生産現場ではトラブルや不具合は付きものです。
日々、生産ラインを管理して、工程を作りこんでいても、トラブルを完璧にゼロに抑えることはできません。
そのため、トラブルを未然に防ぐ予防策の検討も必要なのですが、いざ発生した場合のトラブル対処能力を身につけることも重要です。
トラブルが発生して最初に実施する応急処置は、その後の被害の大きさを決める重要な役割を持ちます。
普段から対応の一連の流れを理解しておくことで、いざという時に迅速で適切な対応ができるようになります。
この記事では、応急処置の位置づけと対応の一連の流れについて、具体例を交えて解説しますので、皆さんの参考になればうれしいです。
応急処置
応急処置とは
さし迫った状況に合わせた臨時の処置のことで、事故が発生した際に、その場ですぐに行動に移す対応のことです。
負傷や病気に直面した際に、現場で対処する手当なども応急処置の一つであり、一般的な用語としてもイメージが付きやすいと思います。
品質管理の観点でも同じく、トラブルが発生した際に真っ先に対処する一次的な処置のことで、被害の拡大を最小限に抑えることを目的としています。
処置の手順
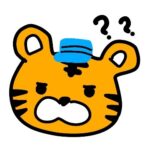
実際にどんな対処をしたらいいの
トラブル発生から応急処置の完了まで、一連の対処の流れを4つのステップに分けて紹介します。
具体的な工程のイメージが付きやすいよう、今回は「プレス加工部品で亀裂(ひび割れ)が発生する」というトラブル事例に沿って説明します。
Step①:工程停止の判断
トラブルが発生したら、真っ先に波及範囲を確認しなければなりません。
たまたま1個だけ異常(割れ)が発生したのか、連続的に発生したのか、あるいは途中でよい状態に回復したのか、発生状況を確認しましょう。
トラブルの原因が明らかで、対処不要と判断できる場合には、そのまま工程を止めずに生産を継続するケースもあります。
しかし、原因不明な場合や、連続的に発生して生産を継続できない場合は、すぐさま工程(生産)を止める必要があります。
止める判断が遅れると被害が拡大するので、この初動対応は非常に重要です。
作業者が独自に判断できない場合は、現場責任者の判断を仰ぎ、それまでは止めることが鉄則です。
いわゆる、「止める・呼ぶ・待つ」と表現される行動指針です。
ただし、あまりに敏感になり過ぎて、チョコ停レベルの軽微なトラブルまで、何でもかんでも工程を止めていては、まともに生産を継続できません。
品質優先の考え方はもちろん大前提ですが、生産性低下も影響が大きいので、品質・コスト・納期のバランスを考えた「適切な」判断が求められます。
Step②:工程の処置
次に、トラブルの発生した工程の処置を行います。
部品が割れるという事象に対し、例えば、プレス圧力を下げる、金型の隙間調整を行う、といった処置です。
部品が割れる→過大な力を受けている→過大な力を取り除けばよい→圧力や金型の調整を行う、といった流れで、問題を解消するための処置を行います。
