トラブル対応シリーズの最後は、未然防止編です。
ここまで、トラブルが発生した際の初動対応にあたる応急処置、是正や予防処置により根本原因を取り除く再発防止を紹介しました。
最後に紹介する未然防止は、予防処置と似た意味合いで位置づけられ、事故を未然に防ぐ処置を表します。
人為的ミスを防ぐ考え方として、ポカヨケやフェールセーフという用語を聞いたことはありませんか?
この記事では、これらの用語の意味と違いを具体例を交えて紹介します。
また、ヒューマンエラーの発生概念を表すmSHELL分析モデルや、日常管理の6つのステップを表すA-KOMIK手法は、仕組みづくりの参考になります。
できるだけ基本から分かりやすく解説しますので、ぜひ最後まで読んで参考にしていただければと思います。
ポカヨケとフェールセーフの違い
ポカヨケとは
「ポカ」とは、囲碁や将棋の世界で、不注意からとんでもない悪い手を打つことを表しており、ポカを避けるという意味合いから「ポカヨケ」という言葉が作られました。
バカヨケと言ったり、英語ではフールプルーフ(fool proof:愚か者向け試験)と呼ばれたりします。
生産現場には、多くの危険が潜んでいます。
設備の誤動作や作業ミス、安全上の危険や品質面での不具合など、色々な面で事故の危険があり、事故が起こってから行動に移していては手遅れです。
こういったリスクへの対処として、そもそも危険が生じないように製品設計や生産設計の段階で仕掛けを組み込むことをポカヨケと言います。
仕掛けといっても、作業者のスキルに依存するようなものではダメで、誰がいつ何度やっても同じように安全機能が作動しなければなりません。
つまり、愚か者がやっても大丈夫、という意味合いがフールプルーフの語源となっています。
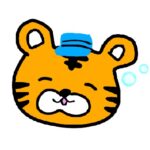
見習いトラでも出来るようにしようね
ポカヨケの具体例
ポカヨケは、日常生活にもたくさんの事例があります。
例えば、洗濯機のフタを閉め忘れるとスタートできない、鍋を置かないとガスコンロが点火しない、といったものが挙げられます。
そもそも、正しい状態にセットしなければ稼働できないという考え方で、これなら安全に使うことができますね。
生産現場の事例では、設計段階で作りこむことが多いですが、製品設計だけでなく、装置や治具にも取り入れられる考え方です。
そのため、生産技術、製造、検査部門など関係者全体での検討が求められます。
特に、製品の品質ももちろんですが、安全上の問題にも関わるので、労災防止の観点から検討を怠らないようにしましょう。
