「初期流動管理って何?」
「具体的に何をやればいいの?」
「初期ってどのくらいの期間?」
こんな疑問や悩みをお持ちの方に向けた記事です。
新製品の立上げや製造プロセスの変更には、トラブルが付きものです。
初期流動管理とは、設計やプロセスの新規適用または変更の際に、量産の初期段階で通常よりも検出感度の高い品質管理を行うことで、不具合を未然防止する管理手法です。
この記事では、初期流動管理のメリット、管理項目の考え方、対象期間の目安について解説しています。
量産開始の初めに何を管理すれば良いのか、対応にお困りの方にとって、参考になればうれしいです。
初期流動管理とは
初期流動とは、量産の「初期」段階における製品の「流動」のことです。
開発試作と量産で大きく異なるのは、製造ロットという概念が加わり、ロットばらつきやロット数量の影響を考慮して、品質を維持しなければならないことです。
試作品では、予算や時間の関係上、量産を模擬できるだけの十分な数量を投入できないことが多いです。
このような制約の中でも、マトリックスデータ解析法や工程能力指数といった統計的手法を用いることで、工程の安定性や影響要因を推定することができます。
しかし、たとえ試作品で可能な限りの検証を行ったとしても、やはり量産では予期せぬトラブルが発生してしまいます。
材料ロットが変わった影響や、数を流して初めて顕在化する不具合もあり、品質の安定性を把握するには、量産初期でバグ出しを行う必要があります。
そのため、量産の初期段階で通常よりも検出感度の高い管理を行うことで、品質の実力値を把握して不具合を未然防止する考え方として、初期流動管理が重要視されています。
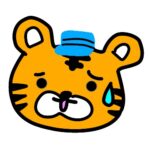
時間が経ってからトラブルが出たら困るもんね
目的とメリット
1.設計の妥当性確認
製品設計やプロセス設計の妥当性の確認は、開発段階での要素試作や量産試作(プリ・プロダクション、プリプロ、PP)で行うのが基本です。
しかし、前述の通り、試作レベルでは見えない要素もあり、量産の初期で設計検証の最終確認を行う必要があります。
管理コストの問題で、通常の運用では取得しないようなデータに関しても、初期流動管理のフェーズで取得することで、設計検証の裏付けに活用できるのです。
2.工程能力の見積り
量産を維持していくには、工程の安定性を把握する必要があります。
工程能力とは、規格の範囲内で製品を作ることのできる能力のことで、CpやCpkといった指数で表すことで、不良の発生確率を統計的に見ることができます。
工程能力指数は、量産試作で見積もることが多いですが、材料ロットやサンプル数が限定的な条件で求めることになるので、精度が良くありません。
初期流動管理で複数ロットの実力値を見ることで、工程能力の見積り精度を上げることができます。
3.品質への影響要因の抽出
量産の中でデータ取得を行うことで、今まで見えていなかった影響要因を見つけ出すことができます。
例えば、材料ロットの影響など、試作段階では相関関係が見えるほどのデータ数を取れないことが多いです。
新たな影響要因が見つかった場合は、図面や検査規格に落とし込むことで、設計保証外のものはリジェクトできます。
初期流動管理のやり方
具体的な進め方について、手順を踏んで説明します。
必要なタイミング
初期流動管理が必要となるのは、設計やプロセスの新規適用または変更の際、すなわち、新製品の立上げや設計・プロセス改善のタイミングです。
新規要素や変更点の裏側には、トラブルが付きものです。
