「QAネットワークって何のために使うの?」
「工程FMEAとの違いが分からない」
「作り方と点数付けの判定基準を知りたい」
こんな疑問や悩みをお持ちの方に向けた記事です。
QAネットワークとは、品質保証項目と工程手順をマトリックスにして、どの工程で不具合の発生と流出を防止するのか、点数化して把握するための分析手法です。
トヨタグループで考案された手法で、現在は多くの企業で品質保証レベルの見える化に有効なツールとして活用されています。
この記事では、QAネットワークという言葉を初めて聞いた方でも分かるよう、活用する目的とメリット、作り方の手順、点数付けの基準について、具体例を交えて解説します。
また、故障モードを分析する類似の手法として、工程FMEAとの違いについても説明しますので、ぜひ参考になればうれしいです。
QAネットワークとは?
QAネットワークの構成
早速、構成を見てみましょう。
表の縦と横に項目が配置されており、その交点に数値が2段に分けて書かれています。
縦軸には品質保証項目または不具合項目、横軸には工程の手順を記載します。
縦軸と横軸の交点の数値は、上段が発生防止、下段が流出防止を表しており、それぞれ4段階で点数化され、数値の小さいほどレベルの高いことを意味しています。
交差する場所に記載するのは、どの工程で何の不具合項目が出るのか、という対応を表しています。
つまり、品質保証項目に対する各工程での保証度合いを見える化したもので、網目のような見た目から「保証の網」とも呼ばれています。
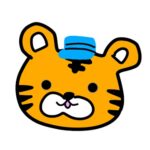
