トラブルの初動対応として、応急処置を済ませたら、次は根本的な問題解決に向かって、再発防止に取り組みましょう。
応急処置編の記事でも紹介した通り、一時的に消火しても元となる火種を取り除かなければ、何かのきっかけに再燃してしまいます。
しかも、いったん落ち着いたことに油断して、一日の生産数量やロットの規模を増やしていると、再発した時のダメージがさらに大きくなって返ってきます。
次の段階として恒久対策を完了するまでは気を抜いてはならず、トラブル対応の一連の流れとして完遂する必要があります。
この記事では、再発防止の処置の分類、検討する際の考え方のポイントについて、具体例を交えて解説しますので、皆さんの参考になればうれしいです。
発生防止と流出防止
再発を防止するには、製造と検査の2つの視点から対策を講じる必要があります。
①:製造段階での発生防止
不具合の発生する原因を元から摘み取ることを意味します。
虫歯の原因を取り除かない限り、また痛んでしまうのと同じように、元の原因を見つけなければ、根本解決には至りません。
原因調査にあたっては、なぜなぜ分析やFTA(Fault Tree Analysis:故障の木解析)の手法の他、QC7つ道具、新QC7つ道具をフル活用しましょう。
データを収集して現状を把握し、得られた結果から仮説を立案、さらには再現実験による仮説の立証といった手順で検討を進めるのが望ましいです。
②:検査による流出防止
もし不具合が再発しても、検査でしっかりと歯止めをかける考え方です。
次の工程に進むほど製品の付加価値が高くなりロスが大きくなります。
さらには、出荷検査での見逃しは、お客様への流出になるので、絶対に避けなければなりません。
そもそも、流出させてしまうことにも原因があるので、発生防止と同じように要因を調べて、ふるいの目を細かくする必要があります。
例えば
・検査員のスキル
・検査装置の精度
・検査員の判定基準
・計測環境
といったように、5M+1Eの観点で漏れがないか確認することが大切です。
4Mとは、Man(人)、Machine(機械)、Material(材料)、Method(方法)のことで、さらにMeasurement(測定)、Environment(環境)を加えたものが5M+1Eです。
発生防止と流出防止は、車の両輪のようなものなので、どちらも抜かりなく対策を講じるようにしましょう。
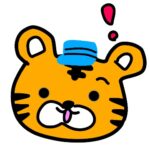
いろんな視点で対策に取り組もう
現在と未来に対する処置
是正処置
是正処置とは、問題点をあらためて正しい状態にすることを意味します。
トラブルが起きた結果そのものに対する是正を行うもので、つまり「現在」の問題点に対する処置を表します。
是正処置の内容としては、5M+1Eの観点から網羅的に行う必要があります。