以下に、ポカヨケの一例を紹介します。
フェールセーフとは
フェールセーフ(fail safe)とは、万が一、誤操作や誤動作が生じた場合でも安全に制御する仕組みのことです。
装置はいつか壊れる、人間は必ずミスをするという考え方に基づき、そういった状況でも安全に制御することで、事故の誘発を防ぐ手法です。
ポカヨケは事故のキッカケとなる失敗を発生させない考え方ですが、フェールセーフは失敗することを前提にして事故につながる経路を絶つ考え方です。
たった一つの失敗で大事故や大きなトラブルに発展することは少なく、その後の処置が適切でないことで被害を拡大させてしまいます。
すべての細かい失敗を取り除くのは大変な作業なので、失敗しても流出させない、壁を何重に作ることを念頭に置いた未然防止の考え方です。
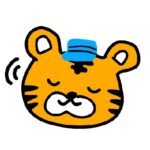
安全機能があれば安心だね
フェールセーフの具体例
こちらも、日常生活で色々な具体例があります。
例えば、自動車のドアロックを忘れても一定速度になれば自動ロックする、ガスコンロで吹きこぼれて火が消えたら自動でガスを止める、といった用途です。
事故のキッカケとなる「失敗」が生じても、自動的に安全な方向に制御するように構築されています。
生産現場での事例としては、以下が挙げられます。
人為的なミスや突発的な異常による事故の種を装置側のセンサやシーケンス(動作順序)で補うことで、何重もの壁を作っています。
このように、ポカヨケとフェールセーフは性質の異なる考え方ですが、いずれが欠けても事故の発生する確率は大きく増加してしまいます。
関係部門で総力を挙げて、安全と品質を作りこんでいきたいですね。
mSHELL(エムシェル)分析モデル
ヒューマンエラーの背後要因を分析するための考え方として、mSHELL分析モデルを紹介します。
最初に概念図から説明します。
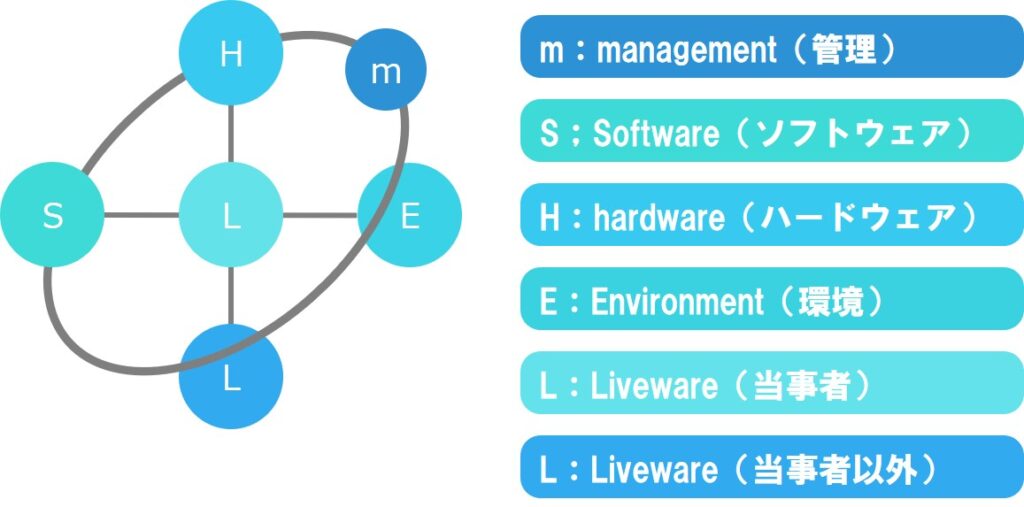
mSHELLはそれぞれ要因を分類する名称の頭文字です。
元々、オランダの航空会社から提唱された安全の考え方としてSHELLモデルがあり、これに東京電力の河野氏が提唱した「m:management(管理)」の要素を加えたものが、mSHELLモデルです。
現場を取り巻く状況を模式図に示したもので、当事者本人(中心のLiveware)を軸に、周りの人、ソフトウェア、ハードウェア、環境が相互的に作用する関係性を表しています。
mSHELLモデルでは、これにマネジメントを加えたことで、より現場の実態に近い状態を表すモデルとして活用されています。