変更に伴う懸念点を事前に洗い出して、デザインレビュー(DR)の段階でリスクを排除する解析手法がDRBFM(Design Review Based on Failure Mode)です。
しかし、DRの場では見えてこない潜在的なトラブルもあり、初期流動の段階で出し切ってしまうことが重要です。
管理項目の考え方
1.重要管理項目の抽出
初期流動管理をいつやるべきか明確になれば、次は管理項目を検討します。
イメージが付きやすいよう、セラミック基材に配線電極を成膜する部品を具体例として紹介します。
まずは、製品の性能に与える影響の大きい故障モードを想定し、その故障の原因になり得る要素を洗い出します。
故障モードの抽出には、FMEA(Failure Mode and Effects Analysis:故障モード影響解析)の手法を用いることで、点数化して優先度の高いものを客観的に選ぶことができます。
今回の事例では、故障の原因となり得る影響度の高い要素として、「電極の膜厚」を重要管理項目とします。
2.運用方法の検討
次に、重要管理項目をどのように管理するか、具体的な運用方法を検討します。
運用方法を決めるにあたっては、主に以下の3つの考え方があります。
①:管理する項目を増やす
通常よりも、管理する項目を増やす考え方です。
例えば、通常の運用では、出荷前検査にて製品の形態で膜厚を測定しているとします。
しかし、万が一、出荷前検査でNGになった場合は、ロット不良となって大きな損失を出しかねません。
ある程度の実績がある場合は、管理コストも踏まえて、最終検査のみの運用でも問題ありませんが、量産初期ではリスクが伴います。
そのため、通常の出荷前検査に加えて、成膜工程での膜厚検査を加えるなど、管理項目を増やす運用が考えられます。
これにより、成膜不良が出たとしても、自工程で不良を検出でき、被害を最小限に留めることができます。
まさに、「後工程はお客様」という品質管理の基本理念に基づいた考え方です。
②:記録内容を増やす
さらに別の考え方として、記録内容を増やす方法があります。
例えば、通常の検査では、膜厚を簡易測定してOK/NGの判定だけやっているとしましょう。
これには一長一短あり、わざわざ数値化しなくても良いので、例えば膜厚の規格範囲をゲージに示して、その範囲内に入っていることを目視確認する簡易判定の運用ができます。
一方で、定量化できないため、後で相関関係を分析したり、規格に対する余裕度を見たりすることはできません。
そのため、初期流動管理では膜厚の測定値まで記録するなど、より詳細な情報を残す運用例が考えられます。
③:頻度を上げる
最後は記録の頻度を上げることです。
例えば、通常は1日に1回の品質確認に対し、1日の最初と最後、あるいは休憩前後でデータを取得するなど、経時変化に対する情報を細かく分析したい場合に有効です。
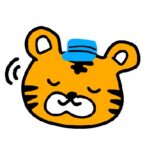
どんな情報が必要か次第ってことだね
管理の対象期間
管理ポイントが明確になったら、最後に気になるのは、いつまで継続すれば良いのかという点です。
初期流動管理の解除の判断は、明確な決まりはなく、それぞれの目的に合わせて決めるしかありません。
ただ、それでは何の目安にもならないので、いくつかの決め方の事例をご紹介します。
①:ロット数で決める
材料ロットや製造ロットなど、元々、ロットばらつきに不安がある場合に取る方法です。
