品質管理の基本的な考え方の一つに「後工程はお客様」という表現があります。
これを聞いて、「後工程は自社でやってるから関係ないよ」と思った方、無関係な内容ではありません。
お客様という表現は、ひとつの言い回しで、後工程が顧客か社内かによらず、品質管理における流出防止の重要な考え方として覚えておくと良いです。
この記事では、後工程はお客様の考え方について、なぜ重要なのか、私自身の経験談を交えて解説しますので、皆さんの参考になればうれしいです。
どういう考え方なのか?
顧客志向という言葉をご存じでしょうか。
企業活動のすべてを顧客中心に考える態度。マーケティング中心の考え方。市場志向。消費者志向。
引用元:広辞苑
顧客(お客様)のニーズに応えた製品やサービスを提供することを最優先とする行動指針を表した言葉です。
顧客のニーズには、機能・性能、コスト、品質などがあり、この中でも特に品質面で顧客に満足いただける製品を作ることが品質管理の使命です。
製品の最終工程を担当する部門や、不具合対応の窓口の部門では、お客様と直接関わる機会も多く、どのようなニーズやクレームがあるのか、肌で感じやすいことと思います。
しかし、すべての部門がこれらを感じ取れるわけではなく、特に上流工程では日常で触れる機会のないことがほとんどと思います。
よく言う教科書的な表現として、品質は全部門で作り上げるという通り、お客様と関わる部門だけが意識する問題ではなく、全員参加で取り組むことが重要です。
そこで、自分の担当する次の工程を顧客に例え、納得いただける品質の製品を送り出すことを行動指針とした考え方として、「後工程はお客様」という表現が考案されました。
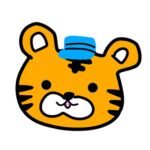
意識の持ち方が大事なんだね
なぜ重要なのか?
2つのポイント
なぜ「後工程はお客様」という考え方が重要なのか、2つの側面での有効性を説明します。
①:工程が進むほど付加価値が増える
製造工程を進めるごとに、材料コストや加工コストがかかります。
当然、出荷の直前が最も手間ひまのかかった状態であり、完成間近で不良品となって廃却してしまうのが最も痛手の大きい状態です。
つまり、工程が進むほど製品の付加価値の高い状態となり、同じ1個を廃却する場合でも、最初と最後の工程ではロスコストが全く異なります。
そのため、不具合は早期に発見できるほどダメージを抑えられ、できる限り前工程で摘み取ることが望ましい状態と言えます。
②:不具合の流出防止につながる
不具合の流出はあってはいけないことですが、恒久的に完璧にゼロに抑え込めるわけではなく、避けては通れません。