具体例を挙げて見てみましょう。
今回は、「製品A向けの部品を誤って製品Bに取り付けてしまった」という事象を題材にします。
以下のように、それぞれの要素に分類して背後要因を挙げることができます。
そして、要因ごとに対応付けて、再発防止に向けた改善策を洗い出すことができます。
一見、部品の付け間違いという単純なミスですが、このように多角的な視点から挙げて見ると、色々と課題が見えてくるものです。
決め打ちの対策に走らず、網羅的に抜け漏れがないか、きちんと整理して対応策を検討するようにしましょう。
なお、今回はトラブル事例として具体例を挙げましたが、「想定されるトラブル事例」と置き換えて検討することで、未知のトラブルの未然防止にも役立ちます。
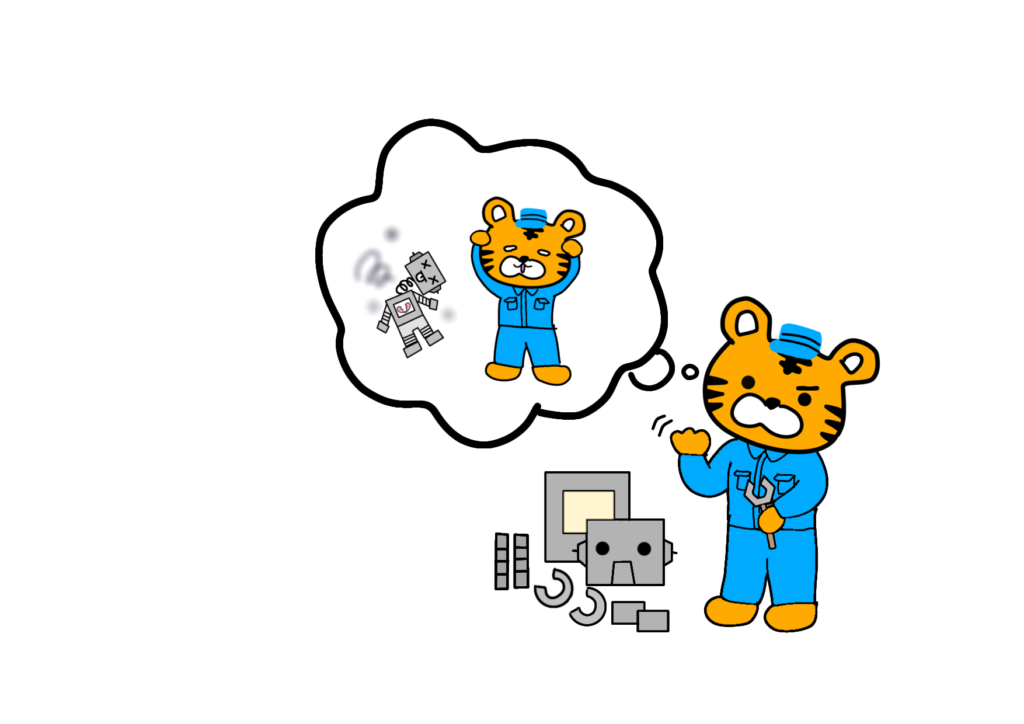
A-KOMIK(エイコミック)
人為的ミスの未然防止を目的とした日常管理のステップで、A-KOMIKという考え方があります。
それぞれ頭文字を取ったもので、以下の6つのステップに分かれます。
A:曖昧さを見つける
K:決め事を決める
O:決め事を教える
M:決め事を守らせる
I:異常を見つけ処置する
K:決め事を改善する
いざ、「ヒューマンエラーの撲滅に向けた活動を!」といっても、いきなりルールを決めて運用に落とし込むのは難しいと思います。
そこで、ステップを刻んで、それぞれの段階で課題と対応策を明確に示すことで、網羅的で無理のない運用ルール(決め事)の規定に結びついていきます。
A-KOMIKのステップを進めるにあたって、想定される障壁と対策の視点の一例を紹介します。
ルールの中身の問題、マネジメント層の問題、組織体制の問題など、色々な要因のあることが分かると思います。
これらの課題を多角的に捉えて、漏れなく検討することが重要であり、フレームワークの一つとして、活用してみてはいかがでしょうか。
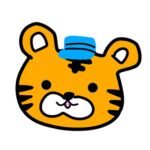
フレームを決めておくと漏れがなくなるね
こてつ経験談
過去資料を参考にして
とあるリピート機種の生産技術を担当していた時の話です。
リピートといっても、数年に一度のサイクルで生産している程度で、しばらく休止期間を経た後の再立上げで起きた出来事でした。
私は生産前の準備として、自動機の健全性の確認を行っていました。
決められた条件で製造した場合に、意図した通りのものができるかどうか、再現確認を行っていたのです。