ひと目で工程と保証項目が把握できるね
工程FMEAとの違い
各工程で発生しうる不具合項目を点数化して影響度合いを分析する手法として、工程FMEA(Failure Mode and Effects Analysis:故障モード影響解析)があります。
工程手順と不具合項目を対応付けて点数化する、という意味では共通した特徴があり、紛らわしい原因でもあります。
工程FMEAの特徴としては、その名の通り「影響を解析する」ことにあります。
不具合(故障モード)がどのような影響に繋がるのか、その影響度合いはどの程度か、といった「影響」に着目して分析します。
そして、発生と流出防止の機能も踏まえてリスク優先度を算出して、点数の高いものから対処するといった使い方をします。
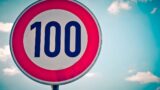
一方、QAネットワークの特徴は、マトリックスになっている点です。
一つの不具合が必ずしも一つの工程だけで発生するとは限りません。
複数の工程にまたがる場合に、FMEAでは見落としの生じる可能性があり、まさに保証の網として、漏れなく対象工程を抽出することがQAネットワークの利点でもあります。
目的・メリット
1.防止策が必要な不具合の見える化
QAネットワークでは、品質保証項目または不具合項目に対し、発生防止と流出防止のレベルをそれぞれ数値化して表します。
目標レベルに対しての現状を一覧化することで、どの項目の防止策が不十分なのか、視覚的にも把握しやすくなります。
2.不具合が発見される工程の見える化
