品質管理の基本的な考え方として、今回は「源流管理」について解説します。
源流とは工程の上流を表し、つまり上流をきちんと管理することを意味します。
なぜ源流管理の考え方が大切なのか、何をどう管理すればよいのか、このような疑問を解決します。
この記事では、まず源流管理の考え方、管理の重要性とポイントを解説します。
続けて、別の記事では、管理項目や着眼点の具体例を詳しく解説します。
できるだけ具体例を挙げてイメージが付きやすいように説明しますので、皆さんの参考になればうれしいです。
どういう考え方なのか
源流管理とは、上流工程の品質をきちんと管理することです。
工程全体を川の流れに見立てると、前工程が上流、後工程が下流になります。
複数部品を組み立てていくのは、途中で複数の河川が合流するのと近いイメージで、最終的に河口にたどり着いて、お客様へと出荷されていきます。
下流ほど川幅も広くなり、万が一、洪水になって氾濫した際には甚大な被害に繋がります。
これは、製品の製造でも同じで、後工程になるほど不具合の影響が大きくなることから、源流をきっちりと管理することが重要という考え方です。
管理する対象は、上流の工程だけでなく、部品や材料といった源泉にあたるものも含まれます。
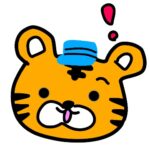
元栓をしっかり閉めるということだね
なぜ重要なのか
製造における3つの柱として、QCDの要素があります。
Quality(品質)、Cost(コスト)、Delivery(納期)のことで、この3つの側面で源流管理の考え方が重要と言えます。
①:応急処置では不具合が再発する(Quality)
トラブルや不具合が発生した場合、適切な対処が必要となります。
初動対応として重要なのは応急処置ですが、応急処置だけ対応して油断してはいけません。
被害の拡大を防いで緊急的な処置を行う意味では大切ですが、根本解決になっていないからです。
根本原因を対処しないと、不具合はいずれ再発します。
その時の被害は最初の不具合よりも大きくなる可能性も十分にあります。
そのため、きちんと源流に遡って、不具合の元を抑えることが重要なのです。
トラブル対応の進め方については、応急処置、再発防止、未然防止の記事に詳しく記載しています。
②:下流になるほどロスコストが増える(Cost)
工程が進むほど、材料や部品が多く投入され、各工程での工数が加算されていきます。
そのため、不具合が見つかるのが後工程になるほど、投入したリソース(モノや人の資源)がムダになってしまいます。
特に、完成間近の出荷検査でNGになった場合は、せっかく手間ひまかけた製品が丸ごとダメになってしまうので、避けなければなりません。
不具合をできるだけ源流に近い段階で見つけて、後工程に流出させない考え方として、「後工程はお客様」という言い回しがあります。
