「PDPC法とは、どんなものか?」
「どんな場面で使うのか?」
「フローチャートを作る手順を詳しく知りたい」
このような疑問・悩みをお持ちの方に向けた記事です。10分で理解できるよう、わかりやすく簡潔に解説します。
PDPC法は、新製品の開発や客先対応の案件など、予測困難な状況に陥るリスクのある場合に活用するフローチャートです。
矢印と図形が複雑に入り組んだフローチャートは難しそうな印象がありますが、具体例を挙げてステップごとに作り方の手順を解説しますので、参考にしていただければと思います。
PDPC法って何?
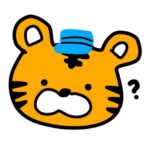
何の略称?
PDPC法とは
PDPCとは、「Process Decision Program Chart」の略で、日本語では「過程決定計画図」と言われています。
目標達成までに不測の事態が生じることを想定して、あらかじめ対応策をフローチャートにして計画する手法のことで、新QC7つ道具の一つとして活用されています。
PDPCの構成
以下のPDPCの一例を示します。
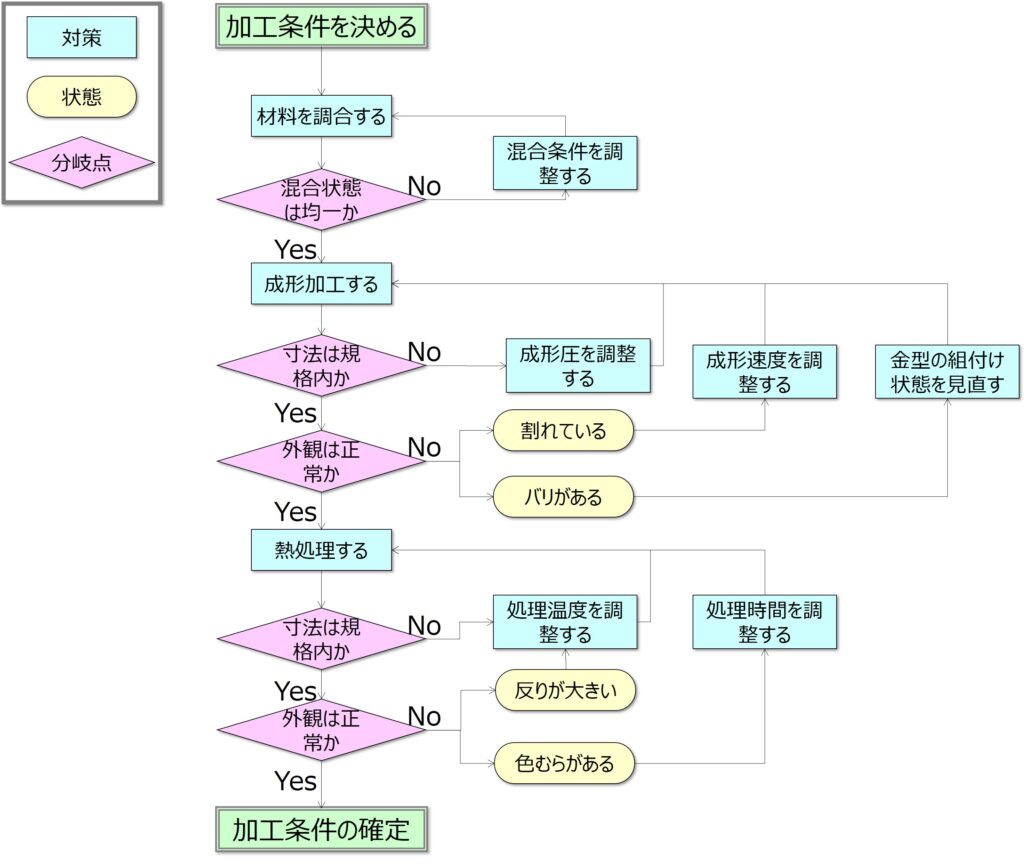
図で使用する記号は、以下のように定義されます。
□:対策(その時に取るべき処置)
○:状態(起こりうる状況)
◇:分岐点(状態が2通りに分かれる状況)
矢印(実線):時間経過を伴う順序
矢印(点線):時間経過の無い順序
分岐点では、必ずYesかNoに分かれます。
全体の構成としては、上から下、左から右に向けて状態の進行を表しています。
図形と矢印でフローチャートにする図式としては、アローダイアグラムと似ていますが、PDPCの場合は、ループするサイクルが許されています。