工程FMEAとの違いでも説明したように、QAネットワークでは不具合が複数の工程にまたがる場合にも、網羅的に表現することができます。
とある不具合が、自工程で検出可能なのか、あるいは後工程になってから顕在化するのか、影響の大きさも変わってきます。
自工程完結(自らの工程で品質を保証して完結させる考え方)が出来ている工程と、そうでない工程、QAネットワークで一覧化すれば簡単に把握できます。
3.顧客への説明資料
自社内での分析資料としての用途だけでなく、顧客向けの説明資料としても活用することができます。
QAネットワークは、工程全体と不具合項目を一覧で捉えられる見た目の分かりやすさがメリットです。
そのため、長々と説明文を記載するよりも、ひとつの表で表現した方が伝わりやすいこともあります。
また、顧客側の立場から見ても、仕入先がQAネットワークで自社の工程分析をやっているというのは安心材料になるので、信頼を得る上でも有効と考えられます。
作り方の手順
QAネットワークの作り方を説明します。
マトリックスの項目を埋める
1.横軸の項目
まず、横軸の項目として、製造フローに沿った工程を記載します。
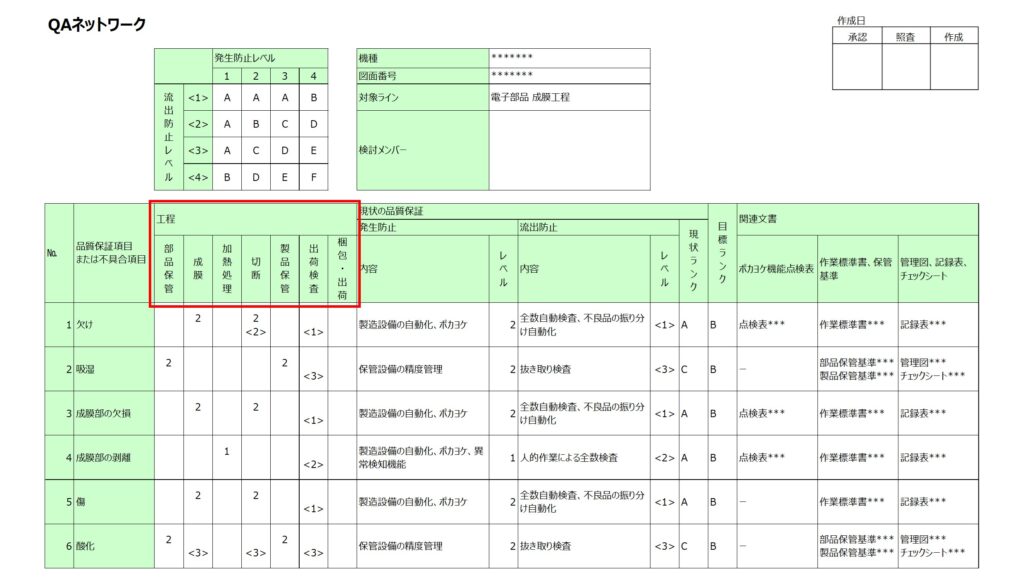
工程の流れは、QC工程表に従って漏れなく挙げるようにしましょう。
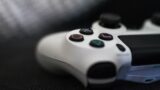
2.縦軸の項目
次に、縦軸の項目となる品質保証項目または不具合項目を記載します。