具体的なイメージとしては、例えば、設計変更(材料)、製造プロセス変更(機械、方法)、ヒューマンエラー対策(人、方法)などが挙げられます。
応急処置編の記事でも紹介した「プレス加工部品で亀裂(ひび割れ)が発生する」というトラブル事例を具体例に挙げてみます。
この場合、仕入れ材の平面度を指定する(材料)、成形圧力を下げる(方法)、圧力を定期確認する(機械)、検査基準を見直す(測定)といった処置が考えられます。
予防処置
もう一つの処置の考え方として、予防処置があります。
予防処置とは、同種のトラブルを予防するために行うもので、「未来」に起こる可能性のある問題に対する処置を意味します。
つまり、「転ばぬ先の杖」にあたるリスク管理のことで、是正処置のさらに次のステップとして、重要な意味合いを持ちます。
予防処置には、次の2つの対応があります。
①:水平展開
類似の製品や工程で同じ問題が起きないよう、水平展開を図ります。
形式的に事実を伝えるだけでは意味がなく、きちんと現状を分析し、情報を整理して展開しましょう。
今回の具体例の場合、同じプレス加工の工法を用いる製品や、同じ材料を取り扱う製品に展開することが考えられます。
情報の共有にあたっては、是正処置の内容だけでなく、その問題が起きた背後要因も分析して展開することが望ましいです。
例えば、成形圧力を定期確認しなかったのはなぜか?という問いかけに対し、仕組みがない、あるいはルールを守らないといったように、何らかの理由があるはずです。
その理由を突き止めて、根本から解決することで、同種のトラブル防止の効果を最大限に発揮することができます。
原因の深掘りにあたっては、なぜなぜ分析や新QC7つ道具の連関図法を用いると、効率的に進められます。
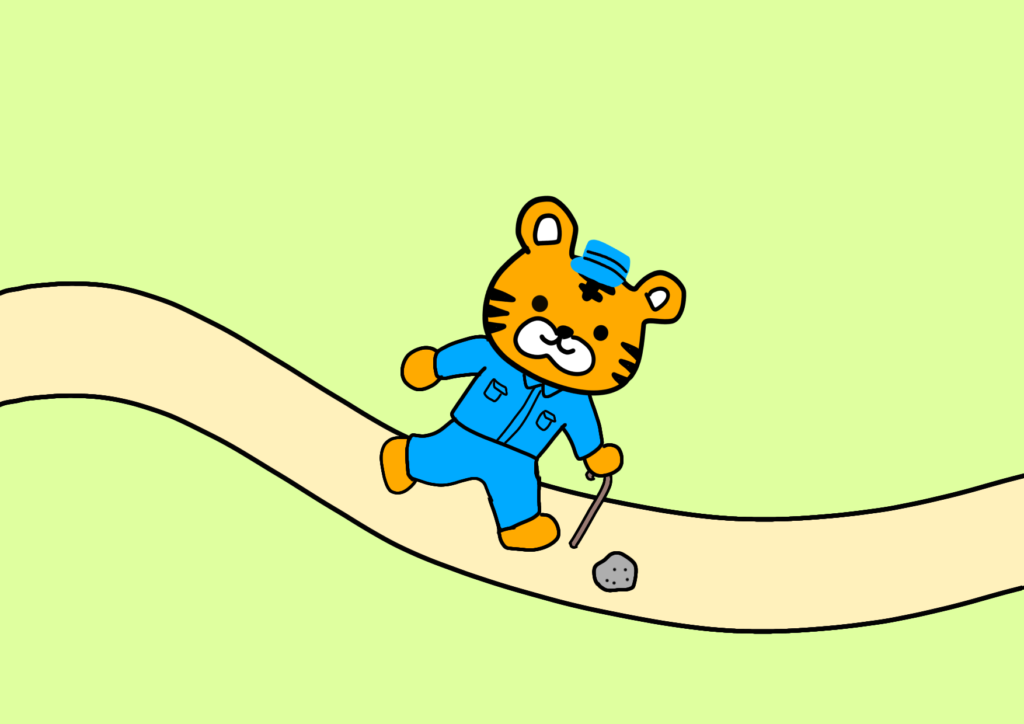
②:仕組み化・標準化
最後に仕組み化・標準化まで実施できれば、一連の再発防止の処置は完了です。
仕組みに落とし込むには、水平展開で実施した背後要因の調査が不可欠です。
なぜ発生したのか?どのような取り決めがあれば防げたのか?という観点に着目し、適切な運用ルールに見直しましょう。
今回の事例では、例えば以下のような改善策が考えられます。
事象:成形圧力を定期確認しなかった
なぜ1:定期確認するルールがないから
対処:保全要領書にルールを規定する
事象:目視検査で見逃しが生じた
なぜ1:疑義を見つけても報告しないから
なぜ2:作業者の品質意識が低いから
なぜ3:教育の機会が少ないから
対処:定期的に品質教育を図る
このように、一言で再発防止といっても、役割の視点から発生防止と流出防止、時間軸の視点から是正処置と予防処置に分類されます。
いずれの検討が欠けても不十分な対策となってしまいますので、最後まで完遂することを忘れないようにしましょう。
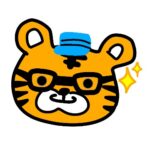