自分の担当する次の工程を顧客に例え、納得いただける品質の製品を送り出す意識を持つことで、それぞれの工程での責任感が高まります。
発生させた不具合は自分たちで見つけて改善する考え方を根付かせることで、おのずと不具合の発生そのものも改善されることと思います。
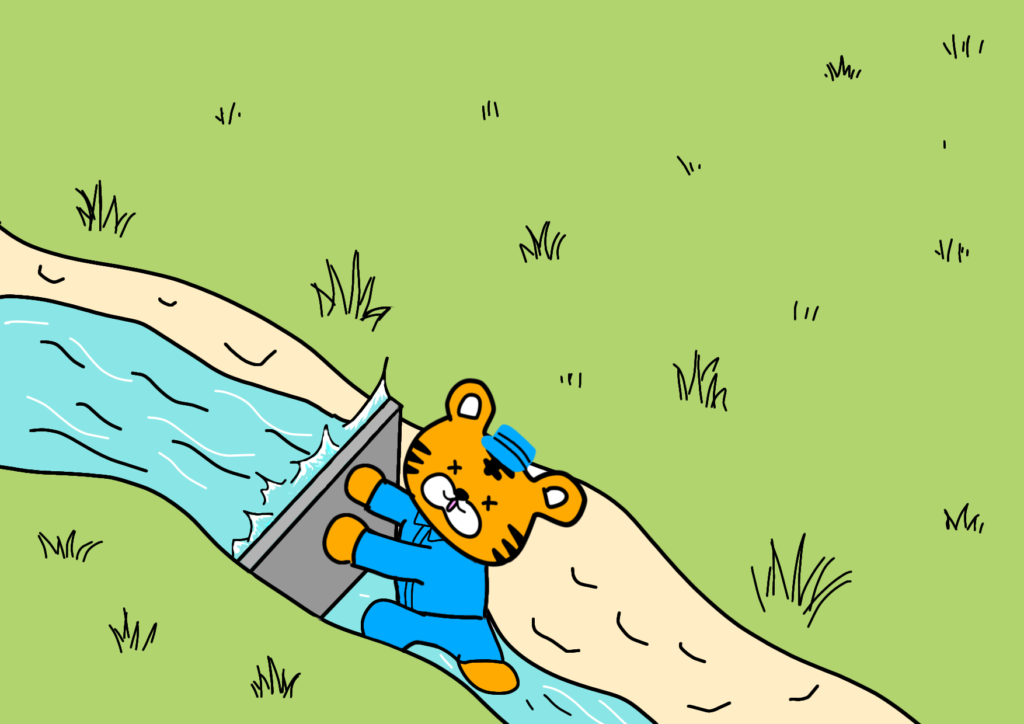
③:下流になるほど改修期間がかかる(Delivery)
例えば、自動車のような何万もの部品からなる製品を想像してみてください。
出荷前の最終試験で何らかの不具合が発覚し、とある部品の不良が原因と判明したとします。
ひとつの部品のために、その自動車一台を丸ごと廃却するロスを考えると、部品交換の選択肢が現実的になります。
しかし、多くの部品がすでに組み込まれた状態での交換は大変厄介で、工程を遡って部品を分解せねばなりません。
そして、部品交換が終わったら、また組み直すことになります。
不良部品以外の材料をムダにしないためには仕方ない選択ですが、改修期間も改修コストも大きな影響が出ます。
納期遅延にもなりかねないので、できるだけ早い段階で見つけ出して改修を施す対処が求められます。
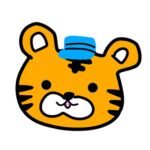
品質面の影響だけじゃなんだね
管理のポイント
ポイントを3つ紹介します。
①:要素に分類して多角的に攻める
とある偏った視点に絞ってしまうと、管理に抜け漏れが出てしまいます。
ひとつの穴を防ぐだけでは水漏れは解消されないのと同じように、関係部門すべてで参画し、網羅的な対処をすることが重要です。
要素の分類には、5M+1Eの考え方を用いると効率的です。
4Mの要素として、Man(人)、Machine(機械)、Material(材料)、Method(方法)に、Measurement(測定)とEnvironment(環境)を加えたものです。
管理項目や着眼点の具体例は、別の記事で詳しく紹介していますので、合わせてご覧ください。
②:全部門参加で取り組む
5M+1Eに分類して漏れなく進めるには、全部門参加で取り組む必要があります。
源流からの不具合を流出するには、それぞれの工程で意識を高く持つ必要があり、特定部門の活動だけで成り立つものではありません。
部門を横断する取り組みは、どうしても利害関係が生じるので、円滑に進めることが難しいかもしれません。
しかし、それぞれの領分の最適解だけに固執すると、全体として穴だらけになってしまうので、目標を共有してそれぞれが全体最適の意識を持つことが重要です。
③:管理コストを惜しまない
管理項目を増やすことはコストアップにつながります。
また、管理に費やす時間が増えることは、担当者の仕事量が増えることになります。
本腰を入れて取り組むには消極的になる理由が多くありますが、だからと言って手を抜くと、後で大きなしっぺ返しを受けることになります。