どんなに作り込んだつもりの工程でも、わずかな穴から不具合が漏れてしまう可能性があります。
例えば、材料のばらつきや、装置の異常、検査の見逃しなど様々で、各工程に要因が潜んでいます。
後工程をお客様と考え、それぞれの工程で不具合の発生防止、流出防止に真摯に取り組むことで、安定した工程を確立することにつながります。
スイスチーズモデル
スイスチーズモデルとは、イギリスの心理学者ジェームズ・リーズンが提唱した事故の発生メカニズムを表現したモデルのことです。
スイスチーズは、内部に大きな穴がたくさん開いた見た目が特徴的なチーズです。
発酵の途中段階で発生する二酸化炭素が核となり、そこに乳酸菌が増殖してガス溜まりを作り、そのまま内部に留まることで空洞を形成します。
この多数の穴を「リスクが流出する欠陥」と見立てて、何層ものチーズの穴をすり抜けた結果、事故として顕在化することを表したものがスイスチーズモデルです。
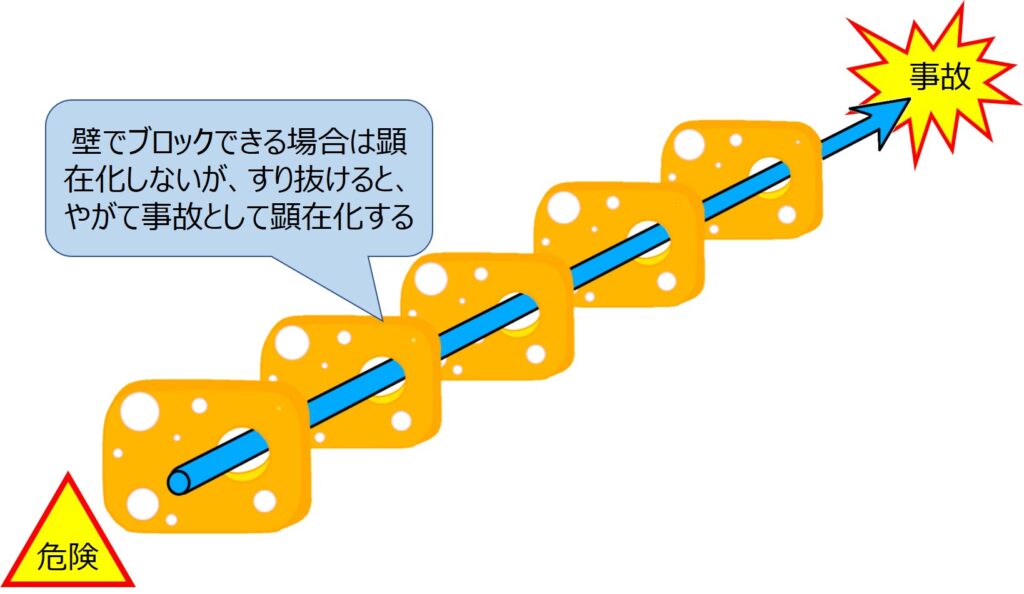
これは不具合の流出にも当てはまります。
例えば、とある工程で不具合が作り込まれたとしても、通常はその次の工程で組立ができなかったり、検査工程で検出されたりと、出荷までの過程で発見されるケースも多くあります。
これは、ひとつの工程で穴があっても、その後の工程が壁となって、すぐさま流出することは無いことを表しています。
ただし、これに甘んじていると、何層もの穴が重なる場合に、本当に不具合が流出してしまいます。
お客様への不具合の流出は、稀な事象だからとか、悪い条件が重なって・・という理由で許容されるものではありません。
流出を防ぐには、中間検査を増やす(層の数を増やす)とか、各工程でチェックを厳しくする(穴を小さくする)対策が求められます。
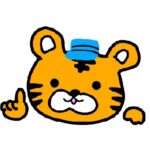
次の壁に頼らず、自分のフィルターを細かくしよう
自工程完結の考え方
工程の管理強化の考え方として、自工程完結という言葉があります。
自らの工程で作ったものは、自分で品質を保証して完結させるという思想です。
例えば、2つの部品を接着剤で貼り合わせる作業を想定してみます。
片方の部品に接着剤を塗って、もう片方をくっつけることで、作業自体は終了です。
しかし、接着剤は瞬間的には硬化せず、流動性がなくなるまで、あるいは機械的な強度が出るまでに、一定の時間を要します。
では、貼り付け直後に次の工程にモノを送り出しするとどうなるでしょう。
強度が不足して後に剥がれたり、固まるまでに傾いて形状がいびつになったり、後工程で見つかれば良い方ですが、客先での不具合になりかねません。