アローダイアグラムの場合は、もともとの目的が日程を計画する性質から、時間に関する順序が重要であり、時間の逆戻りを意味するフィードバックのサイクルは許されていません。
一方、PDPCは状態の進行を表すことが重要であり、いろいろな順序を経て、同じ状態に戻ってくることは、検討の過程で問題のない流れです。
強制連結型と逐次展開型
PDPCは、作り方によって2つの種類に分かれます。
強制連結型
計画時に不測の事態を予測して、あらかじめ打開策を織り込んでおく。スタートからゴールまで、必ず経路がつながっている。
逐次展開型
不測の事態が発生した都度、その打開策を考え、計画を修正しながら最悪の状態を回避する。打開策がなく、途中で途切れる場合もある。
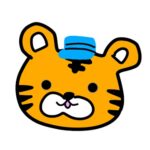
最初にどちらを使うか決めておいた方が良さそうだね
なぜPDPC法を使うの?
目的・用途
- 対応策の事前準備
- 最適なプロセスの検討
- 情報の共有
メリット
- 対応策の事前準備
フローチャートにして、想定される状況をあらかじめ整理しておくことで、実際に問題が起こった場合に、迅速に適切に対応することができます。 - 最適なプロセスの検討
状態の全体像と対処方法の流れを一覧にして表すことで、その時々の状況に応じた最適なプロセスを選択することができます。 - 情報の共有
図式化して情報資産として残すことで、第三者と情報を共有する際にも活用できます。
どんな場面で使うの?
PDPC法を2つの種類にわけて、活用例の一部を紹介します。
【活用例①】製造条件の調整
強制連結型PDPCの活用例としては、以下のような製造条件を決めるフローチャートに適しています。