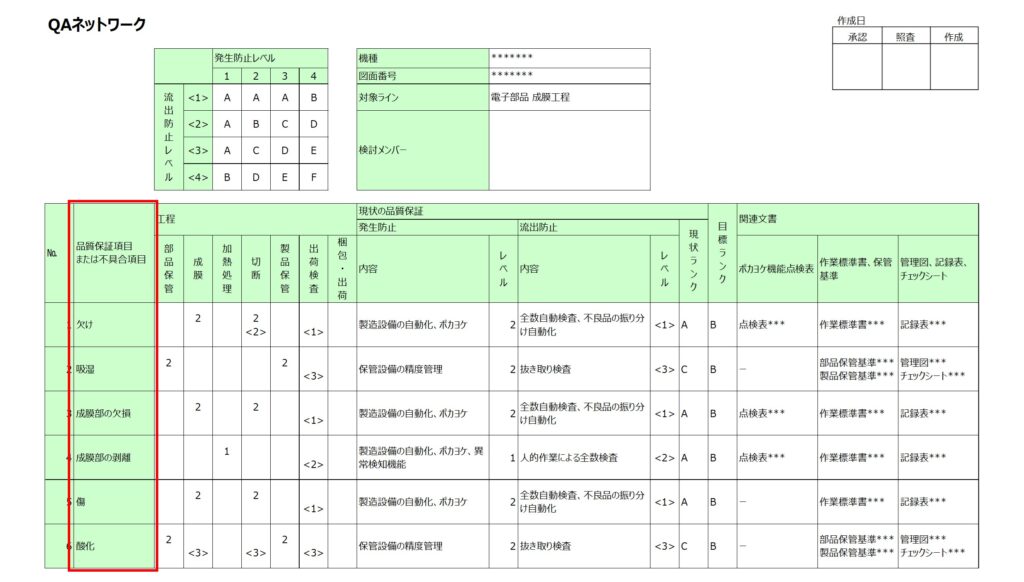
図面や検査規格で規定する項目に関しては、確実にリストアップするようにしましょう。
その他、設計審査で抽出した想定の不具合項目なども盛り込むと、抜け漏れにくくなります。
特に、既存設計、既存プロセスからの変更にあたっては、変更に伴うリスクが内在しており、DRBFMを活用して想定不具合を洗い出しておくことが望ましいです。
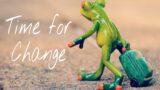
レベル分け、ランク付けする
3.発生防止レベル
マトリックスの軸が完成したら、次は交差するセルの上段に発生防止レベルを記載します。
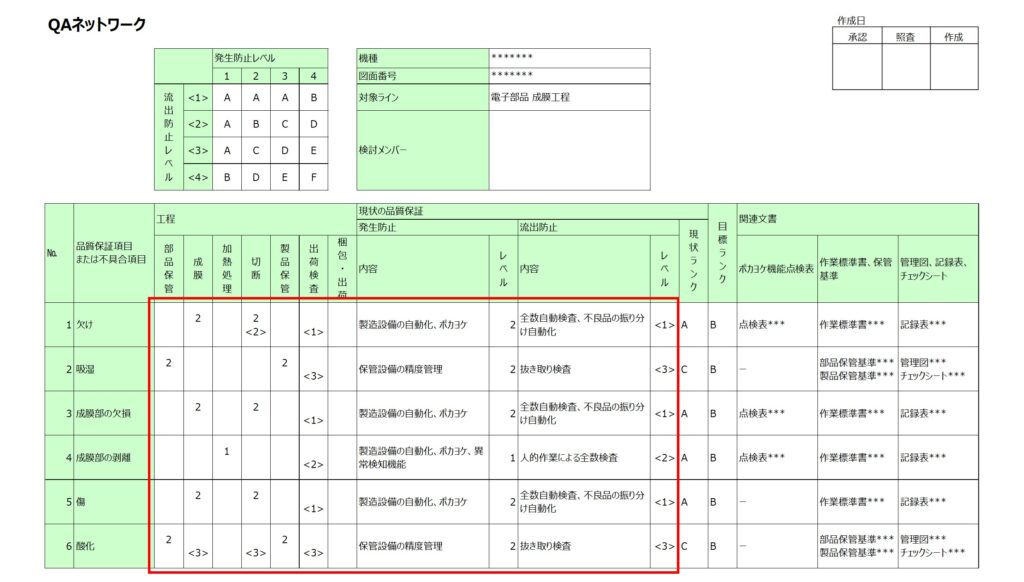
それぞれの不具合項目に対し、どの段階で発生するのか、工程順に追って該当箇所を見つけ出します。
そして、該当箇所のセルに、レベル分けした数値を4段階で記載します。
判定の目安は以下を参考にしてみてください。
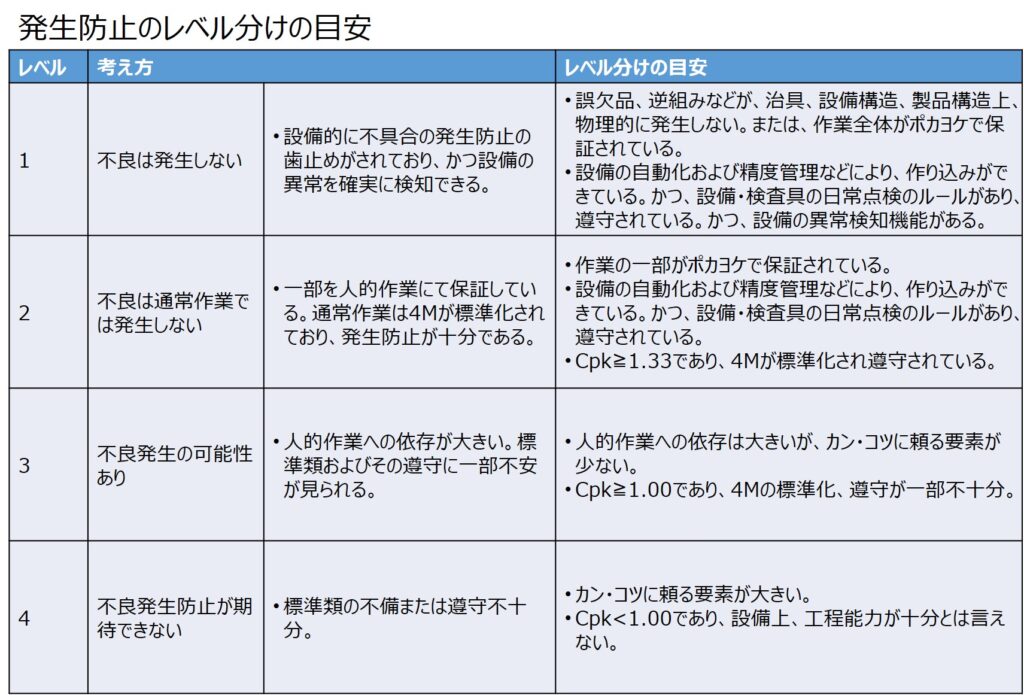
4.流出防止レベル
上記と同じ要領で、セルの下段に流出防止レベルを記載します。
レベル分けの考え方も基本的には発生防止と同じで、判定の目安は以下の通りです。
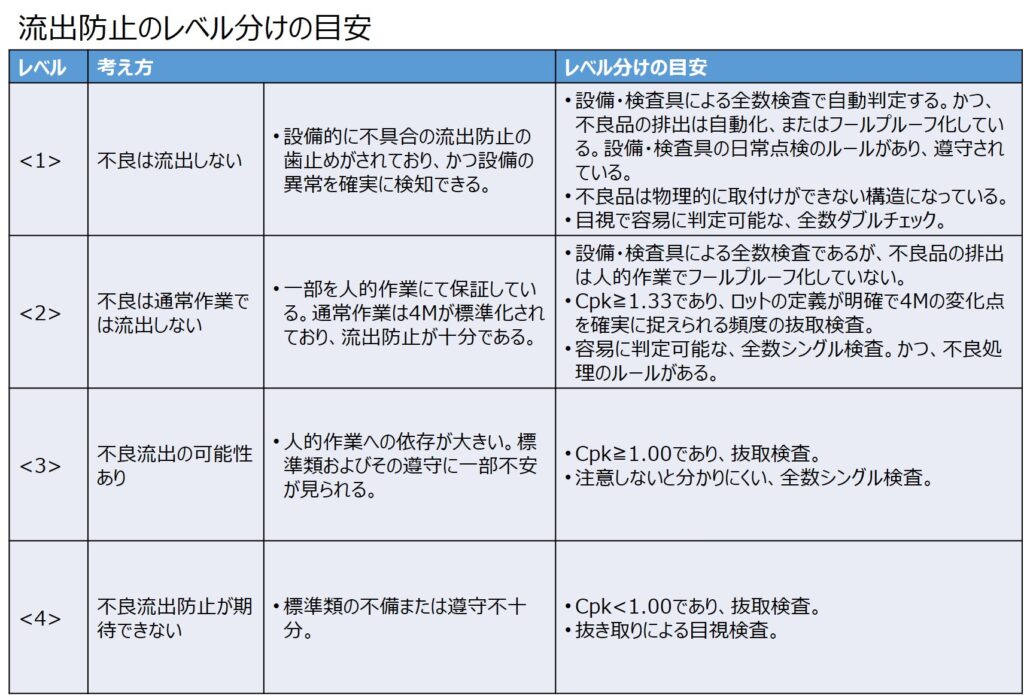
5.現状ランク、目標ランク
発生防止レベルと流出防止レベルをすべて埋められたら、それぞれの不具合項目に対し、ランク付けをしていきます。