量産試作では把握しきれない代表例としてロットばらつきがあり、規格上下限品の評価などを事前に実施していない限り、残念ながら実績を重ねるしかありません。
例えば、3ロットや5ロットなど、あらかじめ対象ロット数を決めて、その間に問題が生じなければ解除するという考え方です。
②:生産台数で決める
ロットの区切りなどが明確でない場合には、累積の台数で決める考え方があります。
例えば、1000個や10000個など、統計量を算出するにあたって十分な母数が確保できれば解除するということです。
統計的に意味のある数量を確保できれば、検定や推定値の精度も高くなり、さらに第三者に説明する上でも確率論を持ち出せるので説得力が違います。
③:歩留りの状況で決める
あらかじめ設定した目標の良品率に対する歩留りの達成状況を見て判断する考え方です。
例え、ロット数や台数で区切っても、大量に不良が出ている状況では、管理を緩くしている場合ではありません。
そのまま工程改善に注力すべきであり、工程分析にあたって重要管理項目のデータは大変貴重になってきます。
原因調査と改善に活用して、一定の目途が得られたら初期流動を解除すれば良いでしょう。
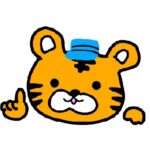
最初にみんなで解除の条件を決めておこう
実践のポイント
1.定量的にデータを残す
単に、OK/NGの合否判定を取る場合でも、通常より頻度を上げることは有効ですが、定量データを残すことで、さらに有効に活用することができます。
材料の検査成績書や製品の検査結果など、通常では数値管理していない項目でも、初期流動の期間できちんと測定値を残しておけば、後に分析の必要性が生じた場合に活躍します。
2.あえて意地悪な流し方をする
検出感度の高い期間に、あえて意地悪な流し方をして、バグ出しを行う考え方があります。
例えば、一日の生産量が日々変わる場合は想定される最大量を流すとか、あえて工程間の滞留時間を最大にして影響を確認する、などの事例があります。
このように、考えられる最悪状態を最初に確認しておくことで、ばらつきに強い工程を確立することができます。
3.管理の目的を忘れずに
悪い例として、何のために初期流動管理を実施しているのか、目的を見失ってしまう場合があります。
目的が明確でないと、ズルズルと引っぱって解除のタイミングを逃してしまいます。
あるいは、せっかく取得したデータが活かされず、ただただ問題ないことをチェックしたという確認行為だけで終わってしまいます。
多くのデータを取得するのは良いことですが、これにも管理コストがかかりますので、目的に沿わないものは可能な限り減らし、本当に必要なものを精査するようにしましょう。
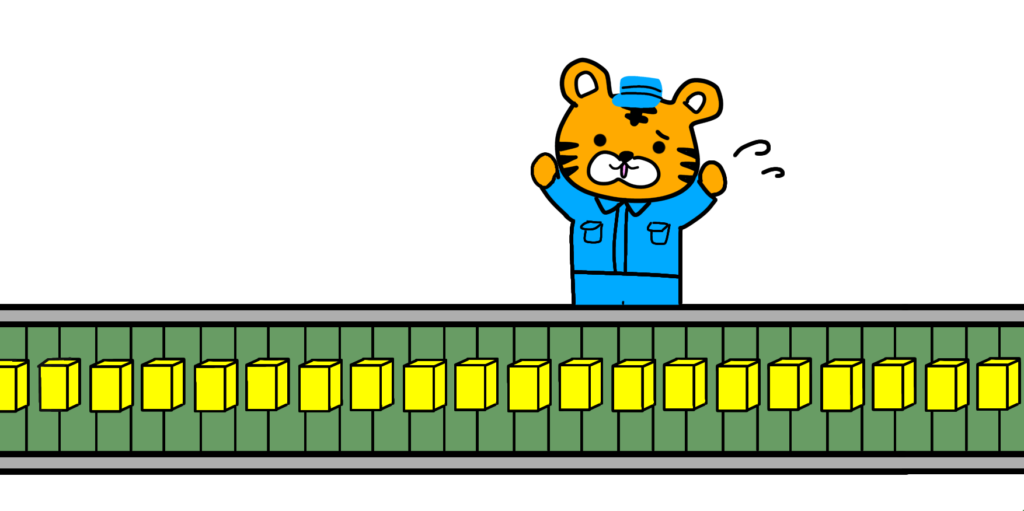
まとめ
- 初期流動管理
⇒設計やプロセスの新規適用または変更の際に、量産の初期段階で通常よりも検出感度の高い品質管理を行うことで、不具合を未然防止する管理手法 - 管理の目的
⇒設計の妥当性確認、工程能力の見積り、品質への影響要因の抽出 - 運用方法の事例
⇒管理する項目を増やす
記録内容を増やす
頻度を上げる - 管理の対象期間
⇒ロット数で決める
生産台数で決める
歩留りの状況で決める - 実践のポイント
⇒①:定量的にデータを残す
②:あえて意地悪な流し方をする
③:管理の目的を忘れずに
初期流動管理は、自社の工程の安定化に繋がるだけでなく、部品メーカなど仕入先の変更点管理にも活用できる重要な考え方です。
今回紹介した管理方法の例を参考に、ぜひ試してみてください。
コメント