いわゆる、対処療法のように、症状を軽減させるための治療に近いイメージです。
このような処置は、根本解決にはならないデメリットがある反面、即効性が一番のメリットで、短期的に一定の効果を出すことに長けています。
工程の処置を何も施さないと、すぐに同じトラブルが再発する恐れがあるので、暫定処置としてタイムリーに行動することは大変重要です。
Step③:不良品の処置
波及範囲の特定と工程の暫定処置が完了したら、次は製品の処置に移ります。
選択肢はいくつかありますが、少なくとも疑義のある状態で製造されたものなので、品質保証の面では、そのまま廃却するのが無難です。
あるいは、歩留りの面で許容できないのであれば、再製作や手直しという選択肢もあります。
さらにもう一つは、被害の程度が軽微で、品質面への影響がないことを保証できるのであれば、救済処置として、良品として扱うこともあります。
例えば、今回の事例ですと、ひび割れの発生箇所が限定的で、割れが短い場合、実使用上で問題なしと判断する処置です。
ここで一つ注意点として、仮に救済処置をして良品復帰させる場合でも、それ以外の通常の良品とは区別するようにしておきましょう。
あくまで、正常品とは異なる前提で製造されたものなので、最初は問題ないと判断しても、後々になって何らかの悪影響が出ないとも限りません。
きちんと救済処置をしたエビデンスとともに管理して、工程復帰させることが大前提です。
救済処置は、合格の判断を下してしまえば、良品と同じ扱いになるので、納期やコストなど余計な心配は不要なのですが、とにかく品質面で要注意です。
なぜ問題がないと言えるのか、進行性はないのか、確認した製品より悪いものは潜んでいないか、内部の状態は健全と言えるのか?など。
いろんな視点でのツッコミをすべて跳ね返せるよう、理論構築をしっかりとやっておかなければなりません。
すなわち、救済するのは、それだけのリスクを背負ってのことと認識しておくことが重要なのです。
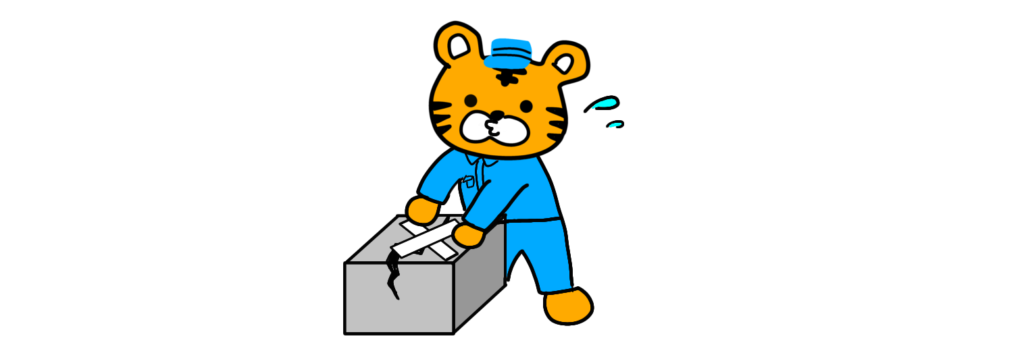
Step④:良品の処置
最後に、同じタイミングで製造した不良品以外の良品の処置を行いましょう。
判断が必要な一つは、すぐに後工程に流すかどうかです。
不良の原因が判明するまで保留処置として、後工程に流さない。
あるいは、健全なことが示されたので後工程に流す、といった判断を下します。
どちらが良い悪いと一概には言えず、品質保証が確実にできるかという観点で考えて、状況に応じて判断しましょう。
もう一つは、追加処置の必要性の判断です。
良し悪しが判断つかない場合は、例えば、追加の処理を施して問題ないことが確認できたものだけを後工程に流す手法です。
今回の事例でいうと、例えば追加で熱処理を施して、ひび割れの進行の無いことが確認できたら良品と判断する、といった考え方です。
いわゆる、スクリーニング(ふるい分け)の思想です。
疑義のあるものに対し、どのような品質上の懸念があるか考え、その懸念を払拭するために何を示せばよいか検討することがポイントです。
