図やヒストグラムでトレンド管理、最後に工程能力で実力を評価する。
このような一連の検討の流れを踏んで確立されたプロセスでは、特殊工程であろうと、やはり安定した成果の得られることが多いです。
また、プロセスの妥当性をロジカルに説明して、関係部門や顧客の合意を得ることは、ある意味でプロセスエンジニアの仕事の達成感や原動力に繋がるのかもしれません。
前向きにとらえて、プロセス設計が先導して品質を作り込んでいきましょう。
まとめ
- プロセス保証
⇒材料、設備、作業方法をきちんと管理してプロセスを作り込むことで、アウトプット(出来栄えの品質)が要求仕様を満たすことを確実にするための活動 - 結果の保証
⇒製品そのものに対して直接的に品質を保証すること - 特殊工程
⇒完成品の検査では品質を保証することが困難な工程 - プロセス保証を適用する目的
⇒特殊工程の品質保証
検査コストの削減
製造現場の風土醸成 - 保証に使えるツール5選
⇒管理図、ヒストグラム、工程能力指数、工程FMEA、QAネットワーク - 実践のポイント
⇒結果の保証とプロセス保証は一対
管理項目は5Mを+1E意識する
数字が苦手でもσだけは覚えよう
プロセス保証は、設計力、現場力の底上げに繋がる重要な考え方です。今回紹介したツールを参考に、ぜひ実践してみてください。
コメント