自工程完結は、自らの工程で品質を担保する考え方です。
この事例では、自工程で硬化時間を設ける、接着強度を抜取で確認する、といった管理を行うことで、後工程に頼らない確立された工程を築くことができます。
実践のポイント
ポイントを3つ紹介します。
①:後工程の気持ちを考える
逆の立場で考えてみると、要求されるものが何かイメージしやすいと思います。
例えば、自分の前の工程から不良品が流れてきたとしましょう。
見た目で明らかな不良のように、見逃しのケースもありますが、自分の工程で組み立てられないことで初めて分かる不良もあります。
当然、「組み立てられないものを送ってくるな」という気持ちになりますね。
これは、寸法をきちんと測定して良品を選別してほしいという要求であり、すなわち、前工程側が果たすべき責任でもあります。
「後工程で何とかしてくれるだろう」ではなく、その立場の目線で考えることで、独りよがりな品質保証になることを避けられます。
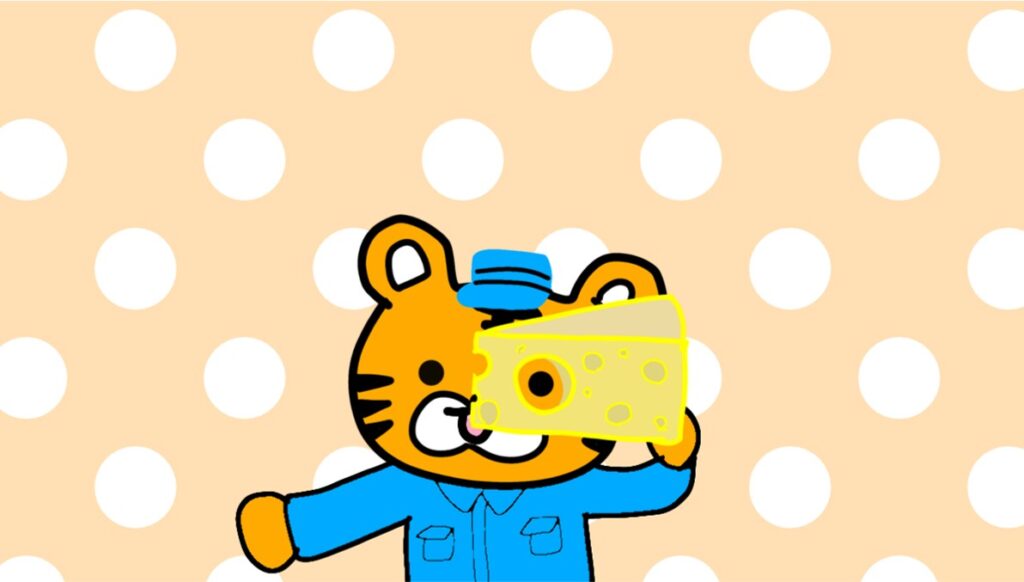
②:判断基準を明確に
判断基準の線引きが不明確だと、責任の所在も曖昧になってしまいます。
そうなれば、それぞれ自分の都合の良い方に捉えて、責任を相手に押し付ける思考に走りがちです。
「この程度の不良は後工程で見つけるべきだ」と一方的にならず、双方で判断基準をすり合わせて、検出精度や付加価値など総合的に判断し、組織としてベストな解を見出すことが望ましいです。
③:連携を密に
最後に当たり前の話ですが、双方のコミュニケーションを密にとることで、認識の食い違いや、情報の伝達不足がないように心がけましょう。
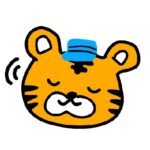
お互い譲り合ってしまうと隙間になるから気を付けよう
こてつ経験談
検査の見逃し?
とある仕入先とのやり取りの話です。
新規に部品を採用して実績がまだ浅かったころ、私の担当する工程内で不良品の流入が多数見つかり、トラブルとなったことがありました。
少なくとも、仕入先での出荷検査と、自社での受入検査を通っており、2段階の検査をすり抜けて工程内に流入したことになります。
まずは、自社の受入検査にクレームを申し入れて、検査見逃しの是正を依頼したのですが、ここで検査規格に対する認識の違いが見つかりました。
この不良品は、部品の角が欠けた状態だったのですが、納入仕様書では、部品の側面や角部が検査対象とは明記されていなかったのです。
つまり、仕様書の取り交わしの不備ということで、いったんは取り下げることになりました。