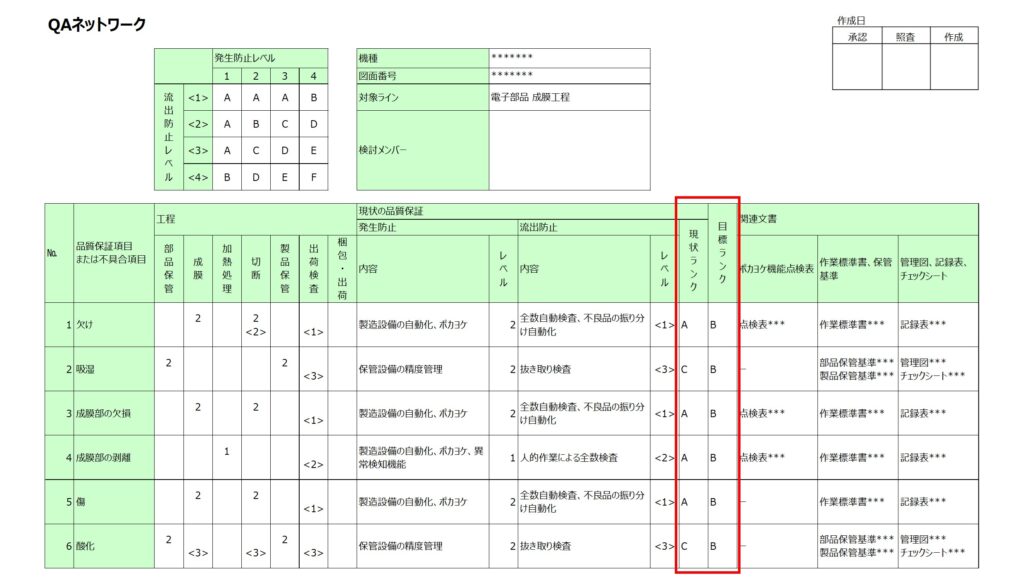
ランク付けは、以下の表に従って機械的にA~Fの6段階に決められます。
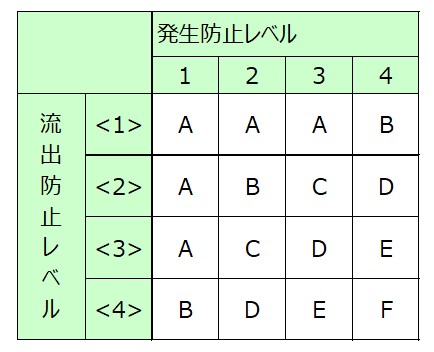
例えば、とある工程で発生した不具合に対し、複数の工程で流出防止できるのであれば、レベル数値の最も小さい(防止レベルが高い)ものを選びます。
これは、仮に一つの工程で流出してしまっても、その他で何重にも関門があるため、最終的に最も流出防止レベルが高い基準で歯止めがかけられるためです。
6.関連文書
ポカヨケや作業標準書、管理図など、関連文書を記載します。
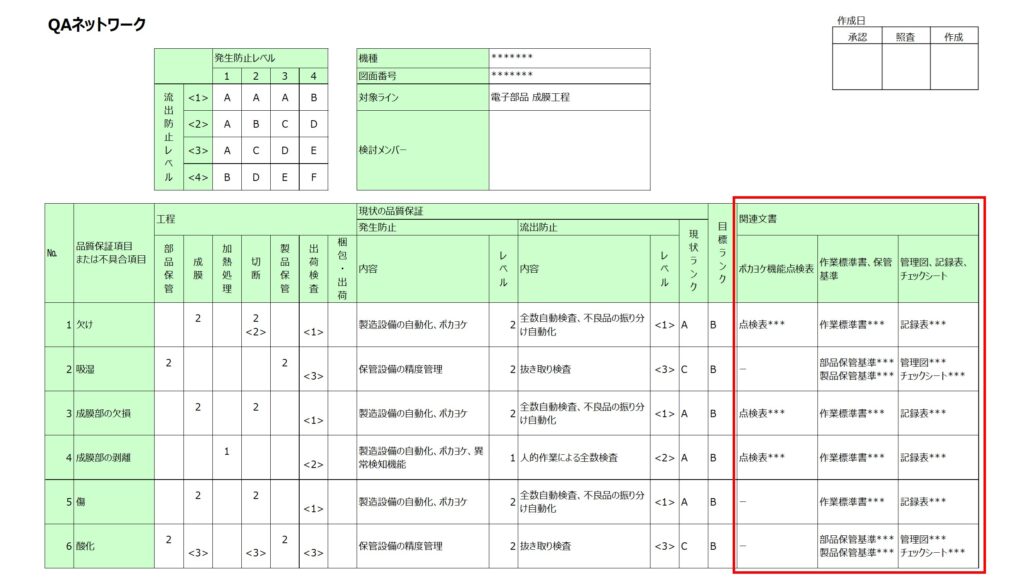
不具合項目と対応付けることで、どの不具合が何のドキュメントに基づいて作業・管理されているのか、把握しやすくなります。
分析した結果をまとめる
7.課題抽出
最後に、分析の結論として、課題抽出を行いましょう。
目標ランクと現状ランクの差異を確認して、弱点となる工程や不具合項目を洗い出します。
目標ランクに満たないものは、改善計画を立てて対処し、PDCAサイクルを継続的に回していくことが重要です。
作る時のポイント
1.行と列の抽出に時間をかける
QAネットワークは、その名の通り網羅的に保証項目と工程を見える化する手法です。
網羅的という表現の副作用として、最初に作成するときに抽出が漏れると、後から気づきにくい性質があります。
レベル分けの区分などは、後に見直して改定することも容易ですが、保証項目と工程に関しては、そう簡単に改定する訳にはいきません。