作業要領書から製造条件と良品規格を参照し、試作したサンプルの寸法や質量測定を行って途中段階の出来栄えに問題がないことを確認しました。
ベテラン作業者に助けられ
事前検証は順調に終わり、いざ生産を始めると早速トラブルが勃発します。
その工程は、自動機で複数種の接着剤を重ね塗りする作業だったのですが、最初に塗った接着剤の途切れた隙間から次の接着剤が漏れ出してきたのです。
思っていたよりも流動性が高く、隙間を許容できない状態であったということです。
自動機での条件調整に行き詰った結果、前回まで担当していたベテラン作業者にヒアリングすることにしました。
すると、実は自動機で塗った後に隙間を埋めるための手直しを施していたというのです。
その作業は要領書に記載なく、作業者の感覚によって独自に判断して工夫してくれていたのでした。
知らないうちに、ベテラン作業者の方にずっと助けられていたわけです。
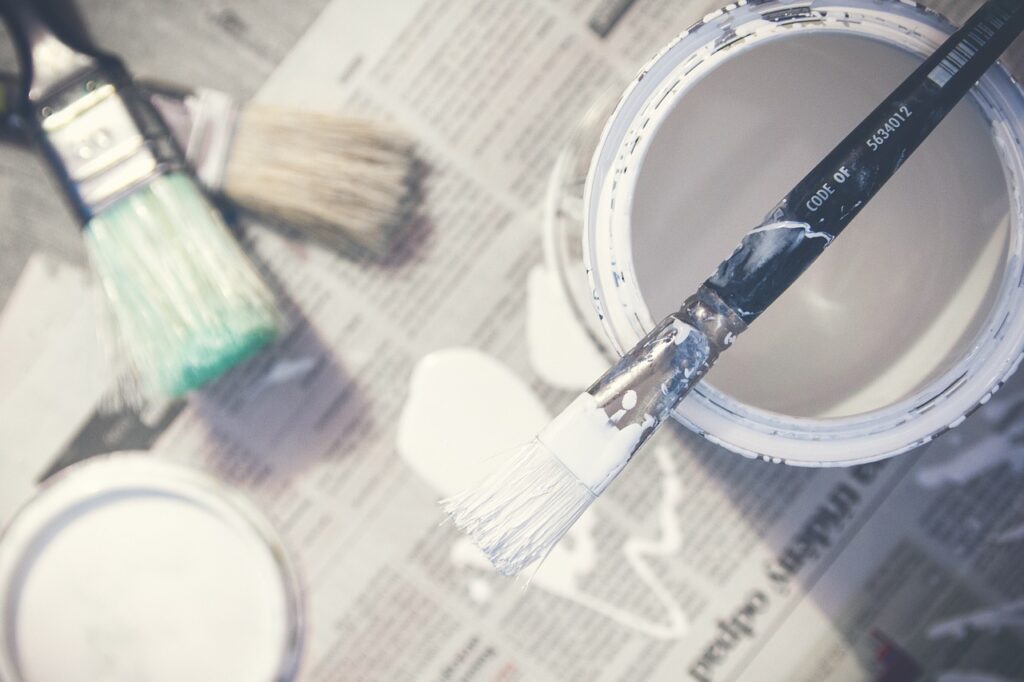
ノウハウは情報資産
今回の問題点は、現場に頼りっぱなしになって、要領書への反映や要因の分析を怠ったことでした。
さらに、そのまま後任に引き継ぐことになり、製造も生産技術もノウハウを伝承することができなかったのです。
未然防止の工夫は、設計や生産技術だけでなく、製造側でも色々とノウハウを蓄積して改善を検討してくれています。
特に、実際の作業者の持つ勘やコツは、突き詰めると理にかなったものも多く、貴重な情報資産であることが多いのです。
この資産を無形のままムダにせず、きちんと要領書に残して仕組み化するところまで落とし込んで、不具合の未然防止を推進していきたいですね。
まとめ
- ポカヨケ
⇒危険が生じないように製品設計や生産設計の段階で仕掛けを組み込むこと
⇒事故のキッカケとなる「失敗」そのものを発生させない考え方 - フェールセーフ
⇒誤操作や誤動作が生じた場合でも安全に制御する仕組みのこと
⇒「失敗」を前提にして事故につながる経路を絶つ考え方 - mSHELL分析モデル
⇒ヒューマンエラーの背後要因を分析するための考え方
⇒現場を取り巻く状況を模式図に示したモデル - A-KOMIK
⇒ヒューマンエラー防止に向けた日常管理の6つのステップ
ヒューマンエラーとの闘いは終わりがありません。
いつか誰かが上手くやってくれるとか、自然と風土が根付いてなくなる、といった根拠のない期待は持たず、現状と向き合って分析を推進していきましょう。
今回紹介した考え方やフレームワークを活用することで、関係者とも情報共有がしやすくなると思います。
ぜひ、身近な題材で試してみてください。
コメント