今回は、源流管理の後編です。
前の記事では、管理の重要性とポイントを解説しました。
次のステップとして、具体的に何をどのように管理すればよいのか、お困りではありませんか?
この記事では、管理項目と着眼点の具体例を解説しています。
一つひとつの項目に対し、必要性や具体例の詳細を記載していますので、皆さんの考える実際の運用イメージに結び付けばうれしいです。
要素の分類
管理要素の分類には、5M+1Eの考え方を用いると効率的です。
4Mの要素として、Man(人)、Machine(機械)、Material(材料)、Method(方法)に、Measurement(測定)とEnvironment(環境)を加えたものです。
要素ごとに対処の事例を見てみましょう。
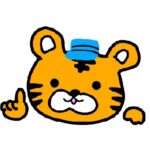
ここから管理項目の具体例を紹介するよ
Man(人)
教育/訓練
人(作業者)に関わる管理と言えば、第一に教育や訓練が挙げられます。
人の介在なしにモノづくりはできません。
全自動の製造ラインとは言っても、装置のオペレータや現場監督など、人によって成り立っていることには変わりありません。
一人ひとりの意識の持ち方で、些細な異常の発見や迅速な対応の仕方が変わるので、日頃から品質意識の向上に向けた教育や訓練を欠かさないようにしましょう。
ヒューマンエラー防止
そうは言っても、人間はミスをする生き物です。
失敗を責めるのではなく、そもそもミスをしない仕掛けや、大事故には至らないようにする仕掛けなど、仕組みづくりを心がけましょう。
このような未然防止の仕組みをポカヨケやフェールセーフと言います。
誰がやってもできる、あるいは、あらかじめ失敗した場合を想定して対処を決める、という重要な考え方です。
この他、mSHELL分析やA-KOMIKといった手法は仕組みづくりの参考になるので、合わせて未然防止の記事で詳しく紹介しています。
Machine(機械)
日常点検/定期点検
装置の健康状態の維持を心がけましょう。
特に自動機は、手作業の手間を省く大きなメリットがありますが、故障した場合の影響もその分だけ大きいです。
よくある事例としては、日常管理を省略したせいで装置の異常の兆候を見逃し、不良品を作り続けて後工程で発覚というパターンです。
故障リスクの高い項目や、品質への影響の大きい項目は、点検による生産の中断の影響を考慮しつつ、点検の要否を検討しましょう。
また、車検や年次点検のように、毎日ではなくても定期的に細部までチェックすることも必要です。
作業者だけで点検ができない場合は、装置メーカにオーバーホールを依頼することも、必要に応じて検討しましょう。
アラーム機能
装置が不調な状態で不良品をどんどん作りこまないように、自主検査の機能を盛り込むことも対策の一つといえます。
例えば、温度や荷重などのパラメータに対し、センサで常時モニタして何らかの異常で管理範囲から外れたら停止する機能です。
あるいは、パラメータ管理が難しい場合は、完成した製品を自主検査することも選択肢の一つです。
カメラや測定機器を装置に備えて、加工した直後に出来栄えの良し悪しを判断できれば、異常をすぐに見つけ出すことができます。
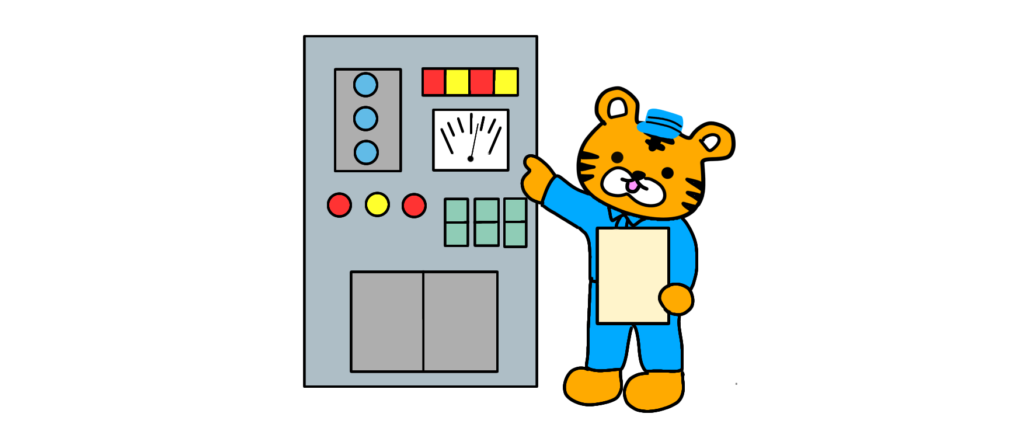
Material(材料)
購入仕様書/図面
仕入先の工程そのものを解決することも源流管理にあたりますが、自社内で管理を強化するには、きちんとした仕様書や図面の取り交わしに尽きます。
つまり、不良品や疑義のある材料(部品)の流入を防ぐことです。
購入仕様書や図面のトラブルで多いのが、規格に対する両社の認識の乖離です。
仕入先の方では、「この程度なら大丈夫」と判断したものが、自社ではNGという場合です。
認識に乖離がある場合、責任の所在で揉めることもあるので、最初に仕様書を締結する際にしっかりと認識を合わせることが重要です。
特に、数値で記載できない外観規格は注意が必要です。
お互い都合の良いように解釈しがちなので、限度見本などを準備して、誰が見ても同じ判断ができる状態を目指しましょう。
Method(方法)
作業標準書/QC工程図
作業方法に関する管理ポイントは、基本に忠実に正確に取り組むことです。
そして、その元となる作業標準書やQC工程図の不備が原因で生じるトラブルも多々あります。
例えば、条件設定の範囲の規定がない、手順が不明確、といった不備の事例があります。
これは、標準書やQC工程図を書く側の意識と、実際に見て作業する側の意識に乖離のあることが問題です。
事前に設計側と製造側で認識を合わせることはもちろんですが、一度、設計側の方で文面通りに作業して確認することをおススメします。
頭の中だけで作業を完璧にシミュレーションするのは難しいので、実作業をベースに文書化することで、抜け漏れを防ぐことができます。
変更点管理
生産性向上や不具合の再発防止の処置として、製造条件や作業方法を変更することがあると思います。