そのため、最初に作成する段階で、急いでレベル分けの作業に移らず、項目の抽出にしっかりと時間をかけるようにしましょう。
2.防止策の具体的な内容を書く
発生防止と流出防止のレベル分けの際に、合わせて具体的な防止策の内容を記載するようにしましょう。
判定の目安は作成手順の中で説明した通りですが、あくまで抽象的な表現に過ぎず、また、全ての項目が合致するとは限りません。
後々になって、判定の根拠を振り返った時に、なぜそのレベルに区分したのか分からなくなってしまう恐れがあります。
そのため、具体的にどの項目が該当するのか、対応付けが分かるようにしておくことをおススメします。
3.多角的な視点で検討する
設計、製造、品質管理など、モノづくりに携わる関係部門の全体で検討するようにしましょう。
例えば、設計部門が期待している流出防止と、品管部門が実力値として把握している流出防止のレベルには食い違いがあるかもしれません。
また、設計部門が見落としている不具合の発生工程も、製造現場では把握できているかもしれません。
このように、部門が違えば点数化する判断基準も変わってくるので、多角的な視点で検討することで、より客観的なランク付けを行うことができます。
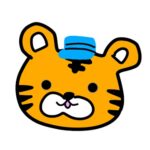
色んな見方が発見できて参考になるね
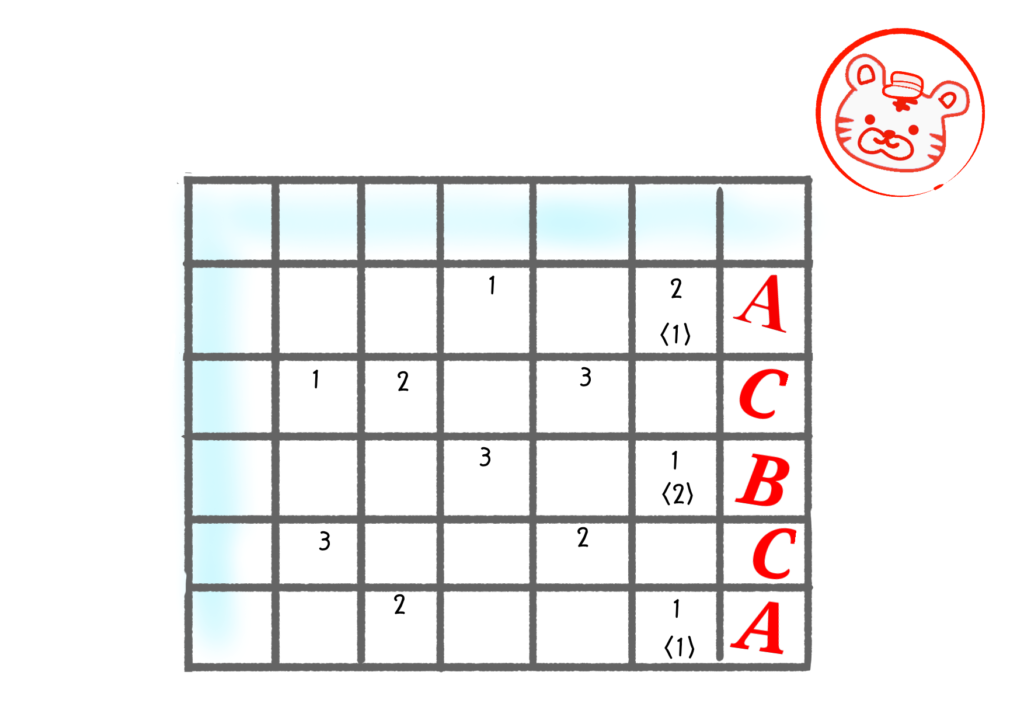
まとめ
- QAネットワーク