このように、良品に対しても、まずは疑いの目をもって選別の要否を考えることで、後工程への流出を抑えることができます。
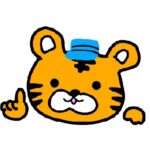
工程も製品も処置を忘れずに
こてつ経験談
喉元を過ぎれば
今回紹介した、「プレス加工部品で亀裂(ひび割れ)が発生する」という話は、私が実際に経験したトラブル事例をもとにしています。
そして、圧力や金型の調整で応急処置する内容も、まさに、その時の実例を題材にしています。
とにかく、トラブルが発生した直後は、周りの関係部門からのフォローがきつくなります。
当時、私は生産技術を担当していたのですが、製造、品質管理、生産管理の関係者から、「一刻も早く工程の復旧を」と注目を浴びることになりました。
こういう状況では、原因調査や恒久対策の検討にじっくりと時間をかける訳にはいかず、フットワークの軽い動きが求められます。
限られた時間の中で再現実験を繰り返した結果、圧力の調整で改善効果が見られることを確認し、生産の再開にたどり着くことができました。
そして、再開後の調子は大変順調で、応急処置の対応のまま、いったん終息することとなりました・・。
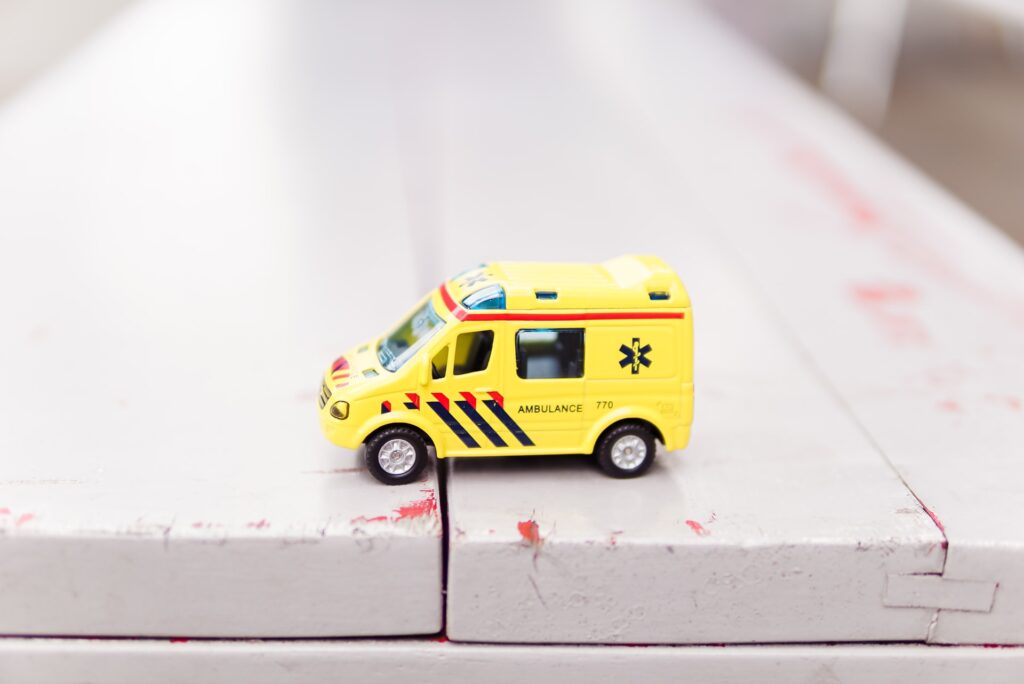
状況に応じた適切な処置を
結末の想像がつきますが、しばらく経過した頃、トラブルが再発します。
圧力調整で対処できたのは、当時の前提条件に限定した話であって、その後、いくつものロットを重ねるうちに、やがて対処しきれない時がやってきたのです。
あらためて、徹底的に原因を調査したところ、実は最初にトラブルが出た頃から、材料に変化があったことが分かりました。
根本原因は、材料にあったということです。
知らぬ間に割れやすい材料に変化していたものを、圧力調整で無理やり使いこなしていたため、辛うじて成立している状態でした。
ところが、色々なばらつきが重なり、対処できる範囲から逸脱した結果、再発に至ったという経緯です。
やはり、応急処置はあくまで一時的なもの、ということを忘れてはいけません。
短期的には工程の再開が最優先ですが、いったん落ち着いて時間が取れるようになったら、次のステージに進む必要があります。
その次のステージとは、根本原因の解明と恒久対策を行うことで、これが再発防止にあたります。
いったん収まったからOKではなく、きちんとその時の状況に応じた適切な処置を心がけましょう。
まとめ
- 応急処置とは
⇒トラブルが発生した際に真っ先に対処する一次的な処置のこと - 応急処置の目的
⇒被害の拡大を最小限に抑えること - 対応の4つのステップ
⇒Step①:工程停止の判断
Step②:工程の処置
Step③:不良品の処置
Step④:良品の処置
応急処置をおろそかにすると、後々になって傷口が悪化して甚大な被害につながる恐れがあります。
同じトラブルでも、誰がいつどのような初動対応を実施するかによって、その後の運命は大きく変わってきます。
救命処置と同様、いざという時のために、日頃から対応の流れを具体的にイメージできることが望ましいですね。
コメント