変更すること自体は、特に問題ありませんが、変更した行為を管理することが重要です。
気づいたら条件が変わっていたとか、良かれと思って日々やり方を変えたとか、品質管理の面では望ましくありません。
なぜなら、この変更がきっかけで、悪影響が出ないと言い切れないからです。
そのため、条件や方法を変更する際にも、変更点管理をきちんと実施しましょう。
まず、変更する理由(なぜ)、変更の時期(いつ)、変更の内容(どのように)、を明確にします。
次に、変更による品質への影響を洗い出します。
製品の機能・性能に影響を及ぼす可能性のある不具合、その不具合はどんな場合に生じるか、といった視点で整理します。
さらに、その不具合を起こさないために、どのような工夫をしたのか、あるいは必要な評価や仕組みは?と問いかけます。
このような手順を踏んで整理することで、変更の妥当性を精査できます。
これはDRBFM(Design Review Based on Failure Mode)と呼ばれ、設計変更の問題点を抽出するための手法として広く活用されています。
設計段階だけでなく、生産準備のフェーズでも活用できるので、ぜひ試してみてください。
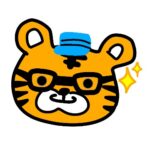
変更点管理は品質管理の頻出ワードだよ
Measurement(測定)
測定機器の校正
測定機器そのものの精度がイマイチでは、そもそも良し悪しを判断できません。
必ず定期校正を実施し、きちんとした精度が維持されているか確認を怠らないようにしましょう。
特に問題なのが、機器の精度が狂っていて、甘い方に判断してしまったケースです。
厳しい方であれば、最悪、工程内で歯止めがかかりますが、緩く見積もった場合、不良品の流出につながるからです。
製造設備だけでなく、検査設備についても、健康状態の管理を忘れないようにしましょう。
検査規格の見直し
曖昧な検査規格は、不良品の流出のきっかけを作ってしまいます。
仕入先との仕様書の取り交わしと同様、社内の検査規格に関しても、曖昧さは禁物です。
検査項目、検査方法、判定基準の妥当性を定期的に見直すようにしましょう。
Environment(環境)
温湿度管理
材料や装置は、温湿度に影響を受けるものがあるので、注意が必要です。
例えば、温度によって装置に微妙な寸法変化が生じる場合や、材料が吸湿する場合などが挙げられます。
そのため、取り扱う製品の性質にもよりますが、製造環境のパラメータとして、温湿度をきちんと管理することが望ましいです。
特に注意が必要なのが、保管条件です。
製造や検査は、一日ごとに区切りがある場合が多いので、その日の環境しか影響を受けませんが、保管は時間経過が伴います。
温度や湿度のわずかな変化しかない場合でも、時間を重ねると知らぬ間に影響が大きくなっていることもあります。
環境要因のパラメータと時間軸を合わせて管理することで、より安定した生産ラインを構築することに繋がります。
なお、時間を管理するということは、すなわち保管期限を明確にするということです。
何となく適当に決めるのではなく、評価結果や理屈に基づいた設定が求められます。
実際に長期保管した現品を準備できる場合は、その評価実績を期限設定の目安にできます。
数年単位での保管が必要で現実的でない場合は、加速試験なども選択肢として挙げられます。
実際の保管環境よりも過酷な温湿度に設定して短時間で結果を得るもので、必要に応じて検討に入れましょう。
異物管理
環境要因のもう一つは、異物管理です。
半導体や電子部品など、品質への影響が大きい製品に関しては、特に注意が必要です。
パーティクル(塵、ほこり)カウンタを用いて、異物の発生数の定常的なモニタを行うとともに、定期的に異物を回収して元素分析するなど、発生源を特定するための対応も重要です。
教育面では、5S(整理、整頓、清掃、清潔、躾)の意識を忘れずに、日頃から異物管理に対する改善活動を継続することで、人的側面からも管理強化を図ることが望ましいです。
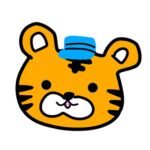
生産ラインの環境整備も忘れずに
まとめ
- 管理要素の分類と具体例
5M+1Eの要素に分けて分類すると整理しやすい - Man(人)
教育/訓練
ヒューマンエラー防止 - Machine(機械)
日常点検/定期点検
アラーム機能 - Material(材料)
購入仕様書/図面 - Method(方法)
作業標準書/QC工程図
変更点管理 - Measurement(測定)
測定機器の校正
検査規格の見直し - Environment(環境)
温湿度管理
異物管理
今回紹介した管理項目の具体例は一部ですが、このように色々な着眼点から管理することで、全部門でロバストな工程を作り上げていくことができます。
まずは、課題の整理や目標の設定など、一歩ずつでよいので、源流管理の取り組みを始めてみてはいかがでしょうか。
コメント