⇒品質保証項目と工程手順をマトリックスにして、どの工程で不具合の発生と流出を防止するのか、点数化して把握するための分析手法 - 工程FMEAとの違い
⇒FMEAは、故障モードが製品に与える「影響」に着目した分析手法
⇒QAネットワークは、不具合が複数の工程で発生する場合に網羅的に抽出するのに便利 - 目的・メリット
⇒防止策が必要な不具合の見える化
不具合が発見される工程の見える化
顧客への説明資料 - 作る時のポイント
⇒行と列の抽出に時間をかける
防止策の具体的な内容を書く
多角的な視点で検討する
いきなり完成版のQAネットワーク表を見たら、構成が複雑で取りつきにくい印象ですが、手順を踏めば難しくありません。
自分たちの工程の品質保証が、どの程度の網目で構築されているのか、ぜひ検討の参考にしてみてください。
最後まで読んでいただき、ありがとうございました。
この記事で紹介したQAネットワークは、品質保証の分析手法の一つです。
製造業に携わるエンジニアであれば、その他の手法はもちろんのこと、品質管理、生産の基礎知識を幅広く身につけておく必要があります。
社内講座などの機会が設けられている場合は、ぜひ若手のうちから積極的に活用して受講することをおススメします。
ただ、多くの社員を対象とする社内講座の場合、皆さん一人ひとりのレベルに適した学習ができない場合もあります。
忙しい日々の限られた勉強の時間を最大限に活かすためにも、自分の教育プランは自分で管理することを意識して、能動的に学習することも検討してみてはいかがでしょうか。
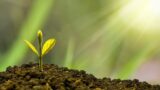
コメント