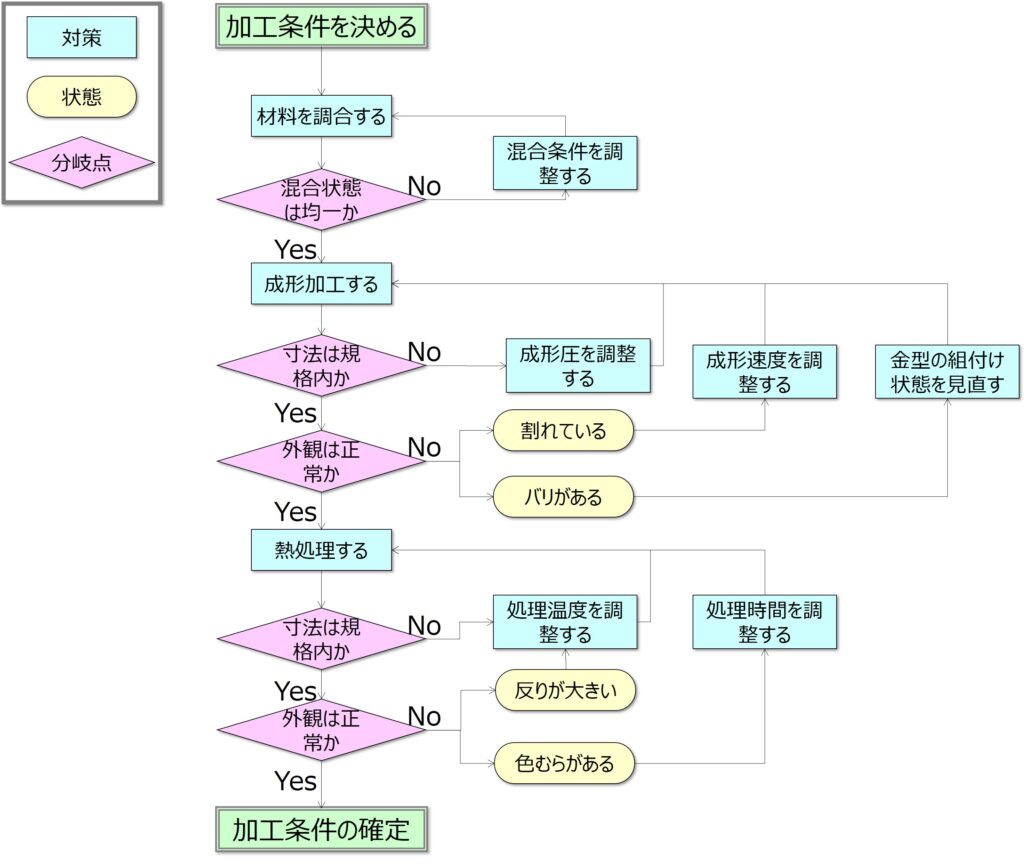
例えば、スタートを「加工条件を決める」、ゴールを「加工条件の確定」と設定します。
スタートからゴールに向けてまっすぐ下に繋がる経路は、理想的な状態を表す最短ルートです。
その途中段階では、四角で示す製造パラメータの調整という対策行為が入っています。
また、ひし形で示す分岐点は、品質の確認行為を表しており、適切な状態でなければ条件を再調整して、また同じルートに戻ってくる順序をたどります。
丸印は状態を表しており、その状態によって取るべき対応策が分かれる場合もあります。
このように、製造パラメータを一覧にして把握できるだけでなく、どういう場合にどのパラメータを調整すればよいのか、最適な手順を踏んで条件調整を進めることができます。
【活用例②】改善策の絞り込み
逐次展開型PDPCの活用例としては、以下のように改善策の中から有力候補を絞り込むことに役立ちます。
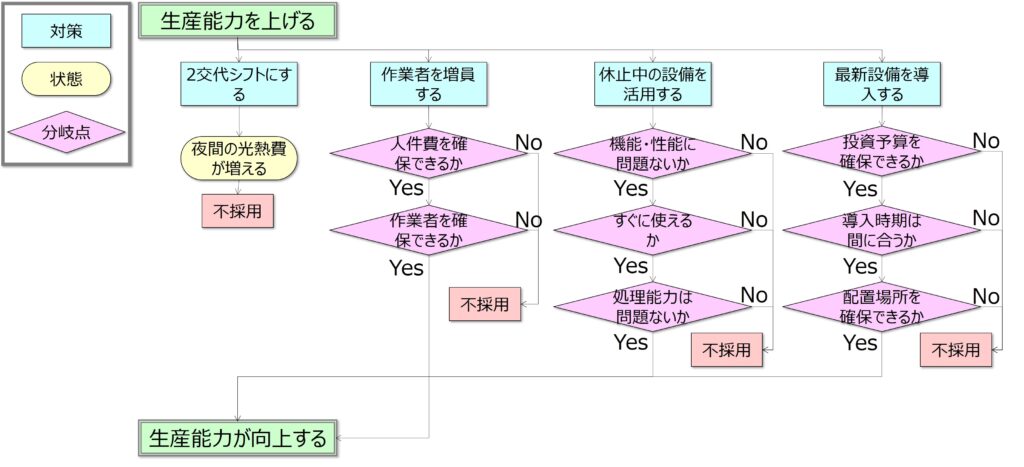
例えば、スタートを「生産能力を上げる」、ゴールを「生産能力が向上する」と設定します。
四角で示すのは、改善策の候補であり、複数に枝分かれしています。
その先では、それぞれの候補に対し、良し悪しを判断する分岐点が待ち受けており、選定基準をクリアしたものが候補として残ります。
多くの候補を絞り切れずに迷っている場合に有効で、新QC7つ道具の系統図法で抽出した候補をPDPC法のフローに沿って絞り込んでいく、複合的な活用方法も覚えておくとよいでしょう。
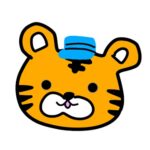
組み合わせて活用すれば、効果倍増!
どうやって作るの?