ここまで出来ればバッチリ
こてつ経験談
藁(わら)にもすがる
「トラブルが発生したら再発防止策を!」と簡単に言うものの、実際に具体案を考えるとなると、結構行き詰まるものです。
私自身も過去にいくつもの不具合対応を担当しましたが、すんなりと解決に向かう案件はあまり多くありませんでした。
関係者で集まって頭を悩ませていると、ふとした時に「とりあえず、こういう対処をしたら?」という意見がポロっと出ることがあります。
行き詰った末に出た意見なので、関係者一同で「そうだ、そうしよう」と一気に意向が傾いていき、そのまま方針が決まる流れをよく目にしました。
まさに、藁にもすがる思いで、その意見を全面的に信頼することになるのです。
こういう状況で、貴重な意見を出してくれたことは大変重要で、その人の真剣さがよく伝わりますが、周りの意見まで一気に傾くことは要注意です。
その途端、他の選択肢が頭の中から排除され、意識が一つの処置に集中してしまうからです。
結果として、ひとつの発生防止策に特化した処置となり、流出防止や、その先の予防処置が全く抜けたものになってしまいます。
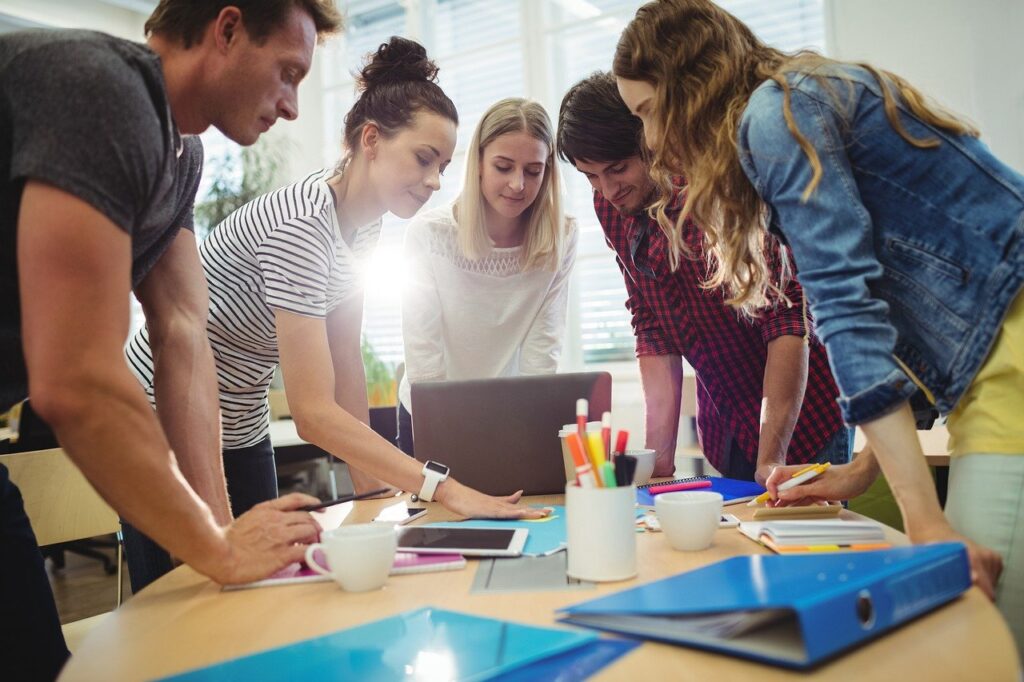
色々な立場での客観視が必要
関係者で対応策を検討する際には、色々な立場から意見を集約して、網羅性に注意を払う必要があります。
例えば、生産技術の立場からすると、条件や設備の改善により、発生防止を推進する意見が多く挙げられるかもしれません。
あるいは、品質管理の立場では検査の強化による流出防止、設計目線では将来製品に予防策を盛り込むなど、それぞれの立場を活かした意見が出ると思います。
その時に、誰かの意見に全面的に依存するのではなく、きちんと自分の立場として責任を持ったアイデアを出すようにしましょう。
ちなみに、他人の意見に流されないというのは、それを否定することを推奨しているのではありません。
「こういう視点が漏れているから、別の対策を並行して進めよう」といったように、他を補うための建設的な意見として議論できることが望ましいです。
全部門を巻き込んだ活動は、対応策として厚みが出るだけでなく、組織力の向上にも役立ちます。
まとめ
- 役割に応じた再発防止の分類
⇒発生防止:製造段階で元の原因を摘み取ること
流出防止:検査で疑義品の歯止めをかけること - 是正処置
⇒問題点をあらためて正しい状態にすること、「現在」の問題点に対する処置 - 予防処置
⇒同種のトラブルを予防すること、「未来」の可能性に対する処置
品質は全員参加で作りこむと言うように、責任部門がすべてを背負うのではなく、皆で改善しようと意識を持つことが重要です。
会議で責任の所在を議論するのではなく、次に進むための建設的な議論にしっかりと時間をかけて、組織力の向上に努めていきましょう。
コメント