しかし、品質上どうしても許容できず、その後に仕入先と再調整して、納入仕様書を見直して、検査箇所を追加することにしました。
あらためて、仕入先と自社内の検査強化を依頼し、不良品の流入は無事に解決したというわけです。
続いて発生対策
不良品のすり抜けに関しては、事なきを得たのですが、今度は発生防止で課題が生じます。
検査項目を追加したことで、仕入先の歩留りが大幅に悪化し、良品を十分に確保できなくなってしまったのです。
元々は仕様不備なので、仕入先を突き放すわけにもいかず、ともに仕入先の工程の管理項目を見直すことにしました。
あらためて工程フローを見ると、製造での確認や中間検査はなく、出荷前検査の一箇所しか、歯止めをかける関門がないことが分かりました。
事情を聴くと、途中段階で製品に触ると脆くて破損するため、最終段階でないと確認できないという理由によるものでした。
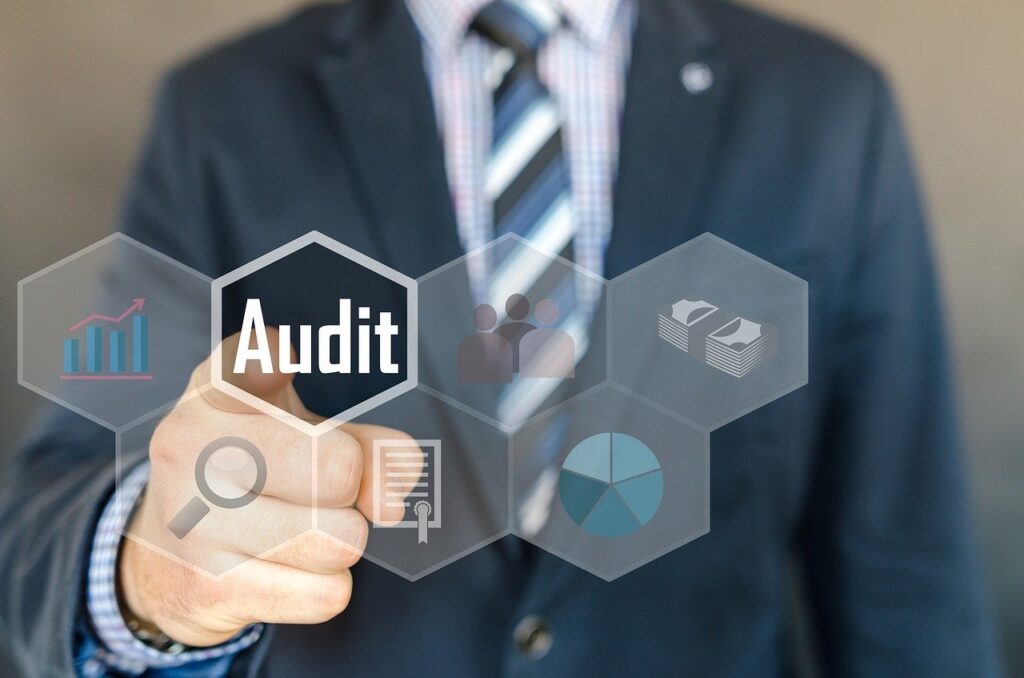
あるべき姿を確認する
製品そのものでなくても、各工程や装置の健全性は確認できます。
例えば、装置の場合、温度や圧力といった要素の確認が該当します。
つまり、始業前点検を意味しており、パラメータが管理範囲内であることを確認する行為も、不良の発生防止の重要な取り組みです。
工程の健全性に関しては、材料の場合は、粘度や粒度、混合比といった要素の確認が挙げられます。
あるいは、途中段階の製品の場合は、強度や寸法など、破壊試験や非破壊試験を織り交ぜて、色々と確認できる項目があります。
製品で直接的に確認することも重要ですが、装置や工程の健全性としては、むしろ要素として確認する方が、不調の兆候を捉えやすい場合もあります。
工程、装置のあるべき姿を日々確認して、何重もの流出防止の壁を構築していきましょう。
まとめ
- 後工程はお客様
⇒次の工程を顧客に例え、納得いただける品質の製品を送り出すことを行動指針とした考え方 - なぜ重要なのか
⇒工程が進むほど付加価値が増えるため、不具合の流出防止につながるため - スイスチーズモデル
⇒チーズの多数の穴を「リスクが流出する欠陥」と見立て、何層もの穴をすり抜けた結果、事故として顕在化することを表したモデル - 自工程完結
⇒自らの工程で作ったものは、自分で品質を保証して完結させる考え方 - 実践のポイント
⇒①:後工程の気持ちを考える
②:判断基準を明確に
③:連携を密に
いくら気をつけていても、思わぬ抜け穴から不具合は出てしまうものです。
対策に完璧というものはないので、チーズの層の数を増やし、穴を小さくすることを日々意識して、工程の地盤を固めておきたいですね。
コメント