手順
- 目的を整理する
- スタートとゴールを決める
- 最短ルートを決める
- 不測事態が想定されるポイントを検討する
- 不測事態への対応策を検討する
- 体裁を整えて完成させる
- 目的を整理する
まず、PDPCを作成する目的を決めます。
目的を整理したら、強制連結型と逐次展開型のどちらで検討を進めるか、イメージを付けておきます。
今回は、先ほどの活用例でも紹介した強制連結型PDPCの作成手順を解説します。 - スタートとゴールを決める
計画のスタートとゴールを設定します。
今回は、スタートを「加工条件を決める」、ゴールを「加工条件の確定」と設定します。 - 最短ルートを決める
次に、スタートとゴールを最短経路で結ぶ、理想的なルートを作成します。
基本的には実施事項を順番に並べていけばよいのですが、あとで不測事態の枝分かれを考える準備として、「対策」と「確認」の区別を意識しておくとよいでしょう。
今回は、対策として「パラメータの調整」、確認として「できばえの確認」と大まかに分類して並べています。 - 不測事態が想定されるポイントを検討する
最短ルートが決まったら、不測事態が想定されるポイントを考え、分岐点として、ひし形で表記します。
先ほどの「できばえの確認」で表記した項目は、分岐点として合否を判断する表記に変更する必要があります。
また、確認項目が複数ある場合は、ひし形を複数並べて、それぞれに対して枝分かれするようにしておきます。 - 不測事態への対応策を検討する
さらに、不測事態への対応策(打開策)を記入していきます。
分岐点で不適合と判断された場合は、条件を再調整して、また同じルートに戻ってくる順序をたどります。
また、丸印で示すように、不適合な状態(不良モード)を複数に分けておくと、その状態に応じて適切な処置を取ることができます。 - 体裁を整えて完成させる
最後に、矢印が交錯していないか、強制連結型の場合はすべての項目が矢印で結ばれているか、確認して体裁を整えれば完成です。
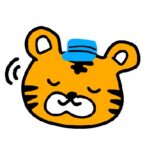
最短ルートを決めるところで、大筋の枝分かれが決まるんだね
PDPCを作るポイント
- 前提条件を決めておく
- 要素をリストアップしておく
- 補足説明を残しておく
- 前提条件を決めておく
PDPCは不測事態を網羅的に整理する有効な手法ですが、なんでもかんでも項目を挙げると、全体が膨らみすぎて、本質の見極めが難しくなります。
こういう場合は、あらかじめ対策の前提条件を決めておくと有効です。
例えば、お金や設備や人など、対策に制限のある場合は、前提条件として冒頭に記載し、これを除いてPDPCにすると、すっきりと整理できます。 - 要素をリストアップしておく
フローチャートの項目に漏れがあっては、対応策も適切なものにはなりません。
そのため、いきなりフローチャートを書き始めるのではなく、しっかりと事前検討して要素をリストアップしておくことをお勧めします。
先ほど紹介した製造条件の事例の場合、以下を分類して整理しておくと、図示する際に手早く進めることができます。
対策(四角):調整パラメータ
状態(丸):不具合モード
分岐点(ひし形):確認項目 - 補足説明を残しておく
フローチャートは、見栄えがすっきりして分かりやすいメリットがありますが、情報資産として残す場合には、説明不足になりがちです。
フローチャートの中で、確認が必要な理由や、合否判定の目安など、追加説明が必要なものは、補足資料にして、セットで残しておくとよいでしょう。
まとめ
- PDPC法
⇒目標達成までに不測の事態が生じることを想定して、あらかじめ対応策をフローチャートにして計画する手法のこと。
⇒PDPC(Process Decision Program Chart:過程決定計画図)には、強制連結型と逐次展開型がある。 - 目的・用途
⇒対応策の事前準備、最適なプロセスの検討、情報の共有 - 作るポイント
⇒①:前提条件を決めておく
②:要素をリストアップしておく
③:補足説明を残しておく
PDPCを活用することで、不測の事態が生じた場合に、迅速に適切に対応することができ、早期に問題解決を図ることができます。
実際に、不測の事態に陥らなくても、普段からリスクを想定して計画に織り込む考え方はとても重要ですので、ぜひ活用してみてください。
コメント