最初は、仕組みづくりや工程の総点検など、特に管理コストがかかりますが、品質や信頼は長年の実績を積み上げていくものなので、初期投資を惜しまない取り組みを推進しましょう。
作業者の意識面では、「やらされている感」にならないよう、源流管理のメリットや省略した場合の弊害など、必要性をきちんと周知した上で、組織として意識改革することが求められます。
やはり、組織全体で目標を共有することが、認識の乖離を解消する上で、真っ先に手を付けるべき課題と言えるでしょう。
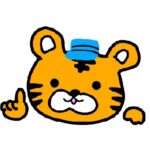
みんなで自発的に取り組もう
こてつ経験談
いつもと違う気づき
とある製品で不具合が出て、生産技術の担当として原因調査をすることになりました。
発生状況を調べてみると、特定の日に作られたものに集中しており、装置の異常であることが判明しました。
後になって分かったのですが、仲の良い現場作業者に聞いてみると、「その日は装置の調子が少しおかしかったんだけどねぇ・・」ということでした。
ほんの僅かな違いですが、動作に少しタイムラグがあり、何かいつもと違う雰囲気があったようです。
毎日見ているからこそ気づく情報はとても貴重であり、そこに不具合の種が潜んでいることも多いのです。
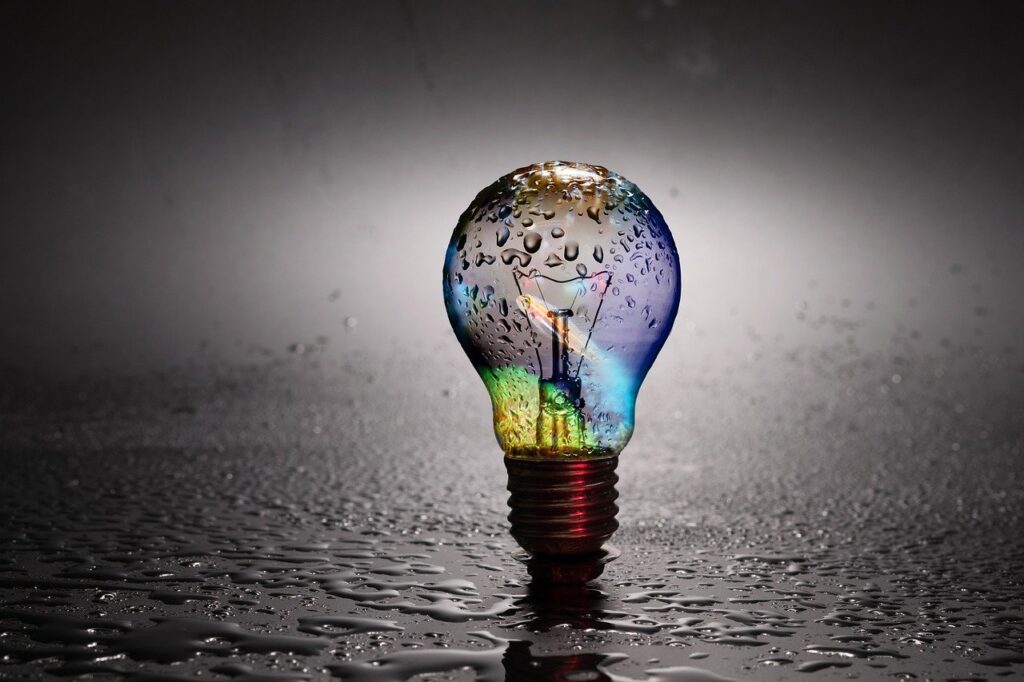
現場の声をきちんと拾う
さらに聞くと、実は異常の兆候が見られた際に、アラームを発していたとのことでした。
しかし、他の案件で手が回らない製造スタッフばかりで、特に何も処置がなされないまま、立ち消えてしまったのでした。
「現場の声にしっかりと耳を傾けよう!」というのは当たり前の話で、これを人員不足の中でどう対処するのか、仕組みの作り方が問題です。
例えば、違和感を覚えたら作業記録にメモとして残す、あるいは、作業者の気づきの感性を信頼して、とにかく一旦止めて状態を確認するなど。
異常発生時だけでなく、異常の可能性が見られた場合の対処方法もあらかじめ決めておくことで、些細な気づきの見落とし防止になります。
まとめ
- 源流管理
⇒上流工程の品質をきちんと管理すること - なぜ重要なのか
⇒①:応急処置では不具合が再発する(Quality)
②:下流になるほどロスコストが増える(Cost)
③:下流になるほど改修期間がかかる(Delivery) - 管理のポイント
⇒①:要素に分類して多角的に攻める
②:全部門参加で取り組む
③:管理コストを惜しまない
仕組みづくりや品質意識の浸透に時間がかかるかもしれません。
だからと言って労力を惜しんでいては、不具合で痛い思いをして、初めて源流管理の大切さに気づいてしまうことになります。
何かあった時に後手に回らぬよう、しっかりと工程を作り込んで、日頃から準備をしておきましょう。
コメント